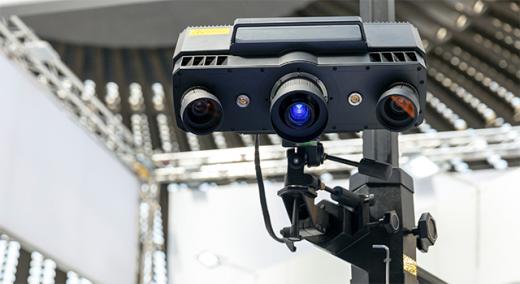
The main benefit of deploying artificial intelligence (AI) for quality inspection is a significant improvement in defect detection. However, the data generated and stored by inspection systems have the potential to deliver additional benefits, including major improvements in yield.
ADVERTISEMENT |
Anyone working in the world of quality inspection will be aware of the limits of manual inspection and the potential benefits of greater automation, including systems that use AI and deep learning algorithms. With recent advances in AI, the most sophisticated inspection systems available today can reduce the error rate to below 1%. In comparison, for manual inspectors a host of factors, such as fatigue and cognitive bias, means the error rate is usually closer to 10%.
Quality inspection sensors on the job
However, a significantly reduced error rate isn’t the only area where automation can have a significant effect.
…
Add new comment