Content by Ryan E. Day
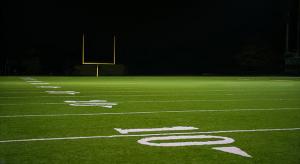
Tue, 03/15/2022 - 12:03
Business is changing at a faster rate than ever before, forcing companies to find ways to adapt and pivot. Keeping the entire organization aligned with current goals can be a daunting task, but surviving and thriving depends on it.
One popular…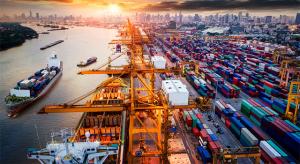
Mon, 02/14/2022 - 12:03
ISO 9001:2015, Clause 6.1 introduces the term “actions to address risks and opportunities,” as a replacement for the standard’s previous term, “preventive actions.” The juxtaposition of “risks” and “opportunities” seems to imply a relational nature…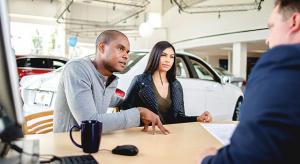
Mon, 01/31/2022 - 12:03
Chickens come home to roost, and canaries meet their demise in coal mines. But hey, we knew there was a high probability of each happening eventually, right? However, when a black swan shows up with severe impact and consequences, everyone is caught…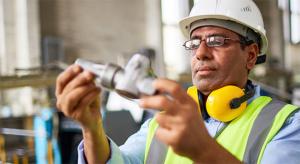
Thu, 01/13/2022 - 12:00
Quality Digest (QD) was born 40 years ago. Birthed as Quality Circle Institute (QCI), the organization was conceived as a consultancy focused on bringing the success of quality control circles at Lockheed to organizations that were beginning to…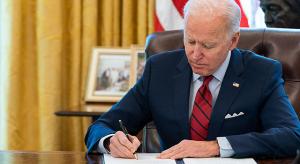
Thu, 11/04/2021 - 12:03
‘By the authority vested in me as President by the Constitution and the laws of the United States of America, including sections 3301, 3302, and 7301 of title 5, United States Code, it is hereby ordered as follows....”
Why do these words make me…
Mon, 10/11/2021 - 12:03
Aquiline Drones Corp. (AD) quips that, “All roads lead to AI.” Recent developments in artificial intelligence (AI) integration make that statement hard to argue against, and the astute application of AI to AD’s cloud-based services also makes a lot…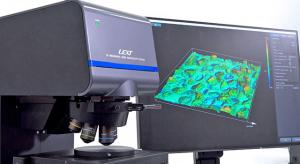
Thu, 09/16/2021 - 12:02
Manufacturing is a very competitive business where high-quality products are expected. And some clients require extremely tight surface measurement tolerances, so being competitive means investing in tools that can satisfy customer requirements.
The…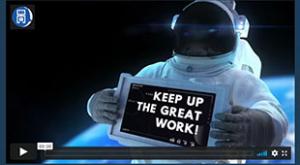
Wed, 08/18/2021 - 12:00
It is estimated that in 2021, the average person watches more than 100 minutes of online video every day. But is that relevant to your B2B marketing efforts?
“The vast bulk of this video consumption is marketing content,” says Maury Rogow, CEO of…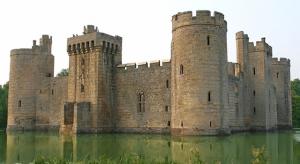
Tue, 07/27/2021 - 12:03
With the migration to remote and hybrid work during the last year, cyberattacks have increased at a rate of three to five times compared to pre-Covid. No big surprise that, for many businesses, virtual private newtworks (VPNs) have become standard…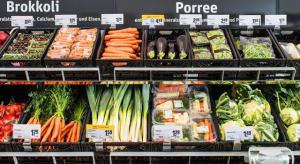
Tue, 06/08/2021 - 12:03
Automation in the fresh produce sector is standard fare these days. What may not be so standard are the containers that get the produce from farm to market. The quality of produce containers has a direct impact on the quality of the produce—and…