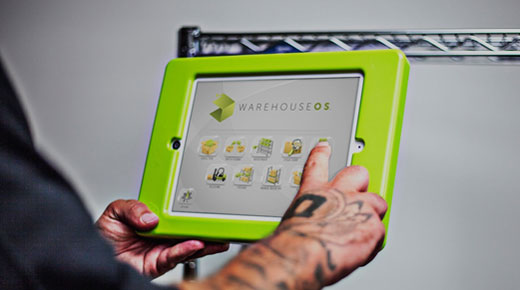
Flawless order fulfillment from a distribution center or warehouse to the customer’s door is the neglected leg of the supply chain. Ironically, without careful attention to the last mile, e-commerce customers are disappointed with the quality, accuracy, and condition of the products being delivered. Although tablets and mobile devices can provide the needed visibility, they are relatively new to the most important part of the supply chain: last-mile delivery.
ADVERTISEMENT |
Maximizing supply-chain visibility from raw materials to manufacturing is as essential as the picking and packing of the product.
Whether handled internally or relegated to third-party logistics (3PLs), customer orders can face an ugly journey on their last mile. Improved processes and decreased operational costs are driving the utilization of mobile tablets. Although radio frequency (RF) guns continue to collect data in the supply-chain process, tablets allow a better user interface with touch screens, connected bluetooth ring scanners, and a highly visual interface with pictures, colors, and more data fields. The RF gun is harder to train on, is usually handheld, and the screen interface is more cumbersome.
…
Add new comment