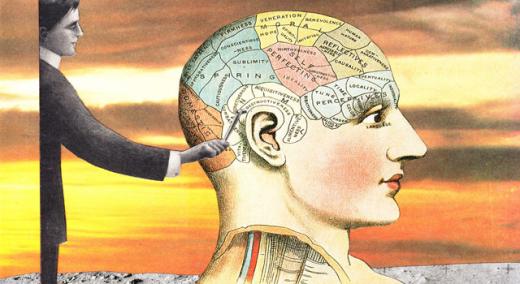
Credit: Bob May
Each article in this series presents new tools for increasing return on investment (ROI), enhancing customer satisfaction, creating process excellence, and driving risk from an ISO 9001:2015-based quality management system (QMS). They will help implementers evolve quality management to overall business management. In this article we look at the subclauses of Clause 6 of the standard.
ADVERTISEMENT |
Clause 6. Planning
Using Clause 6 to build organizational excellence and assess risk
Planning is another of the more obtuse words in ISO-babble. In my experience working with more than 700 companies, planning runs the gamut from how quickly and inexpensively you get product out the door to formal organizational plans for each process that have success metrics that are meaningful.
As we discussed in the article on Clause 5, successful planning begins with the principals creating meaningful and immutable vision, mission and values for everyone. You can’t plan a road trip if you don’t know where you are going and how you are going to get there.
…
Add new comment