All Features
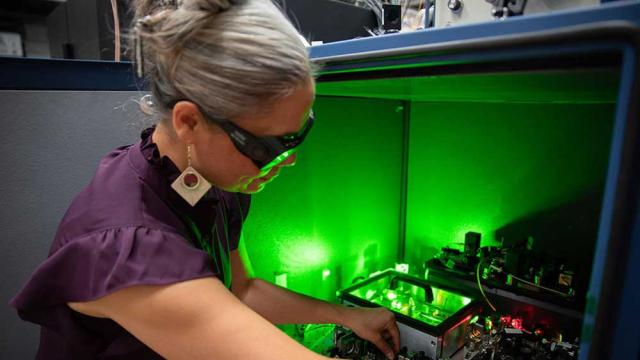
Tara Fortier
If you’ve heard or read about quantum mechanics, you may have seen it described as “weird.” Even the great Albert Einstein—one of the founders of quantum mechanics—called certain aspects of the theory “spooky.”
With its wave-like particles and particle-like waves, quantum mechanics certainly…
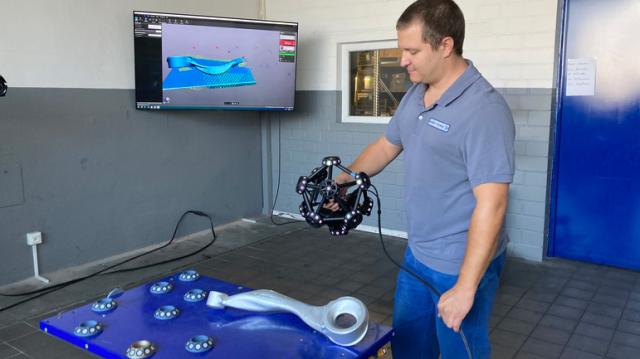
Creaform
For 185 years, Bharat Forge CDP has been a hallmark of expertise and craftsmanship in metal forging and forming. The German company is known worldwide as an innovative leader and trusted supplier to a wide range of industries, including automotive, rail transportation, and mechanical engineering…
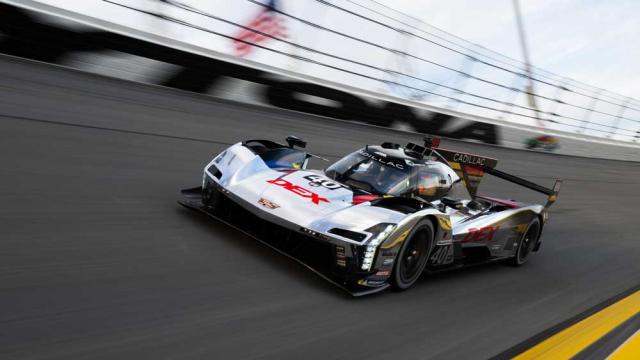
Creaform
Founded in 2007 by three-time World Sportscar Champion Wayne Taylor, Wayne Taylor Racing has quickly become one of the most recognized motor sports brands around the world.
WTR is indeed a powerhouse. It has secured numerous wins across an impressive range of iconic events and race series,…
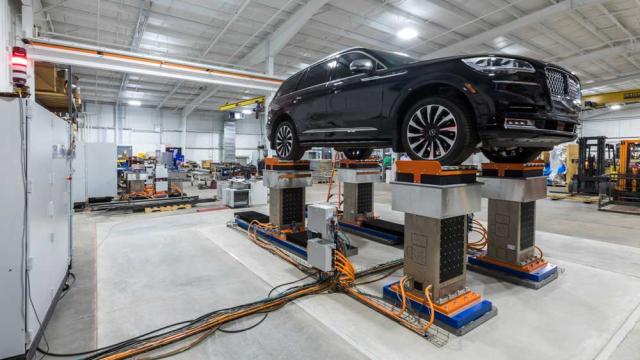
Siemens USA
Since the early 1980s, the automotive industry has used hydraulically actuated (servo-hydraulic) test systems to simulate operating speeds and road conditions for testing OEM components and fully assembled vehicles. These systems have helped unlock vast improvements in the quality, safety, and…
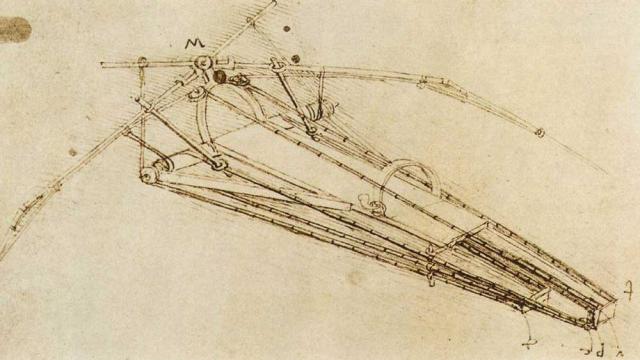
Yushiro Kato
Artificial intelligence (AI) is gaining momentum across a vast array of fields. Nearly everyone has tried or actively uses a form of AI, whether for personal or professional purposes. Many are finding benefits of the technology in industries that use large amounts of data that must be analyzed,…
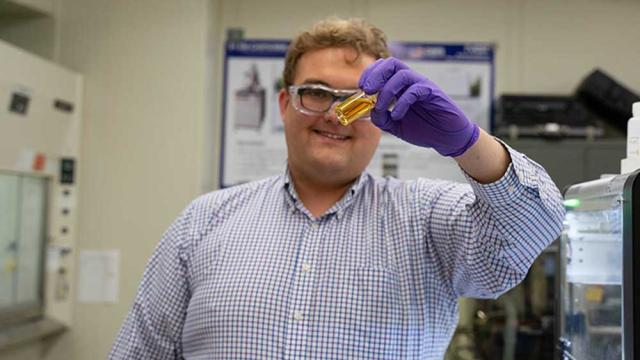
Peter Beaucage
Every time you squeeze toothpaste onto your toothbrush, spray perfume on your skin, or swallow a pill, you’re using the result of a carefully crafted recipe made in a lab. These are called formulations.
Formulations aren’t just simple mixtures—they’re complex arrangements of ingredients designed…
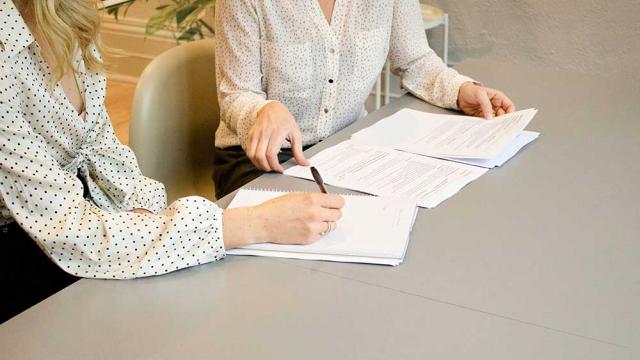
Donald J. Wheeler
In last month’s article, “ANOVA and the Process Behavior Chart,” we saw how both techniques use the same basic comparison to answer completely different questions. Here, we’ll look at a case history where both techniques were used.
A physical property of a mass-produced item was important to its…
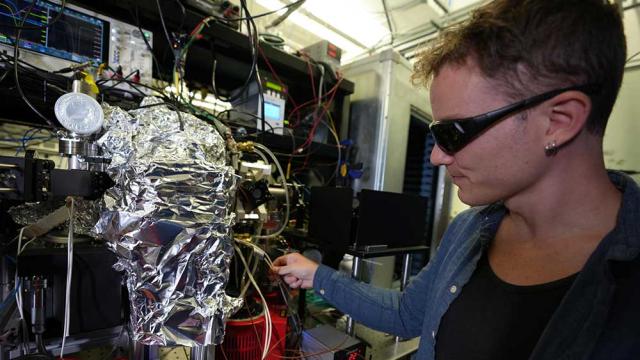
NIST
Scientists at the National Institute of Standards and Technology (NIST) have created a new thermometer using atoms boosted to such high energy levels that they are 1,000 times larger than normal. By monitoring how these giant “Rydberg” atoms interact with heat in their environment, researchers can…
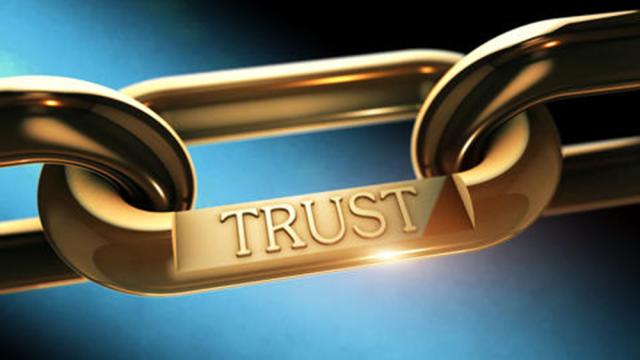
NIST
Without us realizing it, metrology and its associated standards and services play a big role in our daily lives. We buy groceries that are weighed or measured. Prepackaged products are weighed or measured during production. Medicine at the pharmacy is measured to make sure it contains the right…
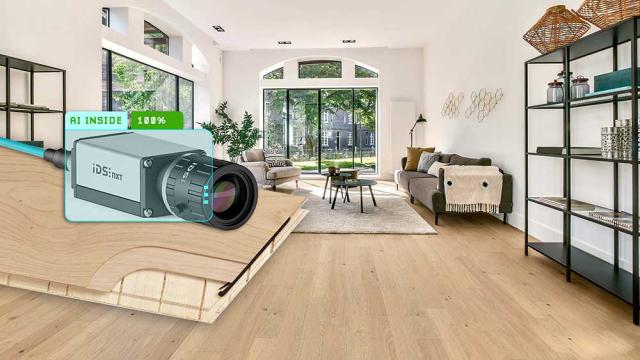
Sabine Terrasi
It creates a warm and inviting atmosphere. Its natural grain and color tones have a lively effect and add character to a room. We are talking about classic wood flooring—usually laminate, and optionally with a click system for easy installation.
Scheucher Holzindustrie GmbH, from Mettersdorf,…
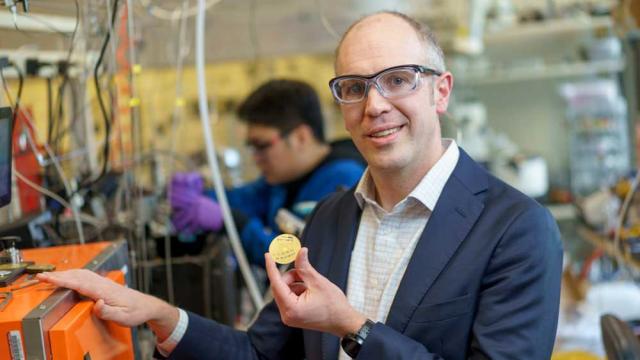
Anne Trafton
For many industrial processes, the typical way to separate gases, liquids, or ions is with heat, using slight differences in boiling points to purify mixtures. These thermal processes account for roughly 10% of the energy use in the United States.
MIT chemical engineer Zachary Smith wants to…

Ariana Tantillo
On June 18, 2023, the Titan submersible was about 90 minutes into its two-hour descent to the Titanic wreckage at the bottom of the Atlantic Ocean when it lost contact with its support ship. This break in communication set off a frantic search for the tourist submersible and five passengers on…
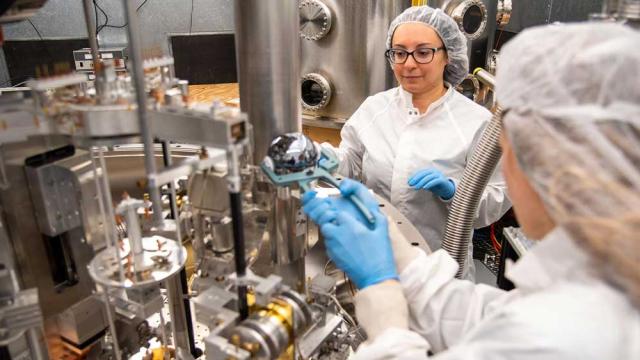
Ben P. Stein
NIST is unique as the national measurement science institute. We are the U.S. agency responsible for maintaining measurement standards, from the second to the kilogram.
We help ensure that these units of measure are consistent across our watches and our grocery scales. But this isn’t as…
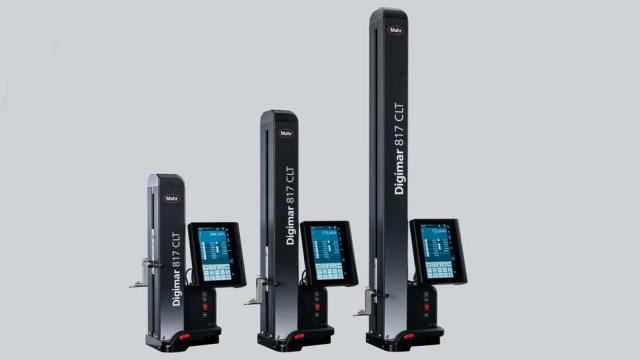
George Schuetz
The need for long-range height measurements has been around since the principles of layout work became a fundamental requirement in machine shops.
The first step in the manufacturing process is to lay out a piece by transferring a design or pattern to a workpiece. This is performed in almost all…
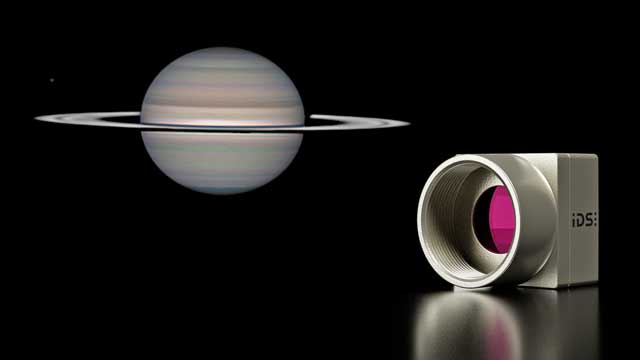
Silke von Gemmingen
Our solar system has fascinated mankind for thousands of years. Astronomical research is looking for answers to the big questions of human existence. How big is the universe? How did it come into being? Astronomers all over the world use telescopes to cast their gaze into space.
However, it’s not…
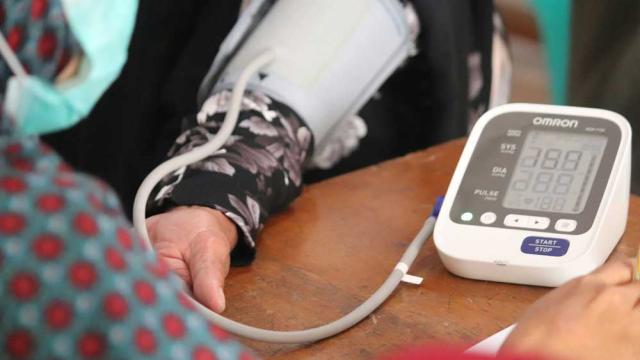
Etienne Nichols
Compliance with industry regulations and standards is a fundamental part of medtech. Without proper medical device compliance, companies risk patient harm, litigation, and reputational damage.
Fortunately, compliance with medical device regulations and standards is not an impossible task. A…
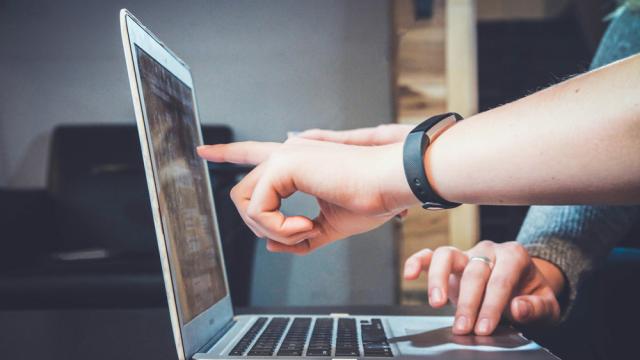
Gary Peacock
W ith the rapid digital transformation of manufacturing, including technologies like cloud solutions, digital twins, next-generation devices, automation, and AI, the role of metrology is poised for a transformative evolution. What can we expect from new quality systems, and how is the metrology…
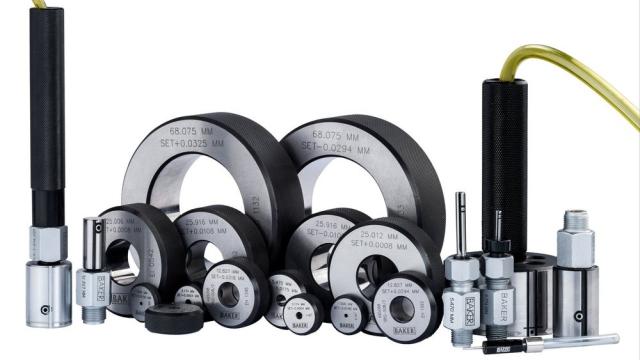
Anil More
The jet in pneumatic dimensional (or air) gauging is the mechanical part of the sensing probe—air plug gauge, air ring gauge, air caliper gauge—through which compressed air is directed onto the part under measurement.
In its simplest form, we have two jets working in tandem facing in opposite…
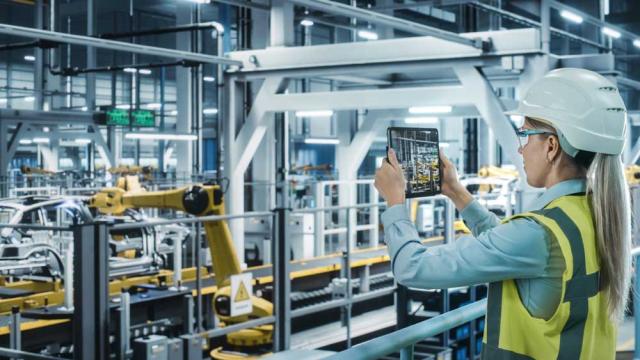
Michael Sharp
Welcome knowledge seeker! Do you feel dazzled and awed by the great potential of artificial intelligence (AI)? Perhaps hesitant or lost when terms like convolution, deep learning, or autoencoder are thrown around? Well, fear not, for you’ve come to just the right place. You don’t need to be a…
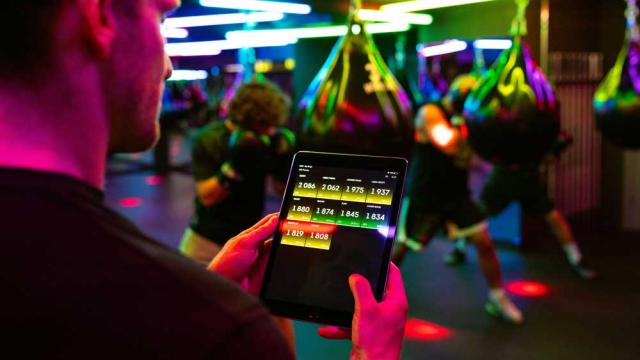
ISO
From small family-run companies to tech giants, the business world is changing at an unrelenting pace. Amid a constantly evolving economic landscape and sometimes dizzying technological advances, one thing remains constant: the need to maintain the highest level of quality.
Whether manufacturing a…
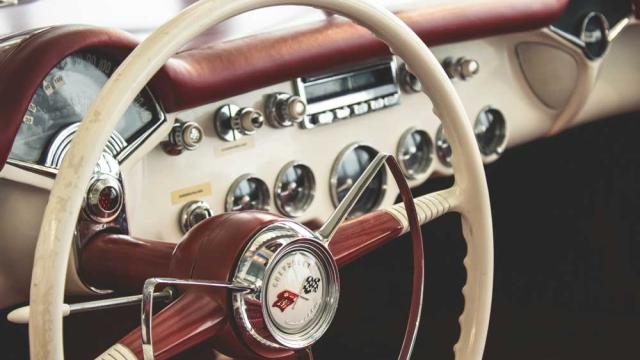
Donald J. Wheeler
Managers are commonly fed a diet of report-card data. These data have usually been aggregated into summaries, averages, and totals to characterize the big picture. As useful as such summaries can be, they can also be an obstacle to an effective analysis. Here, we’ll learn how to avoid this obstacle…
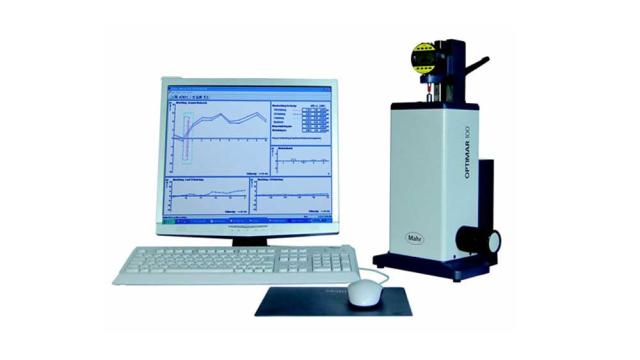
George Schuetz
Whether you’re a small machine shop or a large multimillion-dollar manufacturing giant, there’s no doubt you use dimensional gauges to maintain the standards for quality in your production.
The accuracy of these dimensional measuring instruments must be periodically checked to ensure that they’re…
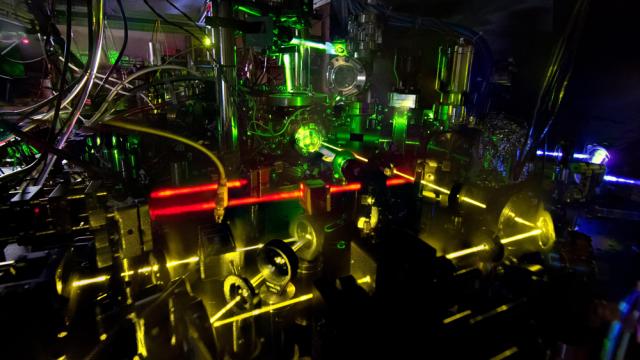
Gabriel Popkin
Time: We all have a sense of it, an innate feel for it. We see it and use it every day. If you’re like me, the first thing you do in the morning is check the time on your phone to see if you need to get out of bed or if you can close your eyes and catch a few more z’s.
Once you’re up and moving,…
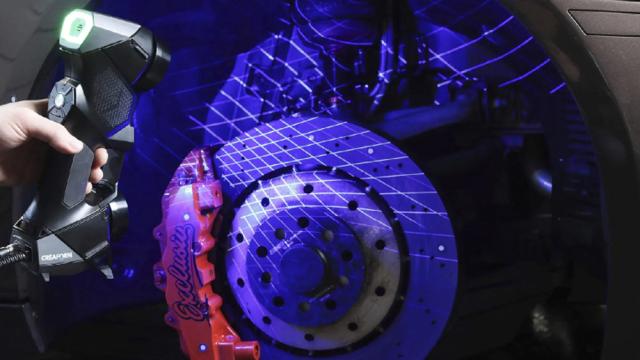
Creaform
In today’s market, it seems like all 3D scanners have similar specifications, as if manufacturers look at their competitors’ data and use the same numbers. Data sheets, marketing videos, and even product appearances all look comparable, making it difficult to distinguish quality based on technical…
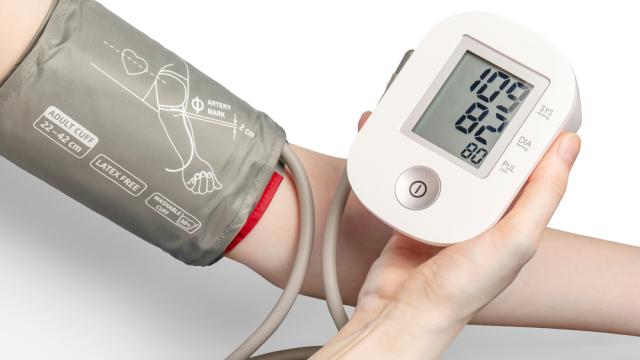
Chris Rush
While clinical trials are the gold standard for generating clinical data to use as evidence of your medical device’s safety and effectiveness, they are by no means the only way to gather clinical evidence.
Real-world data (RWD), which typically come from routine healthcare delivery or…