All Features
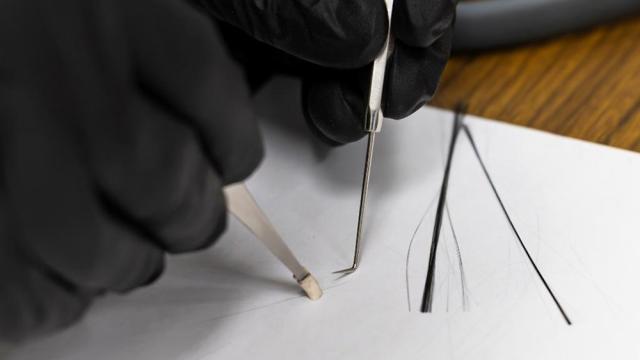
Oak Ridge National Laboratory
Stronger than steel and lighter than aluminum, carbon fiber is a staple in aerospace and high-performance vehicles. Now, scientists at the U.S. Department of Energy’s Oak Ridge National Laboratory have found a way to make it even stronger.
ORNL researchers simulated 5 million atoms to study a …
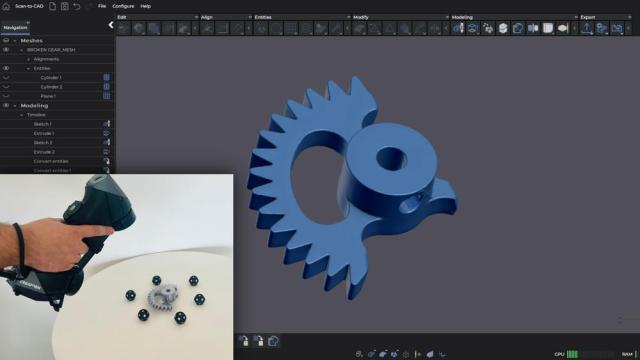
Creaform
Streamlining the transition from scan to CAD involves selecting the right tool set for reverse engineering. However, many software platforms force product designers to switch between multiple tools, disrupting their workflow and increasing the risk of errors. Furthermore, some advanced scan-to-CAD…
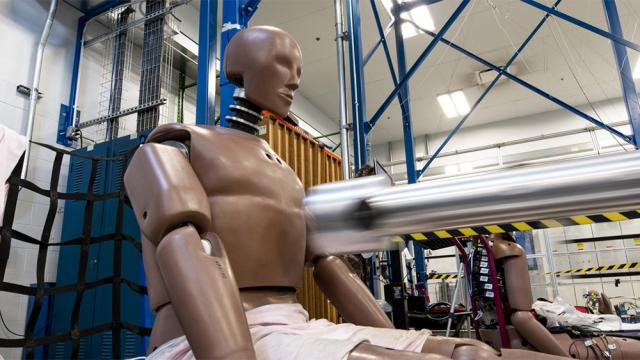
InnovMetric
Humanetics is the world’s largest manufacturer of anthropomorphic test devices (ATDs), commonly known as crash test dummies. The group has more than 1,000 employees across 21 facilities located around the world, with global corporate headquarters in Farmington Hills, Michigan.
Humanetics is…
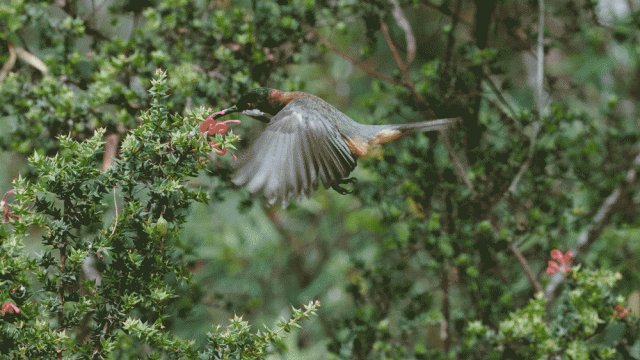
Rene Ymzon
When manufacturing tolerances shrink to the micron, and part geometries become increasingly complex, the margin for measurement error disappears. In this space—where even thermal drift or mechanical vibration can invalidate results—motion control becomes not just a component but a cornerstone of…
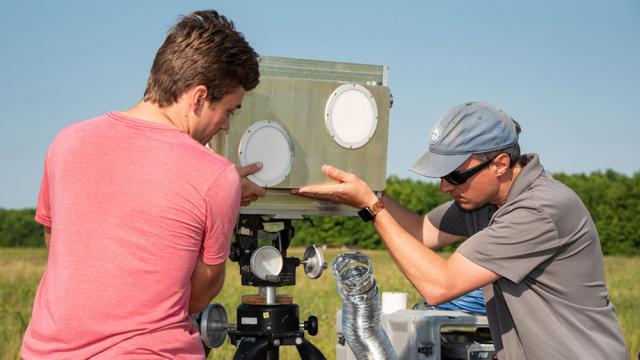
Ariana Tantillo
A team from MIT Lincoln Laboratory has built and demonstrated wide-band selective propagation radar (WiSPR), a system capable of seeing out various distances at millimeter-wave (mmWave or MMW) frequencies. Typically, these high frequencies, which range from 30 to 300 gigahertz (GHz), are employed…
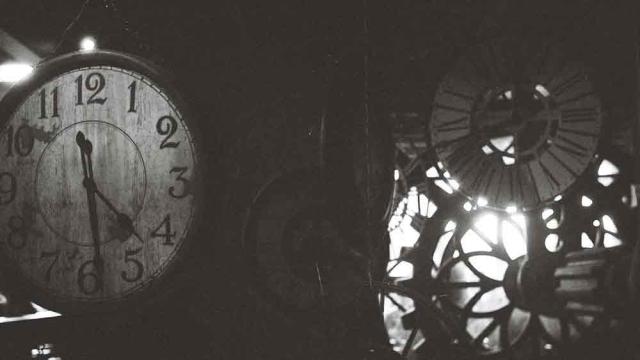
Dr. Scott Davis
Imagine what life would be like without GPS, something you use all the time without thinking about where it came from.
NIST’s atomic clock research helped bring us GPS, which has had more than $1 trillion dollars in economic impact.
This is just one of the many scientific breakthroughs to come out…
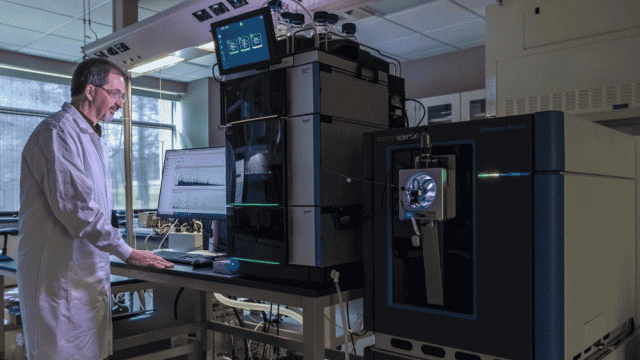
Oak Ridge National Laboratory, Robert Hettich
Robert “Bob” Hettich has spent much of his career at the U.S. Department of Energy’s Oak Ridge National Laboratory (ORNL) demonstrating how high-performance analytical measurements, in particular mass spectrometry, can yield remarkable insights into the mysteries of tiny microbes and their effect…
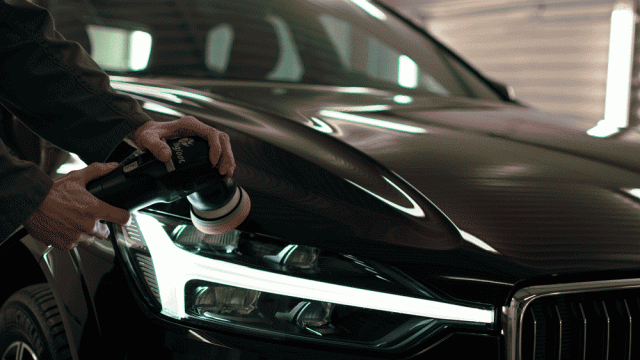
Prerna Sudera
Ensuring that automotive components meet the highest quality standards is critical to vehicle safety and performance. Metals and protective coatings used in automotive manufacturing must withstand extreme conditions such as mechanical stresses, corrosion, and wear during a vehicle’s lifespan. Here…
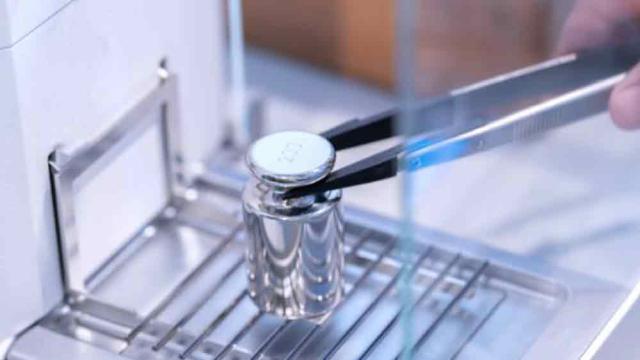
CIH Equipment
Industrial hygiene equipment plays a critical role in ensuring workplace safety by monitoring airborne contaminants, noise levels, and other hazardous conditions. However, accurate readings depend on regular industrial hygiene equipment calibration to maintain precision and compliance with…
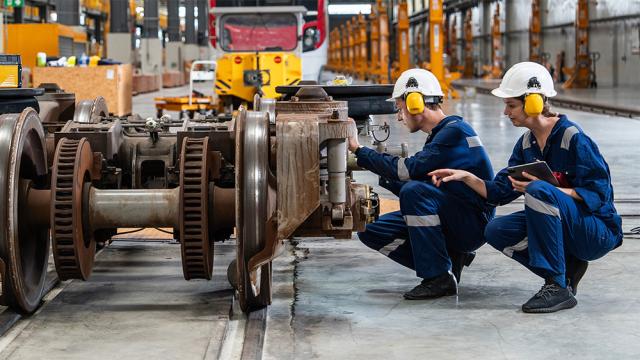
Thwing-Albert Instrument Company
Quality control workflows are only as effective as the machinery they rely on. Ensuring functionality requires understanding what to test and how to measure these factors. Consequently, choosing appropriate material testing equipment is a crucial—if overlooked—step in the quality assurance process…
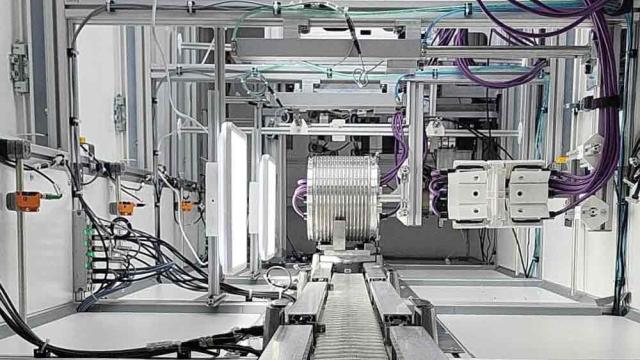
Silke von Gemmingen
In areas such as high-precision metalworking, accuracy is nonnegotiable. This includes the automotive industry and its suppliers, which are in crisis in Germany for several reasons. The industry is under enormous pressure to deliver products of impeccable quality while reducing operating costs (for…

Creaform
Hawthorne High School of Manufacturing & Engineering in Los Angeles is not your typical high school program. Led by program coordinator Lucas Pacheco, it’s a hub where young minds are immersed in advanced manufacturing and engineering design courses. With a hands-on curriculum covering multi-…
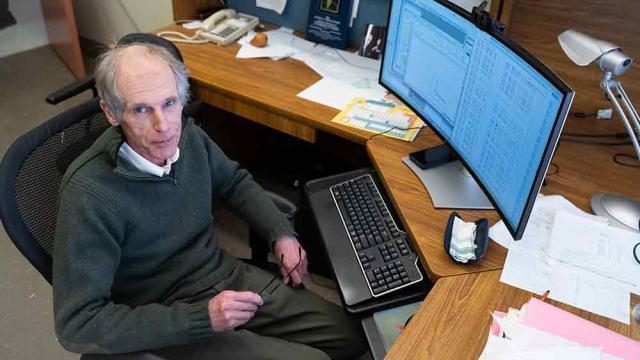
Alexander Kramida
Nearly everything we know about the universe comes from light. Cosmologists learn about the universe by studying light from faraway stars and comparing what it shows us to the light of the same atoms here on Earth. Astronomers use this information to study the expansion of the universe after the…
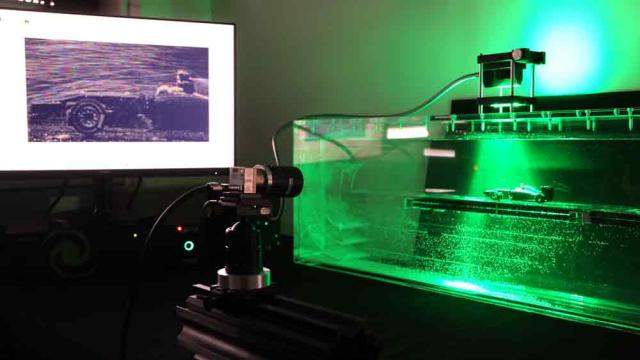
Sabine Terrasi
Today, modern measurement technologies enable high-precision detection of the movement of liquids and gases, providing valuable data for numerous applications. How does air flow around an airplane? How does blood move through our veins? And how can pollutant emissions in combustion processes be…
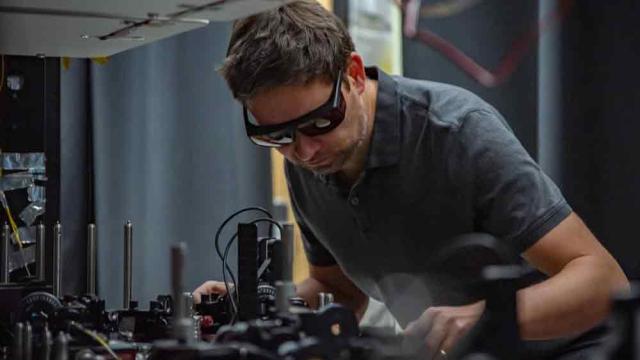
Krister Shalm
One lecture in an undergraduate quantum physics class changed my life forever.
It was 2001, and the professor introduced the idea that physicists could use quantum particles to build a new kind of superpowerful computer. I was so captivated by the idea that quantum physics could lead to…
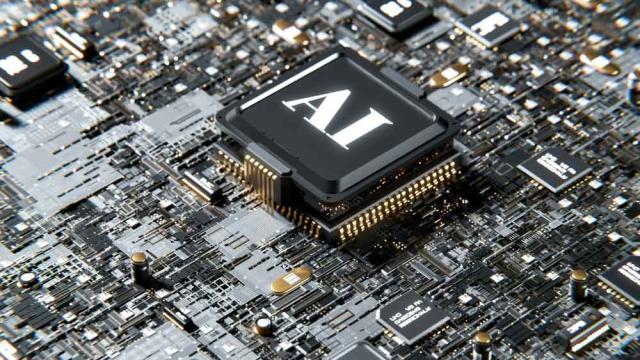
Akli Adjaoute
Keeping quality high in today’s fast-moving production world is a big challenge. Traditional quality checks have worked well, but they can be slow, require a lot of work, and are prone to mistakes.
AI could change this by making quality control faster, more accurate, and easier to scale. It could…
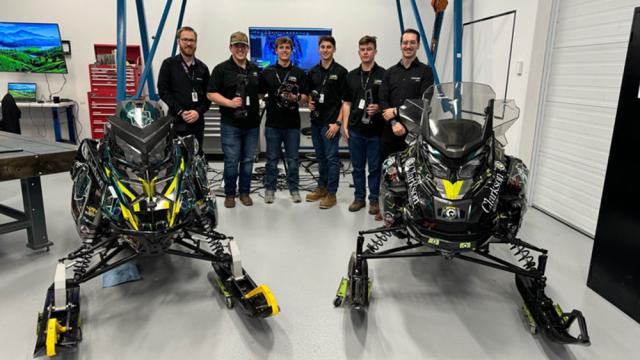
Creaform
Clarkson University is a private national research university in upstate New York and a leader in technological education. As one of the many Student Projects for Engineering Experience and Design (SPEED), the Clarkson University Clean Snowmobile Team is a student-led initiative driven by a passion…
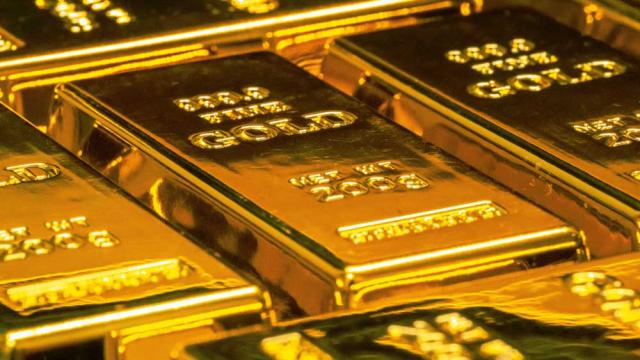
Donald J. Wheeler
Outliers are values that don’t “fit in” with the rest of the data. These extreme values are commonly considered a nuisance when we seek to summarize the data with our descriptive statistics. This article will show how to turn these nuisances into useful information.
The earliest statistical tests…
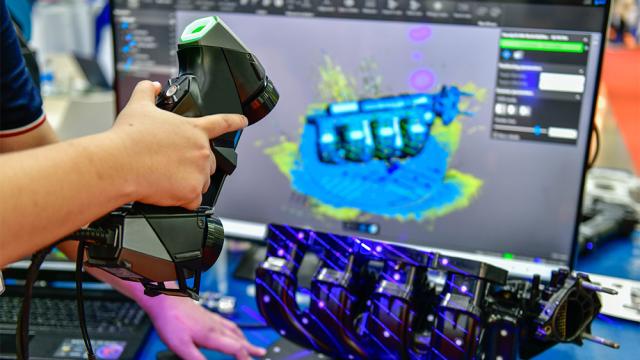
Steven Ouellette
Many industries, from aerospace to medical device manufacturing, are required to show customers, auditors, or regulatory bodies that their measurement devices are acceptable for use. But how do you prove that?
One of my clients needed to show the Biomedical Advanced Research and Development…
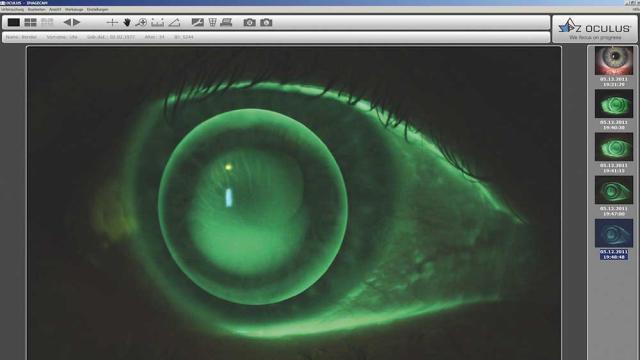
IDS Imaging Development Systems
The slit-lamp examination is one of the most important diagnostic techniques in ophthalmology. It enables a detailed examination of the anterior, middle, and posterior segments of the eye. Ophthalmologists can use it to recognize the smallest changes, anomalies, or damage. This procedure is used…
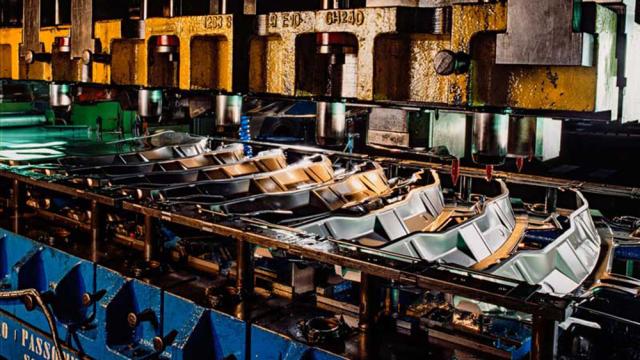
Creaform
Each type of part presents its own set of inspection challenges. This is especially true for sheet metal parts that are made of various entities, each with different positioning and dimensioning tolerances, and variable thickness gauges and sizes. These features can be inherently laborious to…
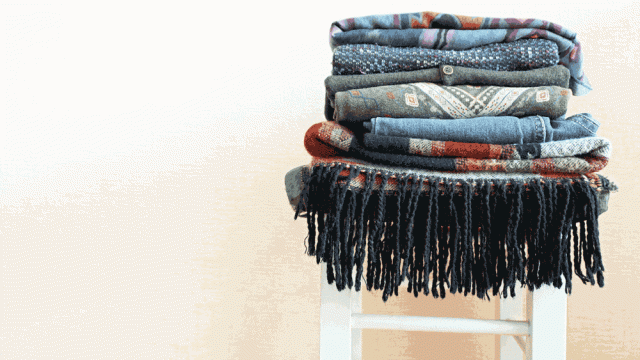
George Schuetz
Machinists working strictly in metalworking shops don’t have many occasions to gage the thickness of soft materials. But many of our readers work in supporting roles, helping to build or maintain the machines that produce textiles, plastic films, paper, and other products that are compressible.…
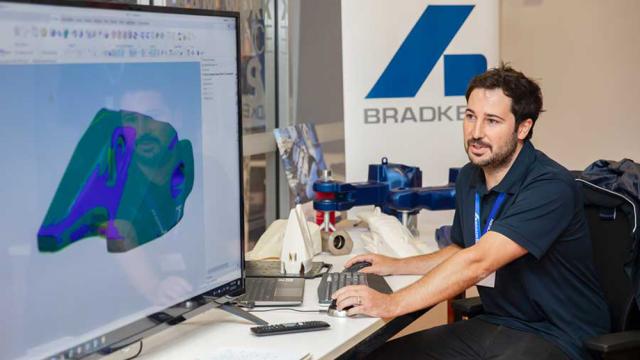
Creaform
Maintaining high-quality standards is critical in the heavy equipment industry. Customers rely on manufacturers to deliver products that perform reliably in harsh and demanding operating conditions. The stakes are high. Deviation from quality and overlooked detail can lead to expensive warranty…
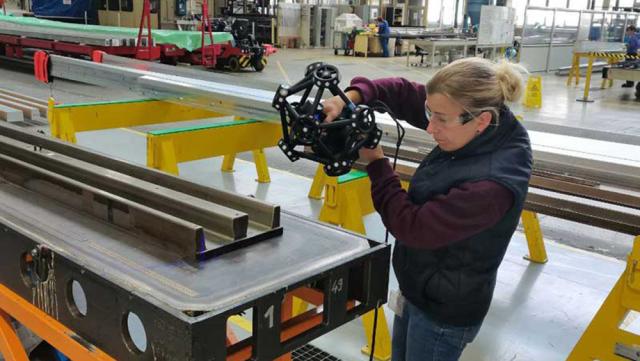
Creaform
GKN Aerospace Deutschland is a global tier-one supplier of airframe and engine structures, landing gear, electrical interconnection systems, transparencies, and aftermarket services.
The company has more than 38 manufacturing locations in 12 countries and 17,000 employees worldwide. It…
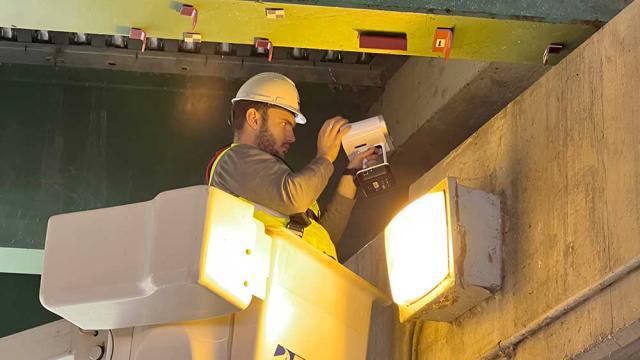
Sergey Sukhovey
The collapse of Baltimore’s Francis Scott Key Bridge in March 2024 was the consequence of a long-standing problem: the fragility of aging infrastructure. As reconstruction gets underway on an estimated four-year timeline, the disaster reflects the urgent need for better bridge inspection nationwide…