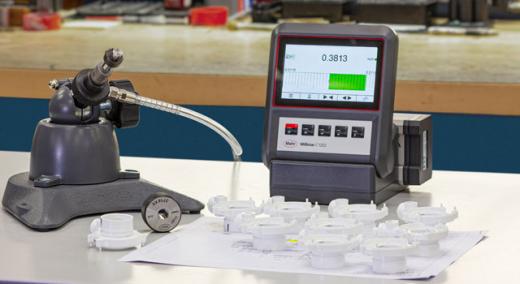
Air gauge measuring devices have given highly reliable and precise measurements since the 1940s. As the name suggests, an air plug or air ring gauge is a gauging probe that uses metered air under controlled pressure to sense the back pressure generated as it impinges on the surface of the part under measurement.
ADVERTISEMENT |
The controlled air flows through one or more nozzles or jets, and the resulting change in the airflow or pressure is measured by a precise sensing device. This pressure change is compared to the same measurement of a part with precisely known dimensions. The comparative measurement is then converted to an absolute measurement value for the part being measured.
To get the maximum benefit of this system of gauging, it’s important to understand air gauges and what factors contribute to their accuracy.
Air plug gauges are used for internal gauging, and air ring gauges are for external gauging. Usually, two jets face outward in an air plug gauge, and inward in an air ring gauge. They are symmetrically and precisely positioned on the diameter to balance the air flowing out. The amount of airflow under pressure depends on the particular readout system’s operating pressure and the size of the nozzles/jets.
…
Add new comment