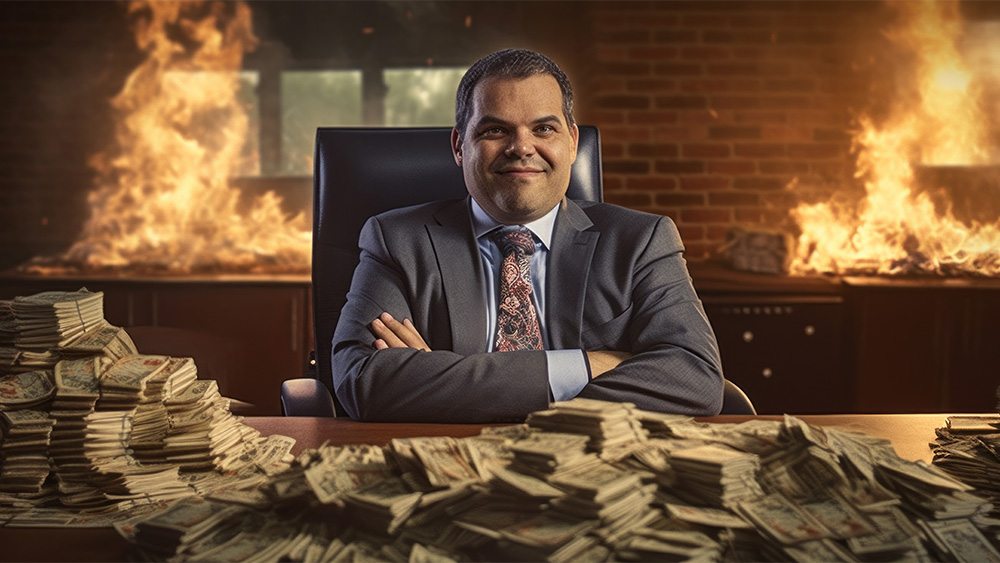
The current alleged quality problems with the Boeing 737 underscore the importance of zero tolerance for poor quality. No manufacturing or quality professional should ever compromise on this issue. Most importantly, the potential consequences to customers but also to the organization are simply not worth the risk.
ADVERTISEMENT |
Regarding the door-plug blowout on an Alaskan Airlines flight in January 2024, NBC News reported that a Federal Aviation Administration audit of Boeing and Spirit AeroSystems—which put the plane at the center of January’s incident—“found multiple instances where the companies allegedly failed to comply with manufacturing quality control requirements.”1 This is but the latest situation in which failure to ensure quality has resulted in a disaster that proved far more costly than containment followed by closed-loop corrective action would have been upfront.
…
Add new comment