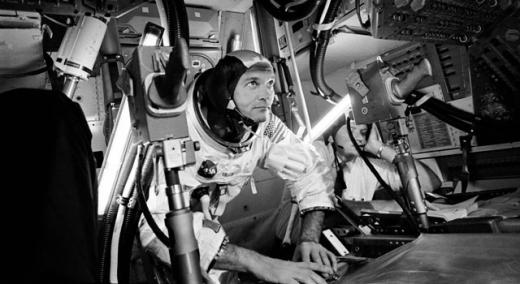
Each article in this series presents new tools for increasing return on investment (ROI), enhancing customer satisfaction, creating process excellence, and driving risk from an ISO 9001:2015-based quality management system (QMS). They will help implementers evolve quality management to overall business management. In this article we look at the clauses and subclauses of section 8 of the standard.
ADVERTISEMENT |
Clause 8: Operation
Clause 8 contains the requirements for planning, designing, and bringing to fruition your products or services. The processes within this clause must be robustly implemented to achieve business excellence. They must also be continually scrutinized for foreseeable risk.
8.1 Operational planning and control
8.1 and excellence
The “plan” is a series of interrelated process, each with acceptance criteria, and each with metrics that tie to the organization’s key objectives and key process indicators. Or, at least that has been my interpretation while leading scores of implementations.
…
Add new comment