Content by William A. Levinson
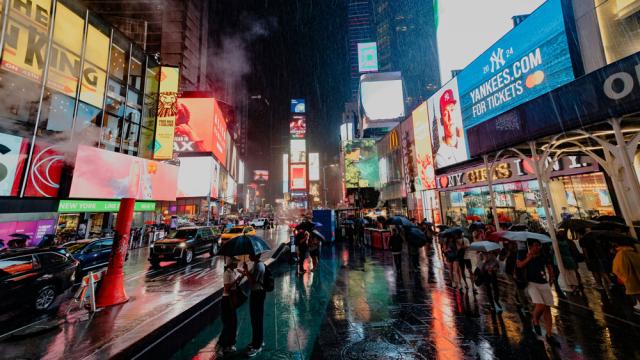
Wed, 08/20/2025 - 12:03
I recently needed to have a hot water expansion tank installed in my house. The first plumber who came to mind is widely advertised on local radio. The company’s online reviews suggest that they do good work, but one added that they are expensive—…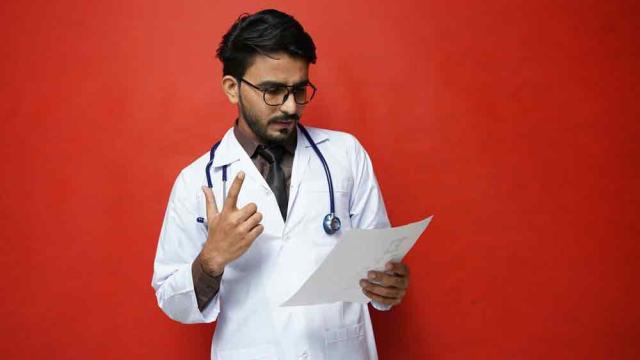
Tue, 06/17/2025 - 12:03
According to the U.S. News & World Report article “FDA Warns Sanofi of Manufacturing Irregularities at Key Facility” (Jan. 23, 2025), the pharmaceutical company Sanofi received a U.S. Food and Drug Administration warning letter “stating that FDA…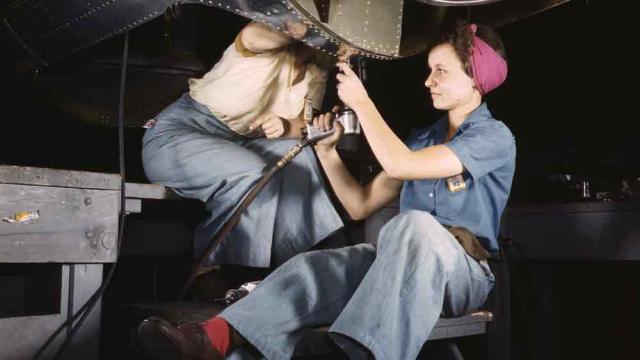
Thu, 05/22/2025 - 12:03
The Chinese character for crisis means “danger” and “opportunity,” and tariffs have created a supply chain crisis throughout the United States. Paul Roberts of the Seattle Times reports that fewer ships are arriving in Seattle: “Fewer ships coming…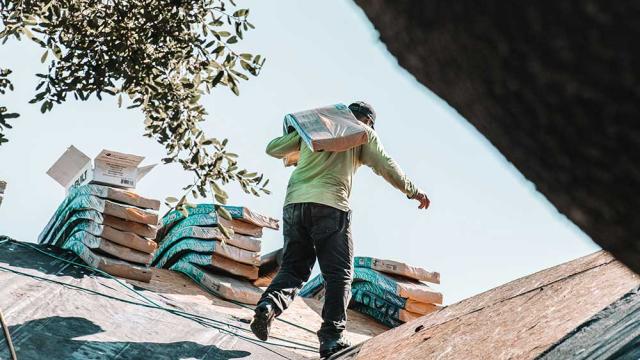
Mon, 01/20/2025 - 00:03
Recent labor relations controversies and ongoing arguments about the minimum wage have raised questions as to how a supply chain should share the utility it produces.
If we ask the wrong question, however, we’ll get the wrong answer. “What is a…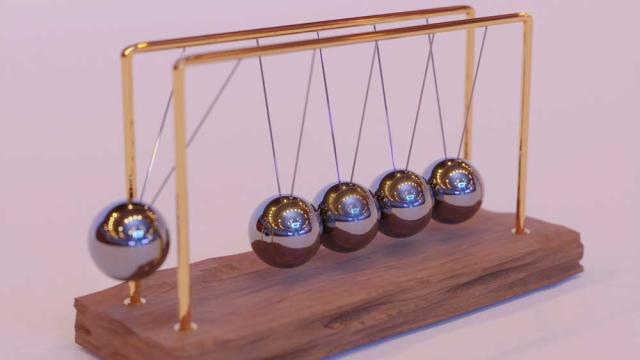
Mon, 12/23/2024 - 12:03
The ongoing relevance of the quality profession requires evolution and adaptation to meet the needs of the 21st century. Remember, the quality profession originated with the need for inspection to prevent poor quality from reaching customers; this…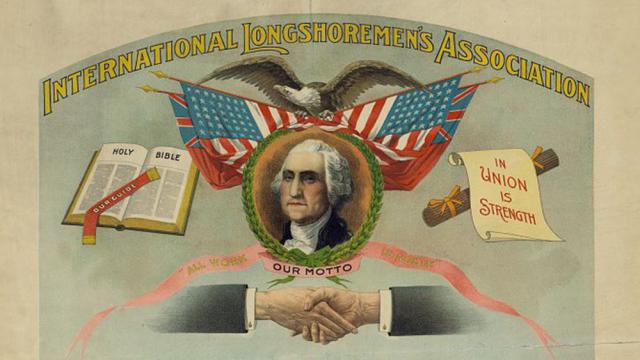
Tue, 10/15/2024 - 12:03
The Associated Press, reporting on the strike by the International Longshoremen’s Association, noted, “Local ILA president Boise Butler said workers want a fair contract that doesn’t allow automation of their jobs.” The report added, “The union had…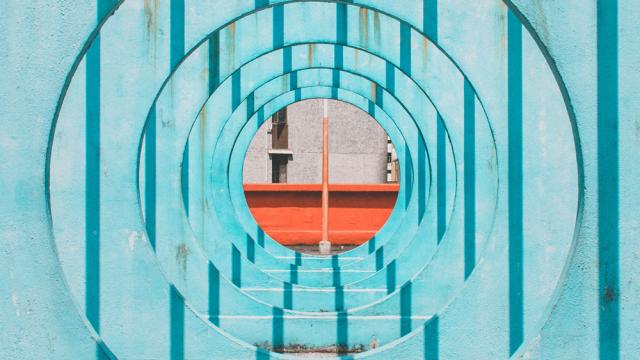
Wed, 08/28/2024 - 12:03
Most quality practitioners are familiar with the Taguchi loss function, which contends that the cost of any deviation from the nominal follows a quadratic model. This is in contrast to the traditional goalpost model, where anything inside the…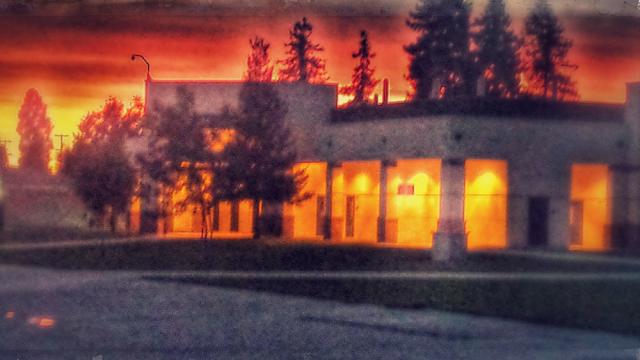
Wed, 06/19/2024 - 12:03
The International Accreditation Forum (IAF) and ISO have published a joint communiqué to require organizations to “consider” climate change in the context of risks and opportunities relevant to the management system.
Although this is pursuant to…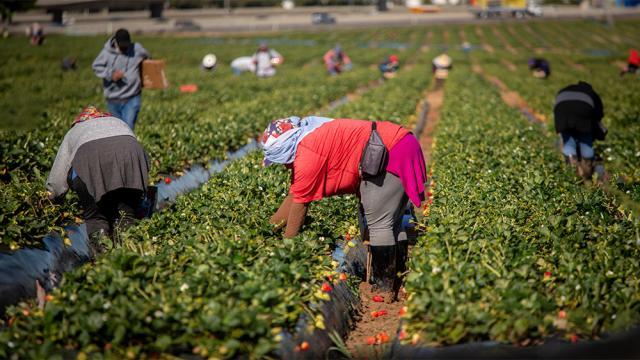
Mon, 06/10/2024 - 12:03
Although quality management has been around in some form or another for thousands of years—a cover of Joseph Juran’s Quality Handbook depicted Egyptians making very precise measurements for the construction of pyramids—this article will show that…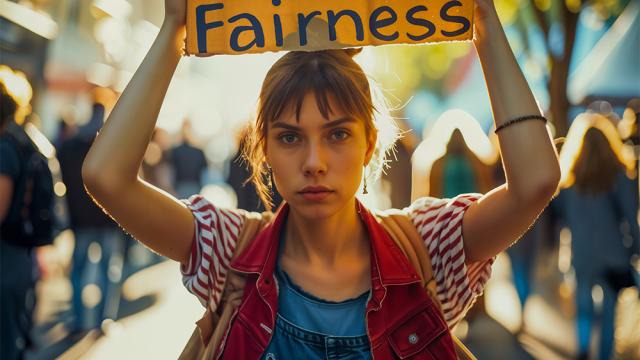
Wed, 05/08/2024 - 12:03
The famous football coach Vince Lombardi purportedly said, “Winning isn’t everything; it’s the only thing.” (According to Bartlett’s Familiar Quotations, in a 1962 interview Lombardi said, “Winning isn’t everything, but wanting to win is.”)
In…