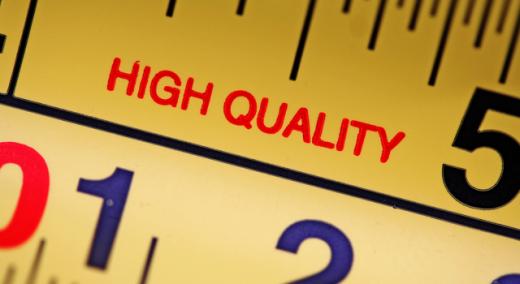
Each article in this series presents new tools for increasing return on investment (ROI), enhancing customer satisfaction, creating process excellence, and driving risk from an ISO 9001:2015-based quality management system (QMS). They will help implementers evolve quality management to overall business management. In this article we look at the clauses and subclauses of Section 9 of the standard.
ADVERTISEMENT |
Clause 9—Performance evaluation
Clause 9 is the part of the standard that we can use to truly quantify business excellence and risk avoidance. I will propose paradigm shifts that will make the outputs of this clause more informative for senior management and will include actionable recommendations that can contribute to the success factors that are immediately palatable and implementable for the leadership.
9.1.1 Monitoring, measurement, analysis, and evaluation—General
9.1.1 and excellence
This subclause requires that the organization must establish what needs to be monitored, measured, analyzed, and evaluated.
…
Comments
QMS applied in University set up for both academic and non
Dear Dr Tom,
Find this illustration very true and useful
What are yo thoughts and guidance when QMS is applied to a University. My institution is an International Sci & Tec type, and we really need to attain global status - whatever that means via partly through ISO certification for ISO 9001"2015
Kind regards
Add new comment