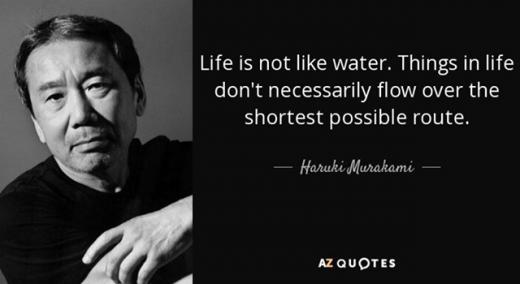
The strength of lean thinking and an agile mindset is that, at heart, they are both about continuous improvement. People want to, need to, improve. We need to get better at what we do, see increasing impact, and know we are making a difference.
ADVERTISEMENT |
If this is a core human need, why do most agile and lean transformations “fail?”
Although it’s tempting to blame managers or staff or coaches for the “failures” of companies and teams to do their A3s; their retrospectives; their story points; their define, measure, analyze, improve, control (DMAIC); or whatever, at some point we have to come to terms with the fact that these are human beings working and not simply work passing through human beings.
![]() We strive for flow but will never fully achieve it. |
Continuous improvement has always, and will always, “fail” because reality doesn’t respect it. People become overloaded, distracted, or even inspired. And these things change the course of work.
…
Add new comment