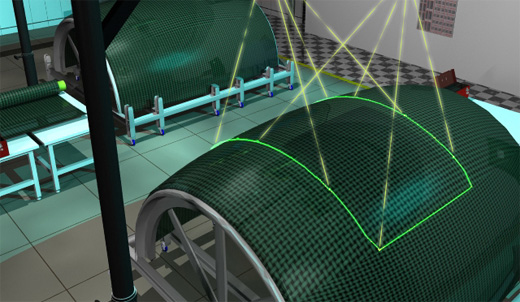
Sponsored Content
Building airplanes and spaceships poses some of the most unique engineering and manufacturing challenges mankind has ever encountered. Fortunately, you don’t have to build rockets to benefit from rocket science. Manufacturers of most any product can improve their efficiency and profitability by studying some of the approaches the aerospace industry takes to overcome production obstacles such as waste, rework, and engineering changes.
ADVERTISEMENT |
SWaP-C factors
Composite-using organizations such as Spirit, GKN, Boeing, Airbus, Albany Engineered Composites, and SpaceX do not tend to share proprietary processes, but they do share common hurdles when it comes to engineering and manufacturing. Aerospace—and all other manufacturing verticals—must consider size, weight, power, and cost. And they must factor those elements into the scheme of a complete system or product.
…
Add new comment