All Features
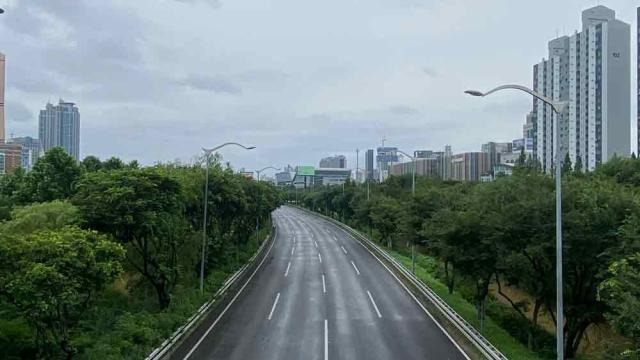
Gleb Tsipursky
The world has shifted in remarkable ways, and flexible work is an undeniable force reshaping professional life. But do remote and hybrid arrangements help the environment or lead to unintended consequences? A new study by Mark Ma at the University of Pittsburgh, Betty Xing at Baylor University, and…
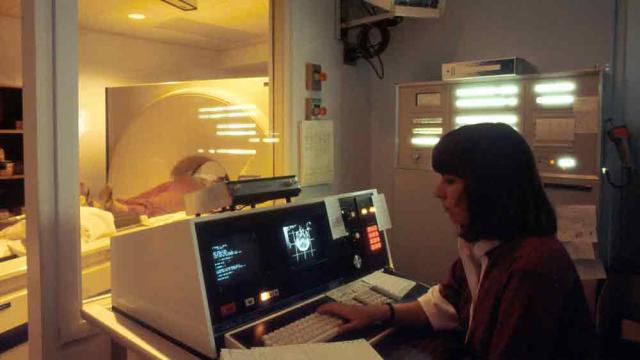
Etienne Nichols
As part of its effort to address the changing landscape around artificial intelligence (AI) in medical devices, the U.S. Food and Drug Administration (FDA) has recently released two new guidance documents on artificial intelligence-enabled device software functions (AI-DSF): • “AI-enabled device…
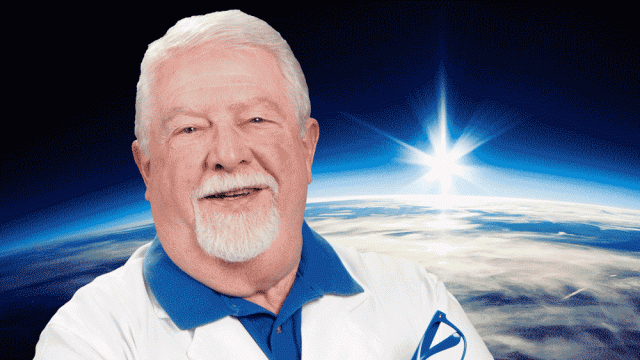
Jeff Dewar, Steven Garner, Quality Digest
Tom Taormina, CMC, esteemed quality consultant and long-time contributor to Quality Digest, has passed away. He is survived by his wife, Midge, and their three children. Recently, Taormina was working with Quality Digest and a consortium of others to design a certified training program for quality…
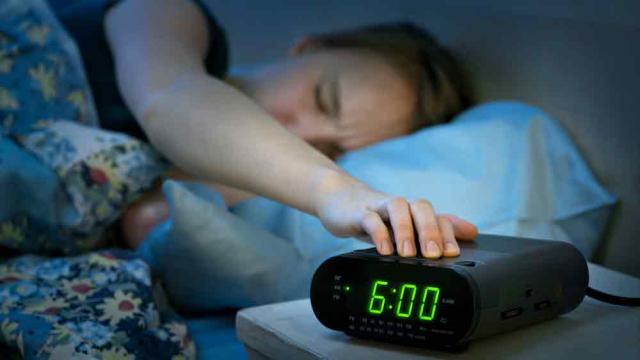
Mike Figliuolo
I heard an interesting twist on an old question the other day. People always ask the classic, “What keeps you up at night?” question. (By the way—don’t ever ask that of your interviewer during a job interview. It comes across as cheesy and stupid.) But while the question itself is a little corny,…
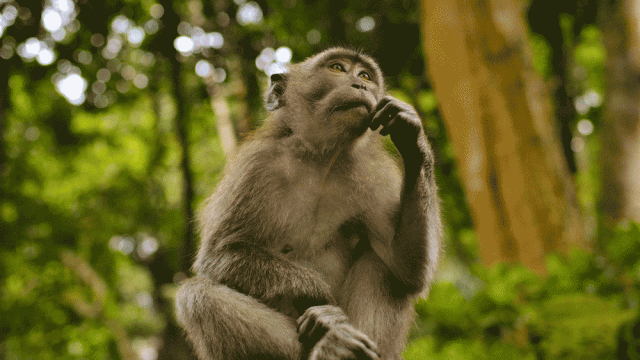
Peter Chhim
For decades, Six Sigma has been the gold standard in process improvement—a proven methodology for reducing defects, improving yield, and driving measurable operational gains. It delivered tremendous value in manufacturing, healthcare, and financial services. But in today’s shifting business…
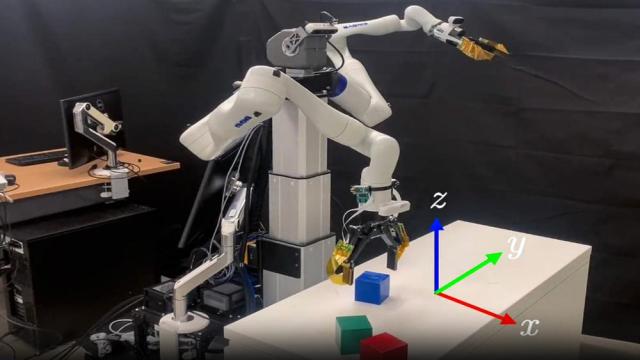
Adam Zewe
Ready for that long-awaited summer vacation? First, you’ll need to pack all items required for your trip into a suitcase, making sure everything fits securely without crushing anything fragile.
Because humans possess strong visual and geometric reasoning skills, this is usually a straightforward…
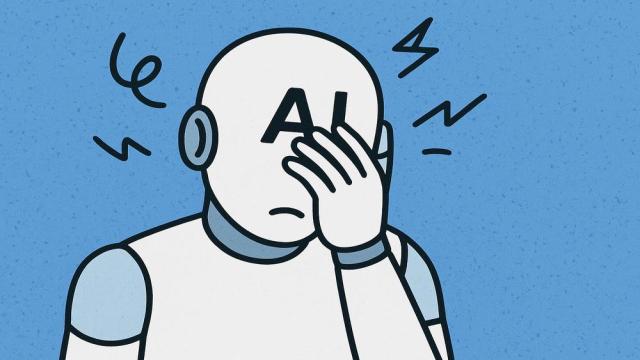
Cornelia C. Walther
On April 8, 2025, a driverless Zoox robotaxi misjudged an approaching vehicle, braked too late, and sideswiped it at 43 mph on the Las Vegas Strip.
One month later, the Amazon subsidiary issued a software recall on 270 autonomous vehicles and suspended operations while regulators investigated the…
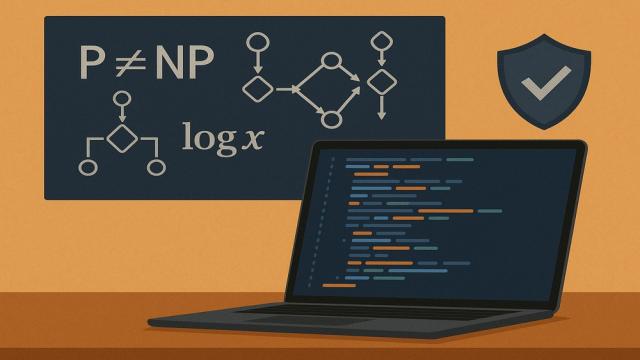
MIT News
On Dec. 21, 2022, just as peak holiday season travel was getting underway, Southwest Airlines went through a cascading series of failures in its scheduling, initially triggered by severe winter weather in the Denver area.
But the problems spread through the airline’s network, and over the course…
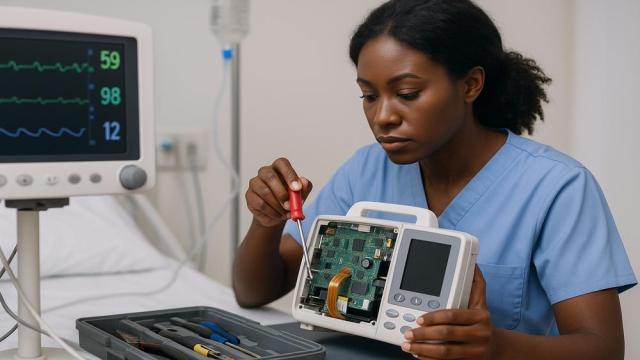
Heidi Drafall
Anyone who has cracked their smartphone screen or had a rapid oil change knows that sometimes the OEM isn’t the most affordable or convenient service option. Consumer flexibility, paired with lower-cost, high-quality options, is logical, whether it’s in the consumer market or in healthcare.
The…

Jones Loflin
This past weekend I engaged in one of my favorite activities as a beekeeper. I got to catch a swarm of bees.
If you haven’t seen it before, it’s wild. About half of the bees leave with a queen and set up somewhere temporarily while they’re looking for their new permanent home. In the case of this…
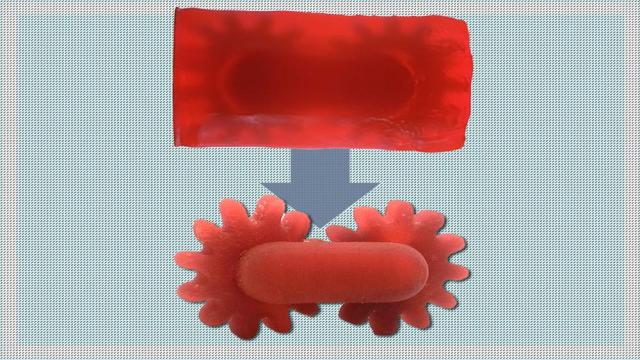
Jennifer Chu
Hearing aids, mouth guards, dental implants, and other highly tailored structures are often products of 3D printing. These structures are typically made via vat photopolymerization—a form of 3D printing that uses patterns of light to shape and solidify a resin, one layer at a time.
The process…
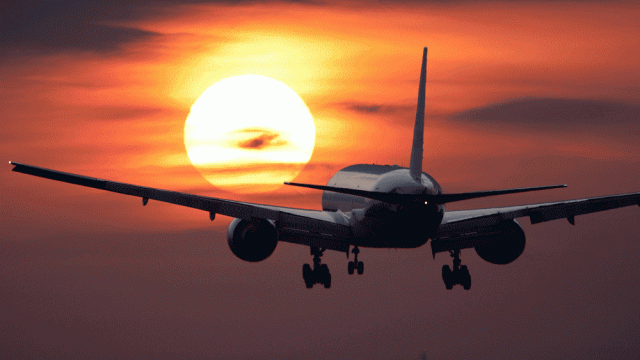
Scott Ginsberg
When quality failures go public, it’s not just your product on the line—it’s also your reputation, compliance status, and workforce morale.
From product recalls to OSHA citations, recent manufacturing disasters reveal a brutal truth: The real cost of outdated documentation isn’t just inefficiency—…

Mike Figliuolo
For as many words as we use, we’re terrible communicators. Voicemails are jumbled streams of consciousness. Emails are “text bombs” with no rhyme or reason. Presentations are nothing but crippling piles of slides. But don’t worry—here are three rules of three to make your communications clearer,…

Gleb Tsipursky
Remote work has become a game-changer for older individuals with disabilities, offering a solution that not only improves their employment prospects but also brings substantial economic benefits, according to a new study from the Center for Retirement Research at Boston College.
Before the…
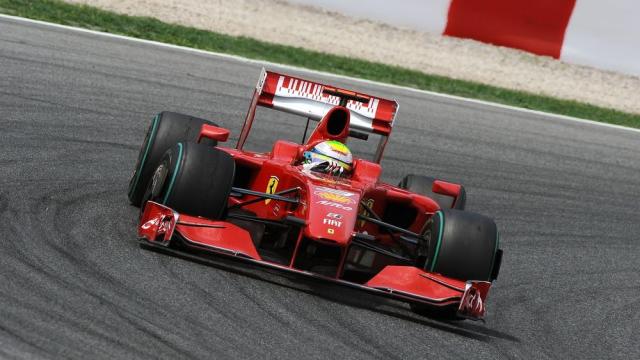
Seb Murray
In Formula One racing, slower drivers are expected to move aside when a faster car laps them. But some don’t give way so easily. They might wait for a spot that costs them less time, delay just enough to stay in their rhythm, or even make the faster driver fight harder to get past, throwing them…
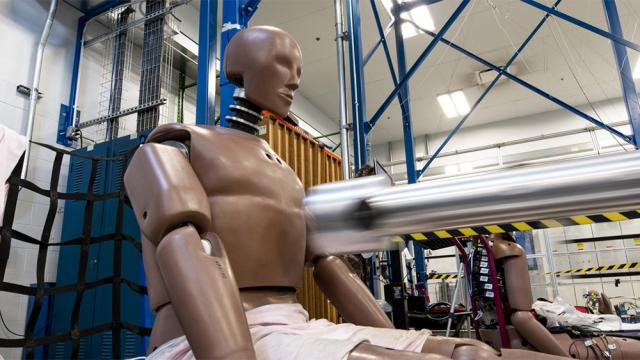
InnovMetric
Humanetics is the world’s largest manufacturer of anthropomorphic test devices (ATDs), commonly known as crash test dummies. The group has more than 1,000 employees across 21 facilities located around the world, with global corporate headquarters in Farmington Hills, Michigan.
Humanetics is…
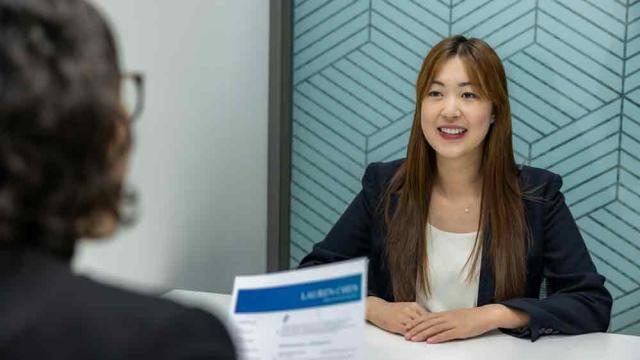
Conformance1
Amid uncertainty in manufacturing, AI adoption, labor market fluctuations, and salary disparities across industries and geographic regions, quality professional compensation can be difficult to calculate. Without current job-level salary benchmarks, quality professionals, from technicians to…
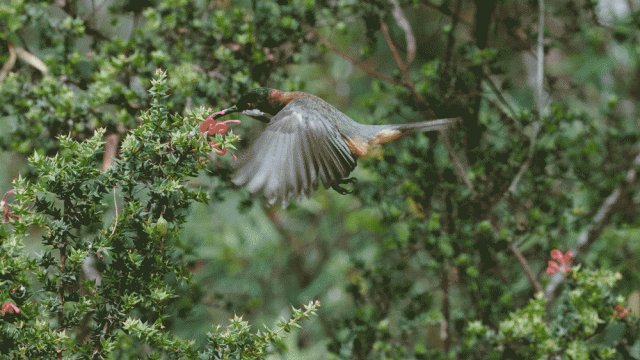
Rene Ymzon
When manufacturing tolerances shrink to the micron, and part geometries become increasingly complex, the margin for measurement error disappears. In this space—where even thermal drift or mechanical vibration can invalidate results—motion control becomes not just a component but a cornerstone of…
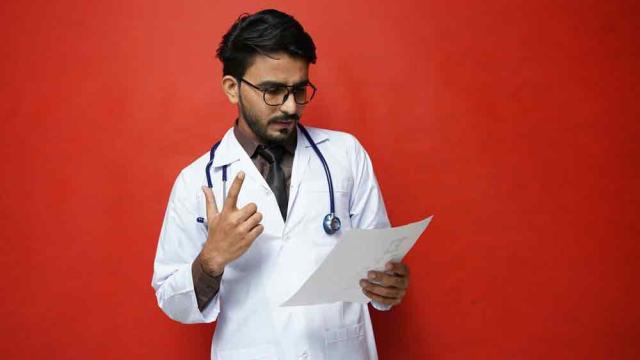
William A. Levinson
According to the U.S. News & World Report article “FDA Warns Sanofi of Manufacturing Irregularities at Key Facility” (Jan. 23, 2025), the pharmaceutical company Sanofi received a U.S. Food and Drug Administration warning letter “stating that FDA inspectors found irregularities with the facility…
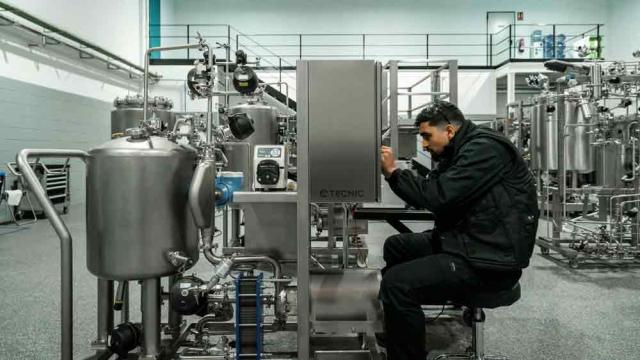
Bryan Christiansen
The cornerstone of efficient industrial and facility management, maintenance, repair, and operations (MRO) cover all activities related to equipment maintenance, procurement, upkeep, and inventory management. This includes spare parts, consumables, lubricants, cleaning supplies, safety equipment,…
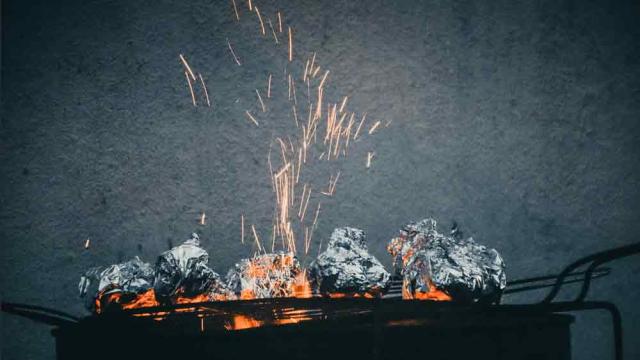
Donald J. Wheeler
For many hundreds of years, “If it ain’t broke, don’t fix it” has summarized the predominant approach to process operation. From the physician’s admonition to do no harm, to the slightly more positive aphorism that the squeaky wheel gets the grease, there is a common theme of differentiating…
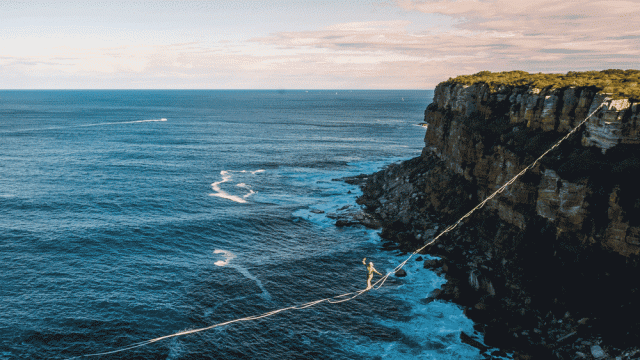
Harish Jose
I am a longtime admirer of George Spencer-Brown’s “Laws of Form.” In this article, I explore how his notion of reentry helps illuminate the paradoxes and blind spots in modern ideologies, especially the rise of xenophobia and extreme nationalism. These rigid ideologies depend on distinctions…
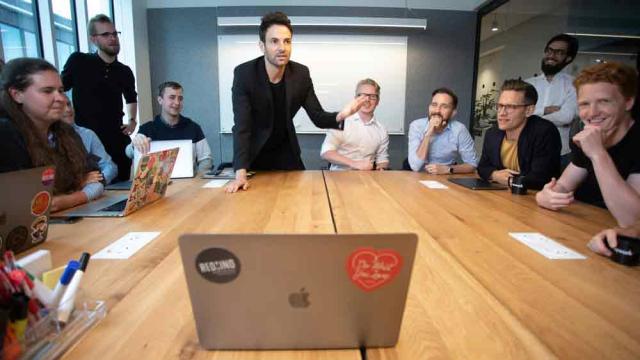
Mike Figliuolo
There’s an old army saying, “No plan survives first contact with the enemy.”
I’m sure some Navy or Marine guy out there will attribute this comment to their branch of service, but to be clear, it came from the Army.
Actually, the original of this paraphrased quote is widely attributed to Prussian…
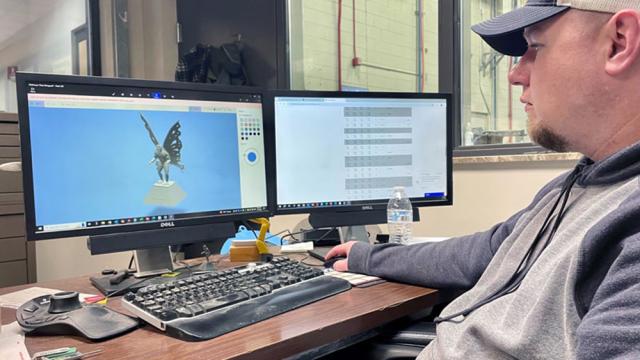
Creaform
The Marshall Advanced Manufacturing Center (MAMC) is a leading-edge resource facility dedicated to driving innovation and advancing manufacturing technologies.
Operating from West Virginia facilities in Huntington, South Charleston, and Point Pleasant, the MAMC is at the heart of groundbreaking…
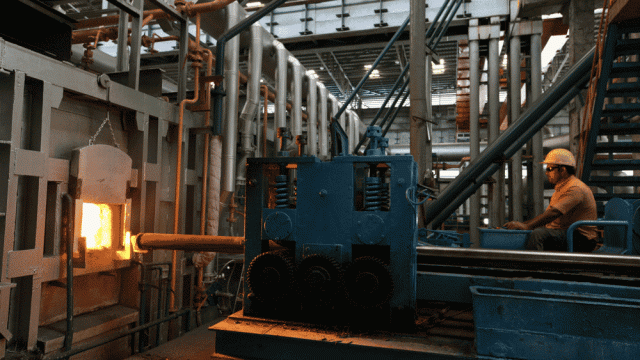
Nick Haase
When I talk with maintenance leaders, I hear urgency. Pressure is mounting. They’re being asked to cut costs, attract skilled workers, and embrace AI—and fast. Yes, pressure turns coal into diamonds. But constant pressure can wear down even the best teams. So for our 2025 State of Industrial…