Content by Donald J. Wheeler
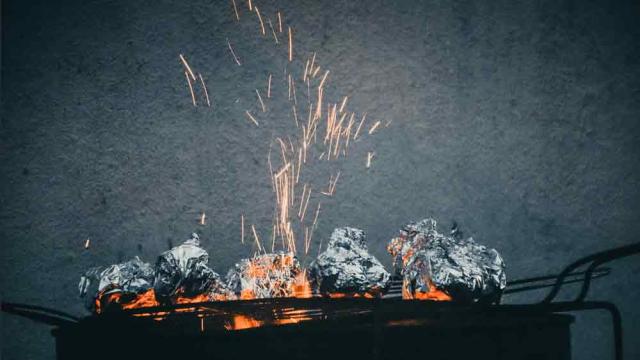
Mon, 06/16/2025 - 12:03
For many hundreds of years, “If it ain’t broke, don’t fix it” has summarized the predominant approach to process operation. From the physician’s admonition to do no harm, to the slightly more positive aphorism that the squeaky wheel gets the grease…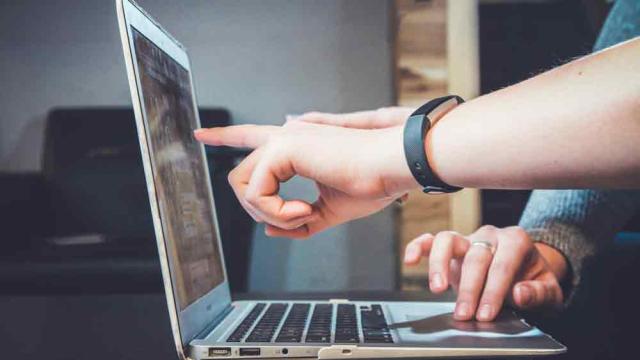
Mon, 05/12/2025 - 12:03
Define, measure, analyze, improve, control, goes the mantra used to carry out improvement projects in many companies. In various books, these steps get slightly different interpretations. But the overall outline is still characterized by DMAIC. This…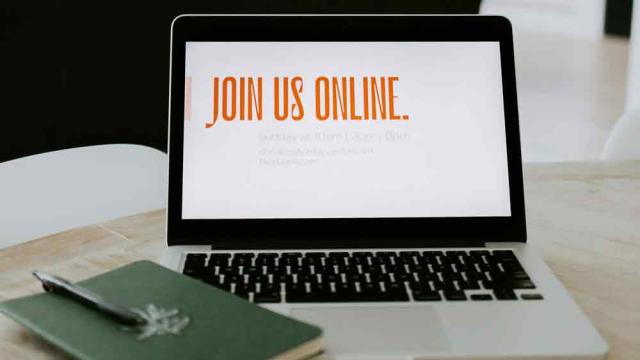
Mon, 04/21/2025 - 00:03
Dr. Donald J. Wheeler has been one of Quality Digest’s most highly read authors for decades. His teaching on the use of control charts in industrial settings has long been considered the gold standard. He has conducted more than 1,100 seminars in 17…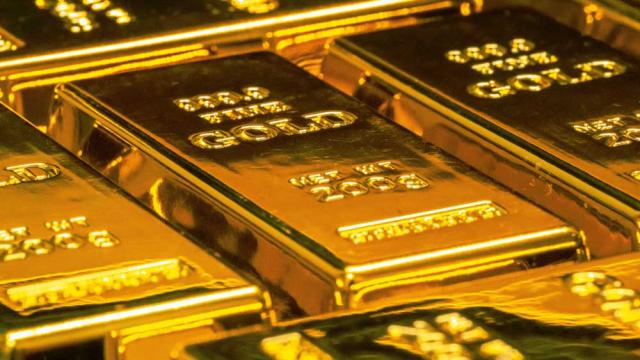
Mon, 04/07/2025 - 12:02
Outliers are values that don’t “fit in” with the rest of the data. These extreme values are commonly considered a nuisance when we seek to summarize the data with our descriptive statistics. This article will show how to turn these nuisances into…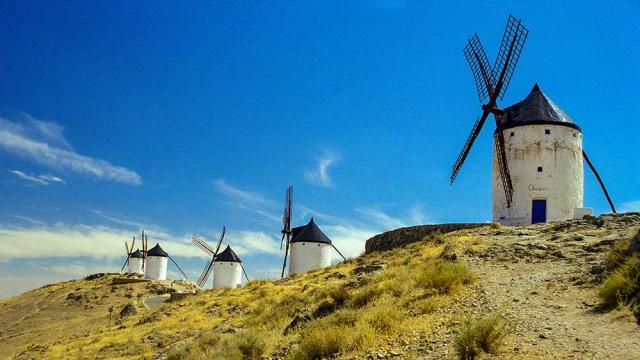
Wed, 03/05/2025 - 12:03
The Man of La Mancha never got to the unreachable goal—and if you’re being judged by overall equipment effectiveness (OEE), then your manager may also be dreaming an impossible dream. This column will look at problems associated with the use of OEE…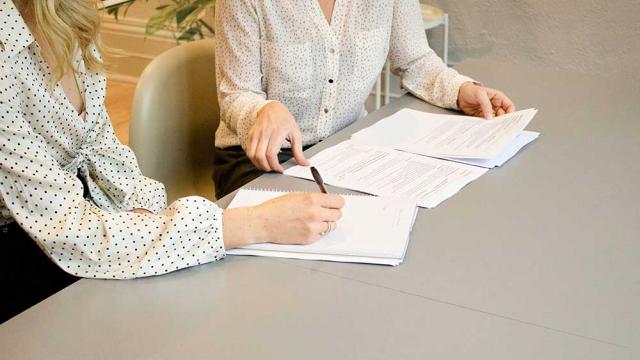
Mon, 02/17/2025 - 12:03
In last month’s article, “ANOVA and the Process Behavior Chart,” we saw how both techniques use the same basic comparison to answer completely different questions. Here, we’ll look at a case history where both techniques were used.
A physical…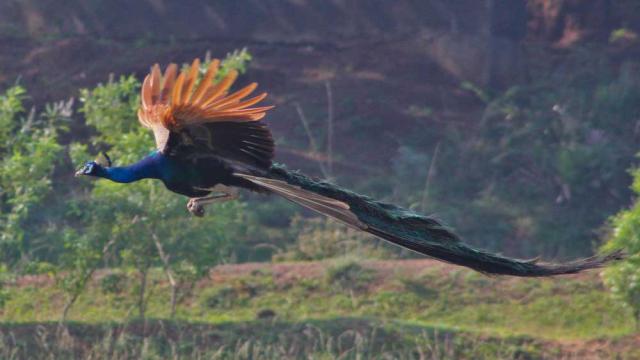
Mon, 01/13/2025 - 12:03
When Sir Ronald Fisher created the analysis of variance (ANOVA) in the 1920s, he extended the two-sample t-test to allow the comparison of k sample averages. During the same time period, Dr. Walter Shewhart was creating the process behavior chart.…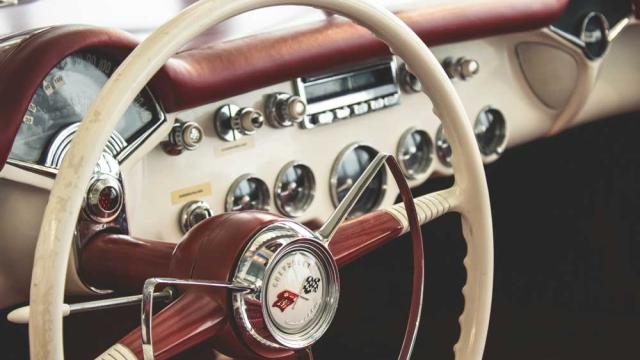
Mon, 12/02/2024 - 12:03
Managers are commonly fed a diet of report-card data. These data have usually been aggregated into summaries, averages, and totals to characterize the big picture. As useful as such summaries can be, they can also be an obstacle to an effective…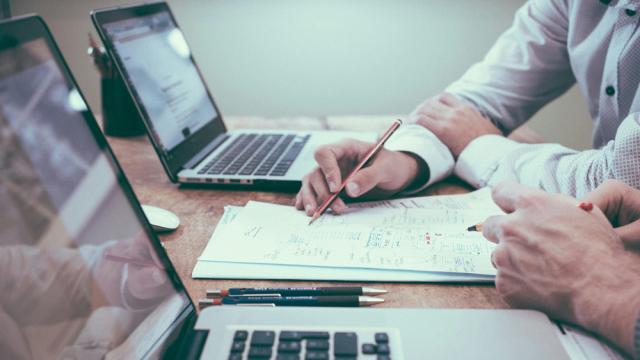
Mon, 11/18/2024 - 12:03
An engineer once told me, “I work on project teams that have an average half-life of two weeks, implementing solutions with an average half-life of two weeks.” Time after time, and in place after place, our improvement efforts often fall short of…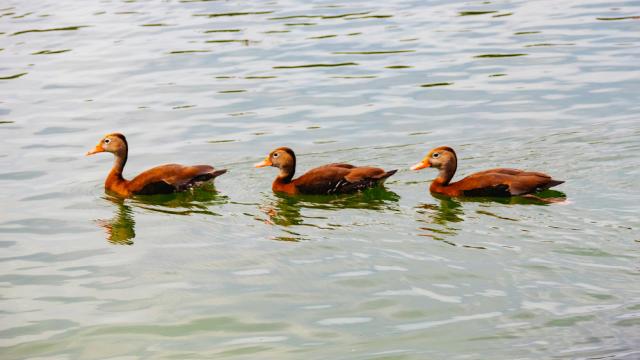
Wed, 10/16/2024 - 12:03
All improvement efforts require a framework. No matter what we’re doing, we all need some way to align our efforts and focus on a specific objective. During my 50 years in this business, I’ve seen people use many different improvement frameworks.…