All Features
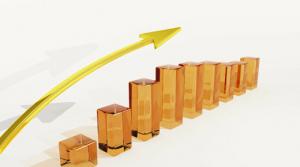
Jason Furness
In a previous column based on our recent book, Manufacturing Money (Amazon Digital, 2015), we explained how to maximize ROI. Here we describe some changes that business owners and managers can make on their way toward becoming a Black Belt in a manufacturing and distribution business.
Before any…
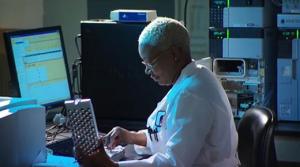
Michael Causey
Former FDA Chairman Robert Califf, M.D., stepped down on Jan. 20, 2017, and it’s not always easy to predict what the Center for Drug Evaluation and Research (CDER), or any FDA agency, will accomplish under a new chairman. Efforts at quality management could be affected by what appears to be an…
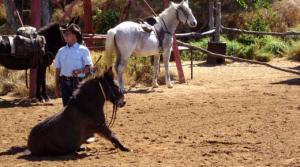
Harish Jose
As our new year unfolds, I wanted to write an article to remind myself of three pieces of advice. They are from Epictetus (55–135 AD), Marcus Aurelius (121–180 AD), and George Pólya (1887–1985). Epictetus and Aurelius are two famous Stoic philosophers of the past, and Pólya is a famous Hungarian…
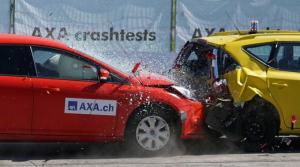
Donald J. Wheeler
What can be done when a test is destructive? How do we characterize measurement error? How can we determine if a test method is adequate for a given product or application? How can we check for bias?
All of the techniques for assessing the quality of a measurement system require us to make…
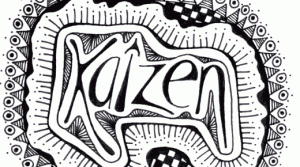
Kyle Pheland, Belinda Jones
Change is inevitable in every organization. Planned or not, forces inside and outside the enterprise can sometimes encumber a workforce and lead to nonvalue-added processes. Growing spurts, major technology implementations, or even small supply-chain organizational projects can present more issues…
Donald J. Wheeler
Who can be against apple pie, motherhood, or good measurements? This is why everyone stands up and salutes when we are told to maintain our measurement systems in good calibration. But what is good calibration? By what method will we achieve it? And how will we know when we have it?
One day I…
Davis Balestracci
Have you ever heard something like: “I’m committed to Dr. Deming’s approach [or Six Sigma or lean or TPS, it doesn’t matter], but executives don’t seem to listen anymore. All they do is keep interrupting my very clear explanations with, ‘Show me some results, then show me what to do.’ I was…
The United State Occupational Safety and Health Administration (OSHA) estimates that $60 billion is lost annually from workplace injuries and illness. Using the administration’s $afety Pays Program calculator, 20 carpal tunnel syndrome injuries will cost a company $1,260,000 in direct and indirect…
Joel Bradbury
Healthcare professionals have a long history of caring for their patients and improving the quality of their services. During the Crimean War (1853–1856), British nurse Florence Nightingale realized that the mortality rate of soldiers was far too high. A visionary statistician as well as a…
Bruce Hamilton
One of Shigeo Shingo’s popular status quo targets was engineers, whom he placed in three categories: table engineers, those who just sit around a table and talk about problems; catalog engineers, those who think the solution to every problem can be found in a catalog; and nyet engineers, those who…
Jason Furness
Editor’s note: This is an excerpt from Manufacturing Money (Amazon Digital Services, 2015) by Jason Furness and Michael McLean. See the article on the Manufacturship blog.
I n martial arts, the level of skill of the practitioner is recognized by the use of different colored belts to be worn with…
Davis Balestracci
Client A came to me for a consultation and told me upfront his manager would allow him to run only 12 experiments. I asked for his objective. When I informed him that it would take more than 300 experiments to test his objective, he replied, “All right, I’ll run 20.”
Sigh. No, he needed either to…
GBMP
Ellis Medicine is a 438-bed community and teaching healthcare system serving New York’s capital region. With four main campuses, five additional service locations, more than 3,300 employees, and more than 700 medical staff, Ellis Medicine offers an extensive array of inpatient and outpatient…
Harish Jose
Kaizen is often translated as “continuous improvement” and identified as one of the core themes in lean. Today I’m pondering the question: Can kaizen ever be bad for an organization?
In order to go deeper on this question, first we have to define kaizen as a focused improvement activity. The…
Ryan E. Day
Sponsored Content
You might say what Henry Ford did for the automobile, GE, Siemens, and Mitsubishi have done for the gas and steam turbine industry. Naturally, the tools and technicians of both sectors have had to evolve right along with the challenges of new technology and the ever-increasing…
Quality Transformation With David Schwinn
We recently had dinner with a wonderful friend and colleague, Michelle Guenther. During our meal, Michelle mentioned a conversation at work when she responded to a question with, “What I believe to be true is....” She said she frequently prefaces her answers to questions with that phrase and that…
Bruce Hamilton
The following is inspired by The Teachings of Don Juan (Washington Square Press, reprint 1985), an anthropological novel from the 1960s written by Carlos Castaneda, chronicling his travels with Don Juan, a Yaqui shaman. To crudely paraphrase, according to Don Juan, the road to knowledge is first…
Bob Emiliani
To this day, lean management has yet to enter the mainstream in business. It remains solidly on the fringe, despite great efforts by many people over many decades.
You almost never hear of lean management in the business press unless the article is written by an insider such as James P. Womack or…
Harish Jose
Uncertainty is all around us. A lean leader’s main purpose is to develop people so they can tackle uncertainty. There are two ways to tackle uncertainty: One is genchi genbutsu (go and see, or seeing for yourself), and the other is to employ the plan-do-check-act (PDCA) cycle, a method for…
Barbara A. Cleary
In a rapidly changing business environment, it’s sometimes hard just to keep up with everyday demands—never mind having time to develop new and better approaches to changing requirements, needs, or markets. Staying ahead of the curve sounds as if it might demand working longer hours, hiring more…
Quality Transformation With David Schwinn
It’s hard these days to miss the passion of people who support Donald Trump or Bernie Sanders, the steadfastness of the Tea Party, the outrage of the Occupy Wall Street group, and the frustration of young people who have so given up on the system that they choose not to vote. Most grievous is the…
Peter J. Sherman
As organizations become successful and grow, uncertainty is generally the enemy. Thriving organizations seek to eliminate variation and increase efficiency. They identify best practices and policies, and design standard operating procedures. Such efforts can make a business wildly efficient at…
Greg Fox
My recent beach vacation began with the kind of unfortunate incident that we all dread: killing a distant relative.
It was about 3 a.m. Me, my two sons, and our dog had been on the road since about 7 p.m. the previous day to get to our beach house on Plum Island, Massachusetts. Google maps said…
Afaq Ahmed, Yves Van Nuland
New technologies have empowered customers to seek out the best products and services at the lowest cost and shortest delivery times. Customers can compare price and delivery information as well as reviews about product quality. Thus, the importance of sustaining outstanding quality in order to…
Harish Jose
There is a concept in lean known as a “monument.” It refers to a large machine, piece of equipment, or something similar that can’t be changed right away, and so you have to plan your processes around it. This generally impedes the flow and frequently becomes a hindrance to lean initiatives. A…