Content by Thomas R. Cutler
Corporate Social Responsibility Starts with Quality and Occupational Health and Safety LinkMisr assesses and monitors the impact of its activities against internationally recognized ISO standards
Wed, 03/16/2022 - 15:30
(LinkMisr: Cairo) -- Corporate Social Responsibility (CSR) policies aim to guarantee that companies work ethically, considering human rights as well as the social, economic, and environmental impacts of what they do as a business. As more North…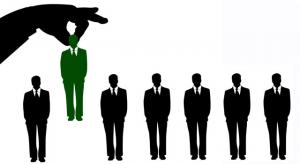
Mon, 04/26/2021 - 12:02
The demand for quality assurance and quality control managers in the manufacturing sector has never been stronger, according to Patrick O’Rahilly, founder of FactoryFix. This online platform matches vetted manufacturing workers with companies…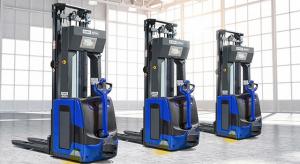
Thu, 10/15/2020 - 12:03
More than 80 percent of U.S. food manufacturing plants operating today were built more than 20 years ago and may lack safety features. The average age of manufacturing assets and equipment currently in operation in the United States, according to…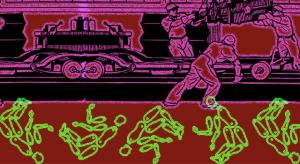
Wed, 09/09/2020 - 12:02
About one in two U.S. adults has a musculoskeletal disorder, costing an estimated $213 billion each year in treatment and lost wages, according to a report from the United States Bone and Joint Initiative. Musculoskeletal disorders (MSD) are…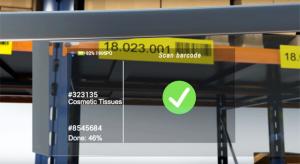
Thu, 08/13/2020 - 12:02
The old picking methods of paper, pick-to-light, and voice-picking are almost impossible when employees must practice social distancing, use PPE (personal protective equipment), and avoid contact that could potentially exacerbate the spread of Covid…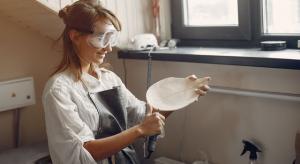
Tue, 12/10/2019 - 12:03
Quality control and inventory control are equally important to the ongoing success of all manufacturing businesses. Both form the basis of an efficient organization that operates at high productivity levels, minimizes waste, and delivers quality…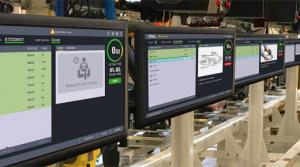
Wed, 07/18/2018 - 12:03
Although automation has been successful in replacing repetitive, simple tasks, the human workforce still plays a critical role in manufacturing. Even the most sophisticated and automated manufacturing operations rely on human operators to configure…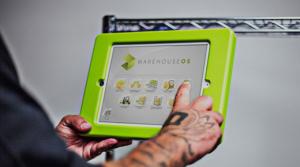
Mon, 08/28/2017 - 12:01
Flawless order fulfillment from a distribution center or warehouse to the customer’s door is the neglected leg of the supply chain. Ironically, without careful attention to the last mile, e-commerce customers are disappointed with the quality,… Quality Starts With CommunicationTraining a multilingual workforce to ensure quality and safety
Tue, 03/28/2017 - 12:03
Two years ago, the marketing research division of Florida-based TR Cutler Inc. interviewed CEOs of privately held manufacturing operations in North America and reported that their top fear was a lack of communication with employees due to the… Avoiding and Managing Product RecallsChildren are the most vulnerable consumers
Tue, 01/24/2017 - 12:01
Two words no manufacturing organization wants to hear: product recalls. By their very nature, product recalls are unpredictable events.
The cost to a company transcends potentially expensive litigation and settlements. Product recalls and the…