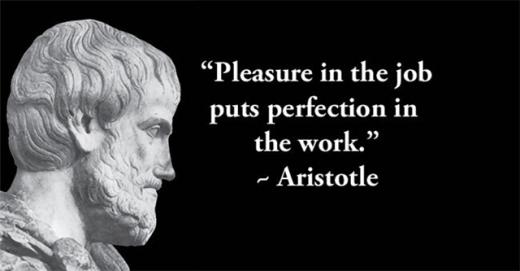
In lean there is mura, the waste of unevenness.
ADVERTISEMENT |
It’s probably the most important, but also most overlooked, in the waste theater.
For knowledge work, unevenness primarily interrupts flow. It’s when you have work that you should do easily but you don’t. There is this mura lying around that makes things harder than they need to be.
And most of this mura we create ourselves. Unnecessary rules, needless decision-making centralization, or simply not getting together and figuring out how we do things. So each professional on the team does predictable things in a slightly different way... making the predictable arbitrary.
Now, here’s the thing. We have three kinds of lean flow:
1. Operational flow (the flow of work)
2. Information flow (the flow of possibilities)
3. Psychological flow (the flow of our own creativity and focus).
If our aim is to create great product with an unhindered team, it is our job to make sure that all three kinds of lean flow happen to the best extent possible. We do this primarily by removing obstacles and increasing opportunities for professionalism.
This causes us to confront the double-edged sword of what lean calls “standard work.”
…
Add new comment