All Features
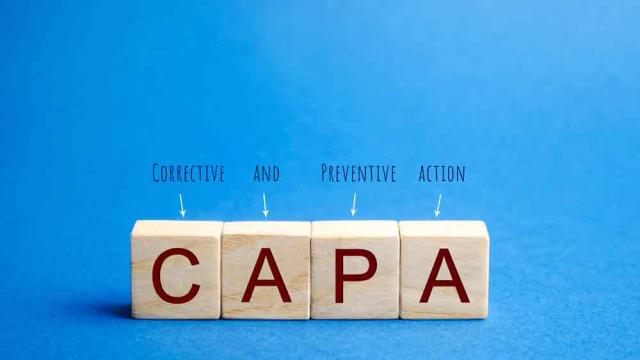
Etienne Nichols
The corrective and preventive action (CAPA) process is one of the most important elements within a medtech company’s quality management system (QMS). The goal of the CAPA system is to identify, address, and prevent systemic issues that could compromise product safety, regulatory compliance, and the…
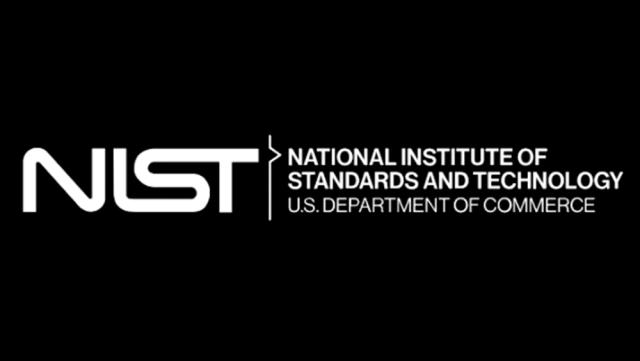
NIST
Using an electron beam to image the tiniest of defects and patterns on microchips, the scanning electron microscope (SEM) has long been a mainstay of the semiconductor industry. But as the industry continues to miniaturize chip components—essential for computers, implantable drug dispensers,…
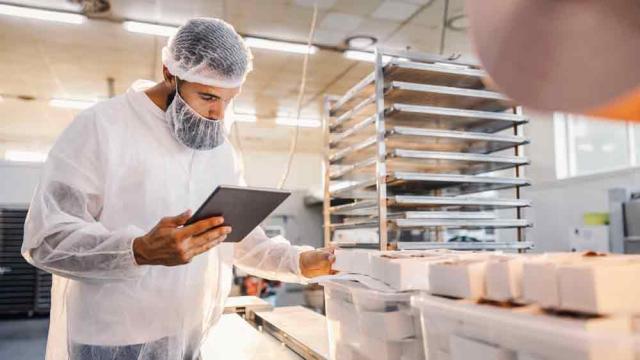
Prasant Prusty, Arundhathy Shabu
A global food safety and quality certification, BRCGS (British Retail Consortium Global Standards) initially focused on food safety but now comprises various sectors such as packaging, consumer products, and retail. It aims to ensure that businesses maintain high standards of safety and quality…
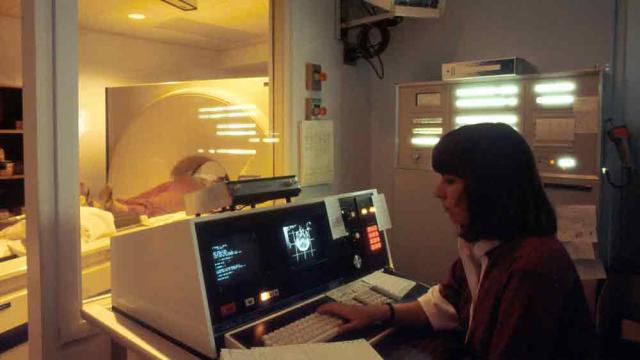
Etienne Nichols
As part of its effort to address the changing landscape around artificial intelligence (AI) in medical devices, the U.S. Food and Drug Administration (FDA) has recently released two new guidance documents on artificial intelligence-enabled device software functions (AI-DSF): • “AI-enabled device…
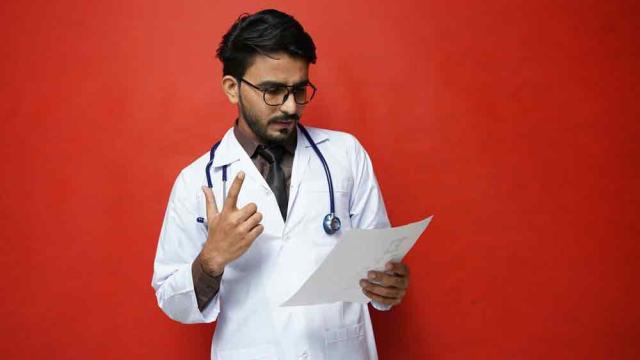
William A. Levinson
According to the U.S. News & World Report article “FDA Warns Sanofi of Manufacturing Irregularities at Key Facility” (Jan. 23, 2025), the pharmaceutical company Sanofi received a U.S. Food and Drug Administration warning letter “stating that FDA inspectors found irregularities with the facility…
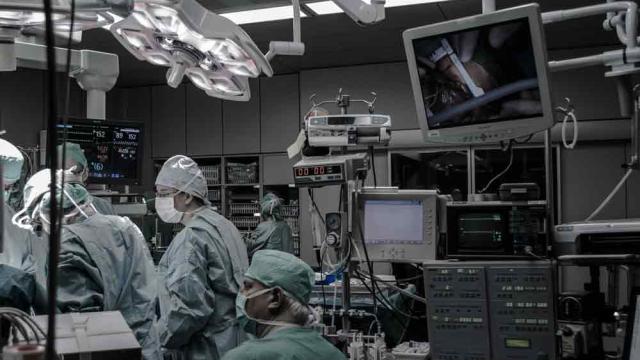
Matt McFarlane
One of the key findings in Greenlight Guru’s 2025 Medical Device Industry Report was that economic uncertainty is playing a large role in the decisions medical device companies make this year.
The report surveyed more than 500 medical device professionals across quality, regulatory, product…
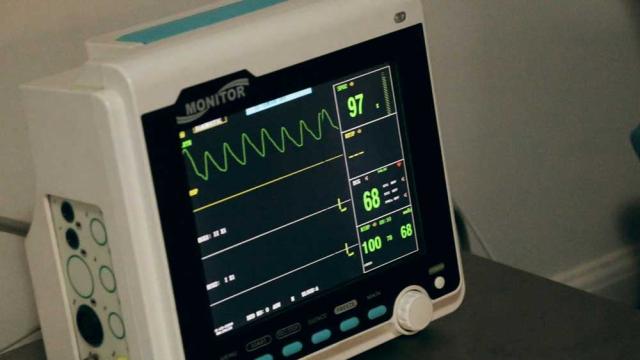
Matt McFarlane
The medical device industry is growing. Data from KPMG predict that global annual sales will rise by 5% per year to reach just under $800 billion by 2030. New technology, new opportunities, and, as always, the promise of improving patient outcomes around the world are major drivers of growth within…
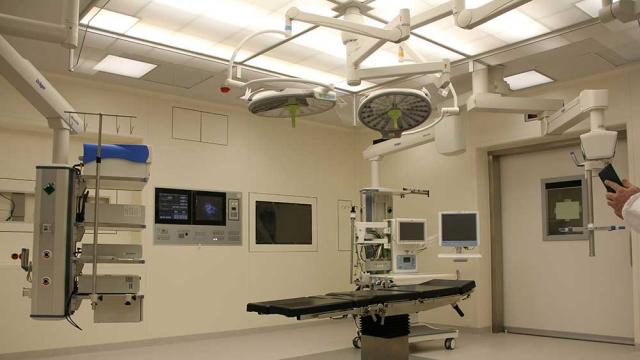
Etienne Nichols
Have you ever wondered what your medtech company looks like from the point of view of a U.S. Food and Drug Administration investigator? Well, this is your chance to find out.
Greenlight Guru invited Vincent Cafiso, a former FDA investigator, to the Global Medical Device Podcast to share his…
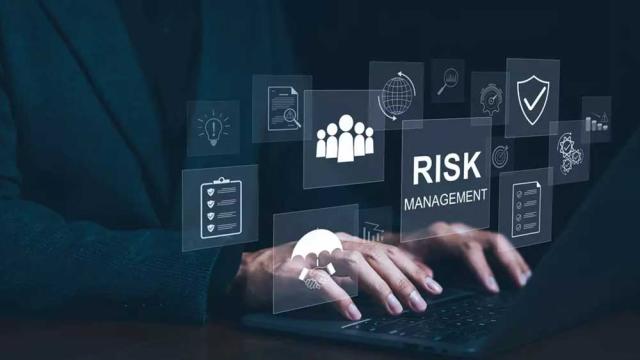
Stephanie Ojeda
Quality risk management (QRM) has become a crucial tool for ensuring regulatory compliance worldwide. It plays a central role in ISO management system standards and regulations, as well as the EU Medical Device Regulation (MDR/IVDR), FDA 21 CFR 820, and ICH Q10 in the pharmaceutical and biotech…
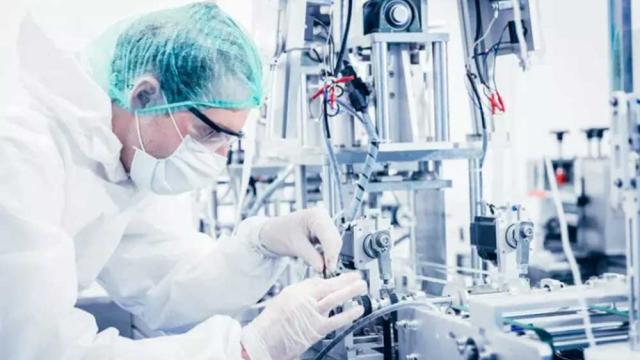
Stephanie Ojeda
In April 2018, the U.S. Food and Drug Administration (FDA) approved the first artificial intelligence-powered diagnostic system, a software program used to detect diabetes-related vision loss.
Since then, the industry has seen explosive growth of AI in medical device manufacturing, which is…
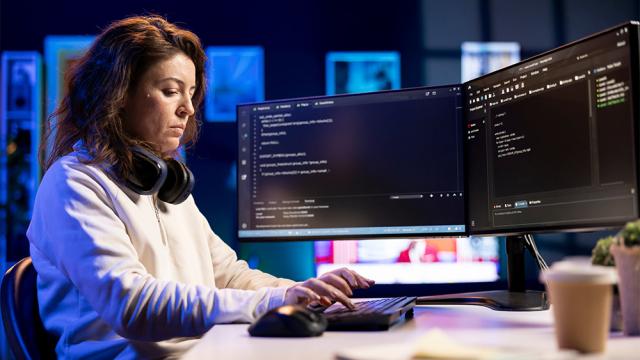
Ilana J. Sprongl
Back in 2023, only 15% of businesses had adopted AI-augmented software testing tools. By 2027, that number is expected to leap to 80%. The reason behind this rapid adoption is clear. The complexity of modern software and products is skyrocketing, and with it, the risks associated with quality…
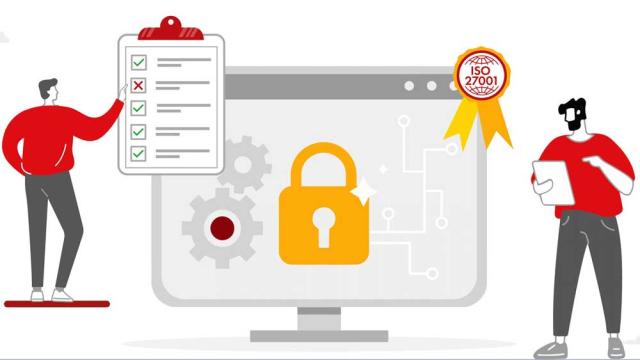
4C Consulting
ISO 27001 is a globally recognized standard for establishing, implementing, maintaining, and improving an information security management system (ISMS). Successfully implementing ISO 27001 can provide tremendous benefits, such as ensuring data security, building trust with customers, and meeting…
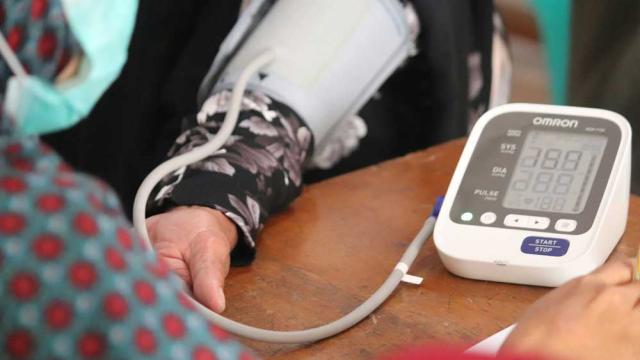
Etienne Nichols
Compliance with industry regulations and standards is a fundamental part of medtech. Without proper medical device compliance, companies risk patient harm, litigation, and reputational damage.
Fortunately, compliance with medical device regulations and standards is not an impossible task. A…
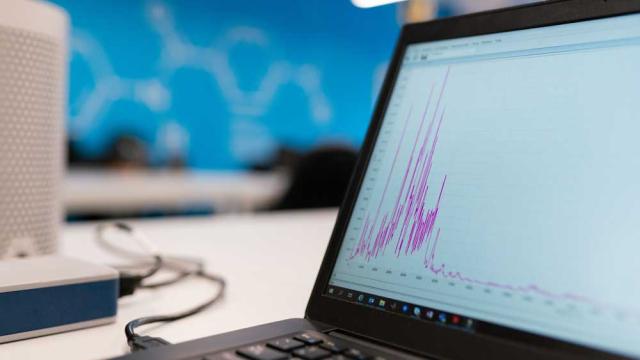
Victoria Alestra
In regulated industries like pharmaceuticals, medical devices, and food manufacturing, compliance is crucial for operational excellence. A validated quality management system (QMS) is key to maintaining this compliance. Let’s explore how QMS software streamlines validation and ensures regulatory…
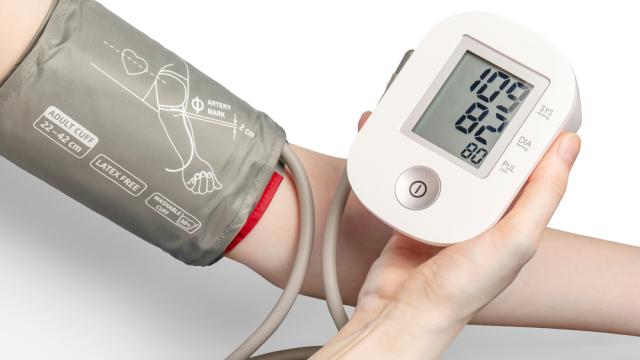
Chris Rush
While clinical trials are the gold standard for generating clinical data to use as evidence of your medical device’s safety and effectiveness, they are by no means the only way to gather clinical evidence.
Real-world data (RWD), which typically come from routine healthcare delivery or…
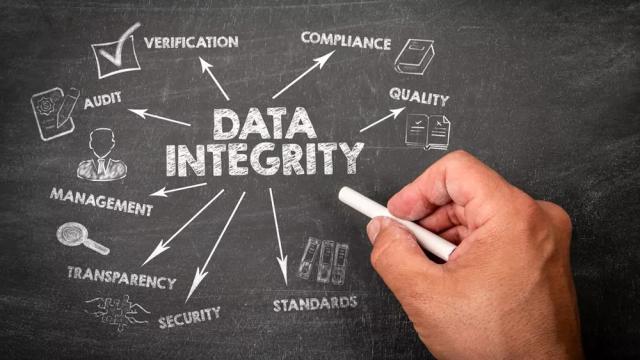
Stephanie Ojeda
In the highly regulated world of life sciences, data integrity isn’t optional; it’s essential. The ALCOA principles—attributable, legible, contemporaneous, original, and accurate—provide a foundational framework for ensuring data are reliable and trustworthy.
With the rise of digital…
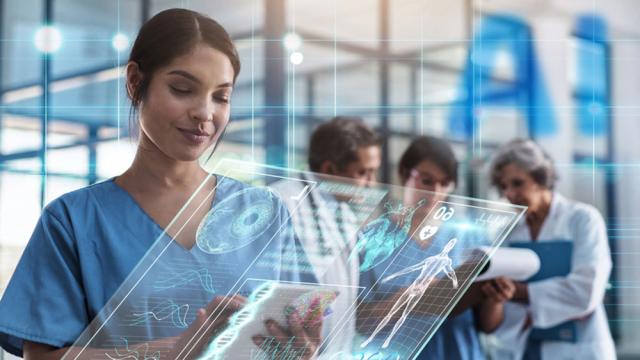
Zach Winn
Most doctors go into medicine because they want to help patients. But today’s healthcare system requires that they spend hours each day on other work—searching through electronic health records (EHRs), documenting, coding and billing, gaining prior authorization, and evaluating services—that often…
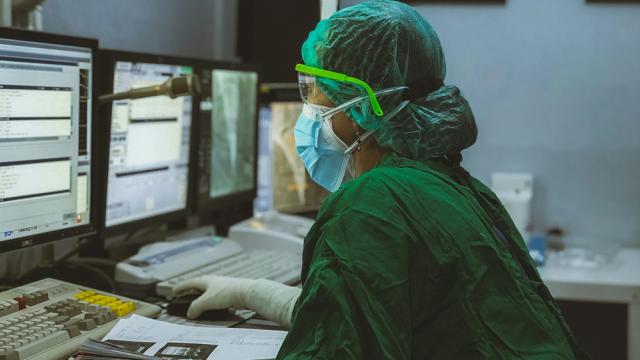
ISO
Cybersecurity has become increasingly critical in the digital age as organizations across all sectors face growing threats from cybercriminals.
Imagine that hackers breached a small healthcare practice through “phishing”—sending a scam email and gaining access to sensitive patient data, including…
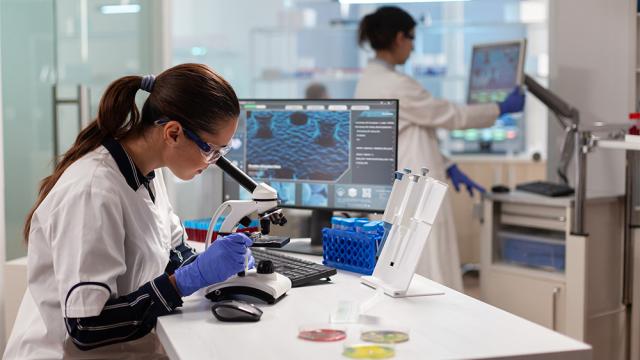
Saurabh Joshi Shripad
Before the ICH Harmonized Tripartite Guideline Q9—“Quality risk management”—was introduced in 2005, the pharmaceutical industry was evolving but lacked a structured, scientific, and systematic approach. Various stakeholders, including the industry, regulators, and patient rights groups, recognized…
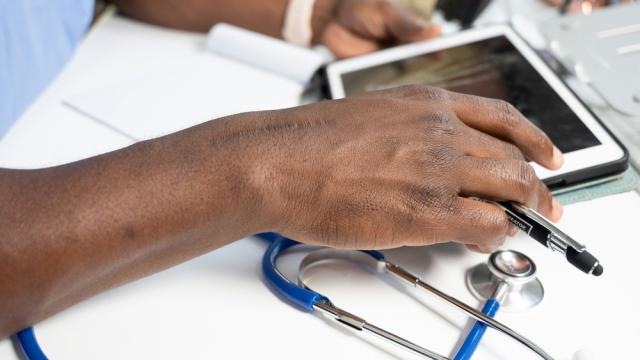
Laura Velásquez Herrera
With its roots in compassion and humanity, the healthcare sector might seem an unlikely place for artificial intelligence (AI) to play a big role. Yet as we look deeper into the complex processes that build our medical systems, we uncover a multitude of ways that AI could revolutionize patient care…
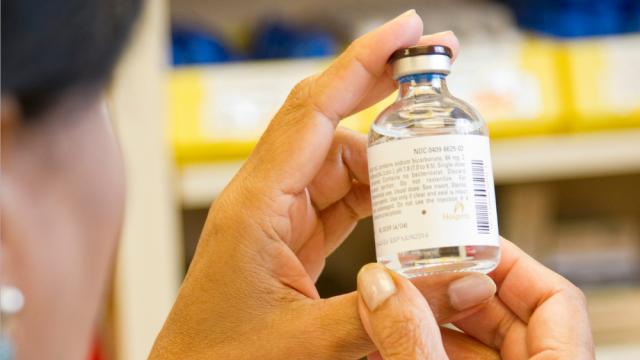
James Chan
The U.S. Food and Drug Administration (FDA) is the country’s chief agency for regulating the manufacture, marketing, and distribution of critical consumer goods including food, cosmetics, medical devices, biological products, and pharmaceuticals. The FDA provides direct oversight of the businesses…
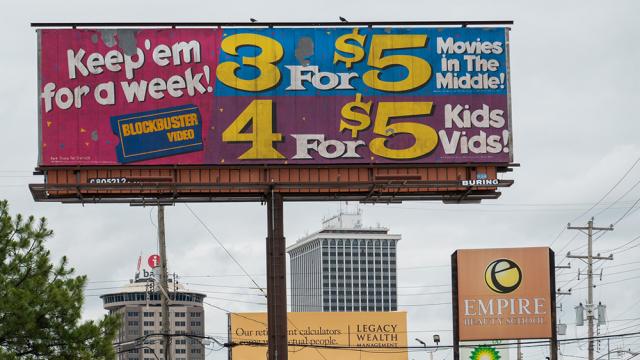
Robyn Coward, Brian Brooks
This year, the Medical Device Innovation Consortium held an Excellence in Quality Summit where it was promised that participants would receive a “unique opportunity to learn adoptable cutting-edge practices to maximize the impact of investing in quality across [their] total product life cycle.”…
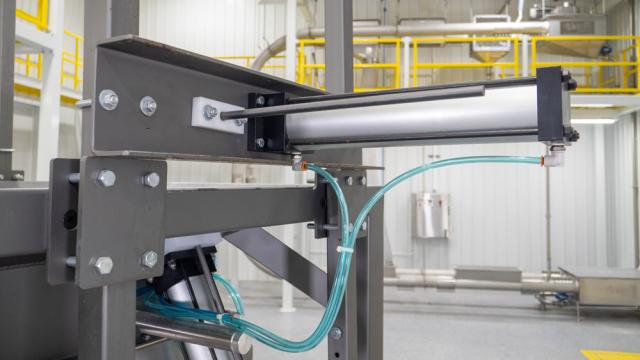
Del Williams
In food processing, bulk-bag discharge systems are used to transfer food ingredients such as flour, sugar, and spices from bulk bags to mixing and blending equipment. However, when not designed or installed properly, bulk discharge systems can become a production bottleneck.
Complicating the issue…
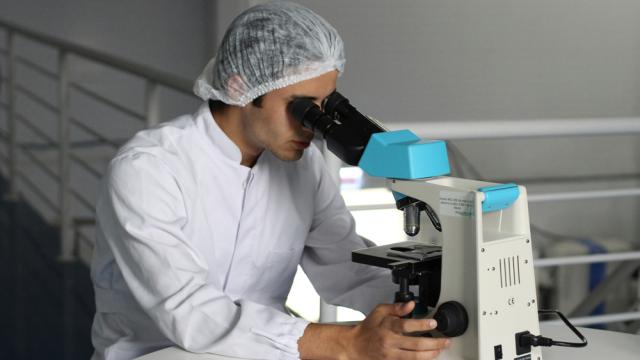
Etienne Nichols
On Jan. 31, 2024, the U.S. Food and Drug Administration (FDA) released its final rule for the new Quality Management System Regulation (QMSR).
The new QMSR is the result of aligning the current good manufacturing practice (cGMP) requirements of the FDA’s quality system regulation (QSR) with the…
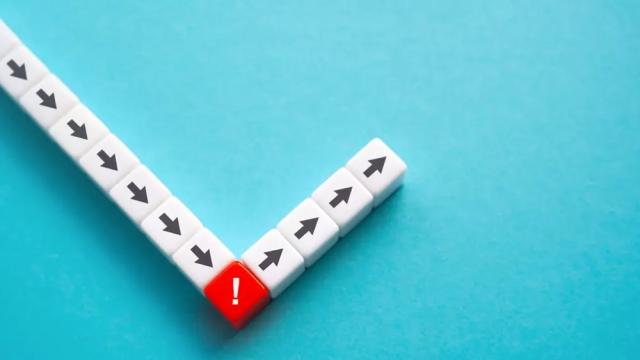
Stephanie Ojeda
There’s no question about it: Should an auditor or inspector visit your facility, one thing that will certainly be under the microscope is your corrective and preventive action (CAPA) system.
CAPA management is a recurring theme in U.S. Food and Drug Administration (FDA) warning letters, a fact…