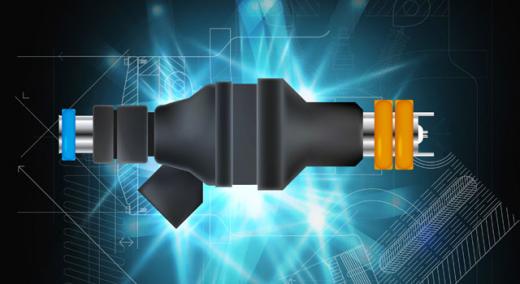
The manufacturing and production industries have rapidly evolved during the past 10 years, faced with significant challenges both in finding resources to run production and in manufacturing under tighter tolerances for surface texture and 3D feature dimensions.
ADVERTISEMENT |
The strict tolerances required in advanced manufacturing increases the need to have very repeatable metrology systems as part of the manufacturing line. Often a robot is used to exchange parts between the production tool and metrology equipment, leading to a fully automated process that removes some of the variability found with human operators.
Through the same automation path, results from a metrology tool are transferred to a central server that keeps track of trends or abnormalities using statistical process control (SPC) or other methods. This evolution is often referred to as Industry 4.0, where manufacturing is highly automated and directly integrated with metrology.
…
Add new comment