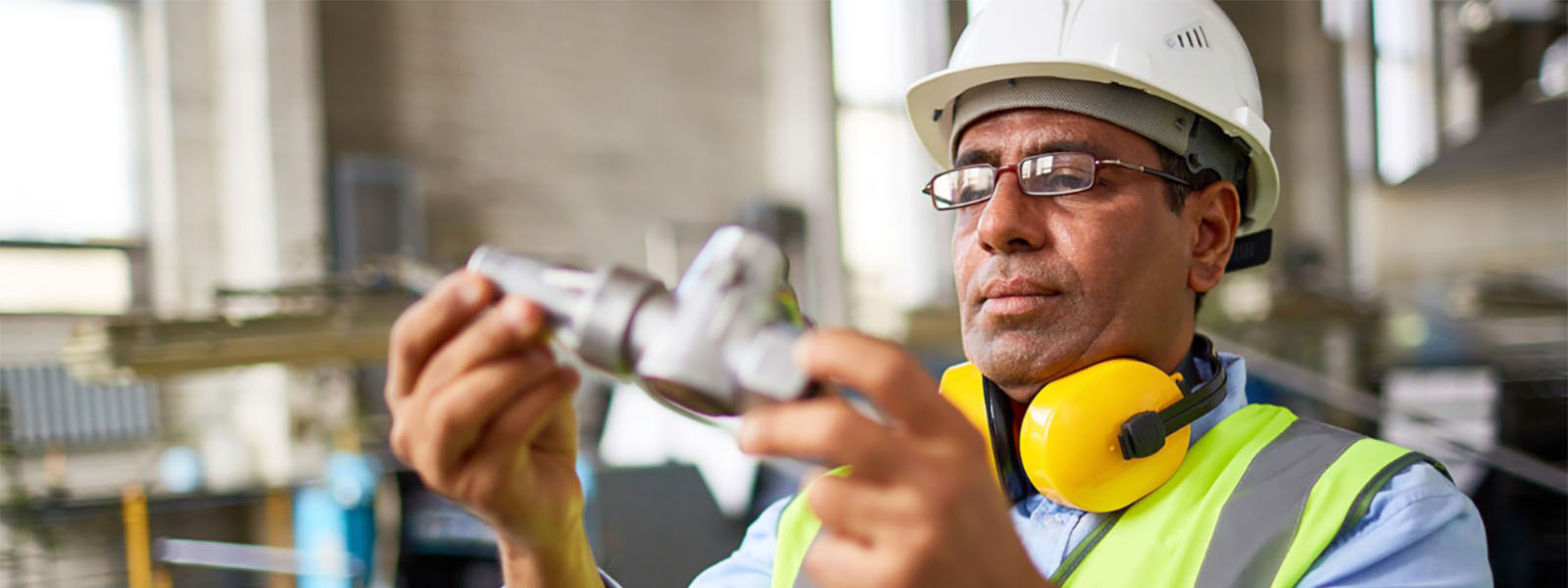
Quality Digest (QD) was born 40 years ago. Birthed as Quality Circle Institute (QCI), the organization was conceived as a consultancy focused on bringing the success of quality control circles at Lockheed to organizations that were beginning to awaken to the importance of employee involvement in the improvement process. But times change and ideas evolve, and QCI became QD to better represent the broader quality industry, especially the movement toward international standards. In fact, the very definition of quality, and its role in manufacturing and business, has been something of a bone of contention all along.
Definition of quality
One might assume the definition of quality to be a simple affair. Apparently, this is not the case. According to the Merriam-Webster Dictionary:
“Essential Meaning of quality = How good or bad something is, i.e.,
• Pollution affects air/water quality
• The restaurant serves food of high quality. [= the food at the restaurant is very good]
• The dress material is of poor quality. [= the dress material is not good]
A high level of value or excellence:
• Wine of quality [= very good wine]
• They offer quality at a reasonable price.”
…
Add new comment