Content by Harish Jose
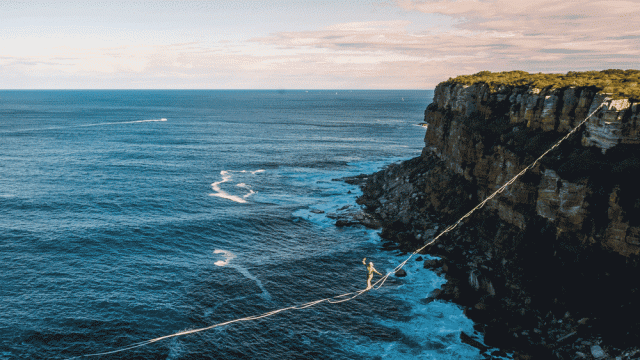
Mon, 06/16/2025 - 12:02
I am a longtime admirer of George Spencer-Brown’s “Laws of Form.” In this article, I explore how his notion of reentry helps illuminate the paradoxes and blind spots in modern ideologies, especially the rise of xenophobia and extreme nationalism.…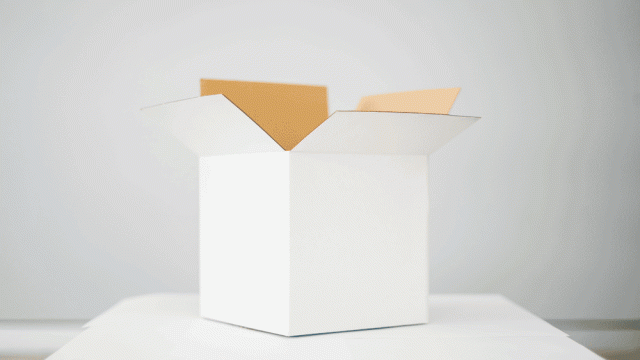
Tue, 05/06/2025 - 12:03
In this article, I’m looking at the brilliant philosopher Ludwig Wittgenstein’s “The Beetle in the Box” analogy.
Wittgenstein rose to fame with his first book, Tractatus Logico-Philosophicus, in which he proposed the idea of a picture theory for…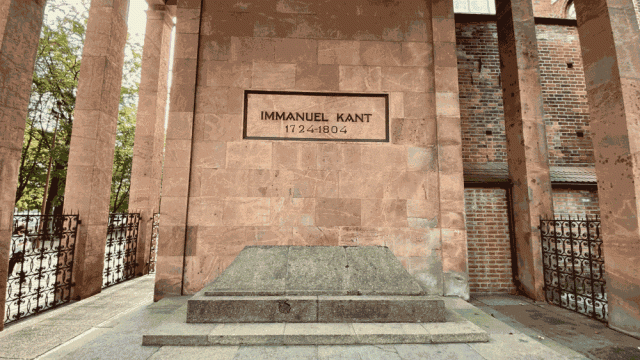
Tue, 02/18/2025 - 12:03
Today I’m looking at Immanuel Kant’s “thing-in-itself” and Hans Vaihinger’s ideas. In Kant’s philosophy, the thing-in-itself (Ding an sich) refers to the reality that exists independently of human perception or experience. Kant argued that while we…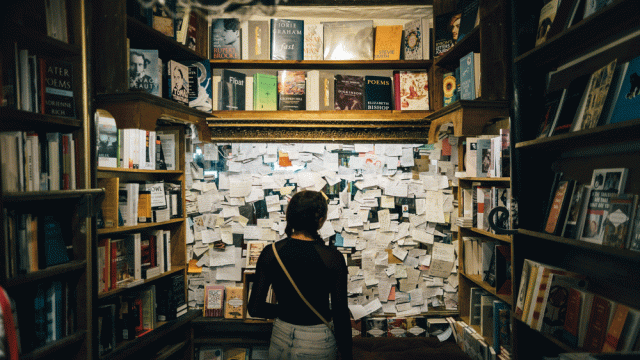
Tue, 02/11/2025 - 12:03
Today I’m looking at the free energy principle (FEP) by the British neuroscientist Karl Friston. The FEP basically states that to resist the natural tendency to disorder, adaptive agents must minimize surprise. This has implications for the gemba,…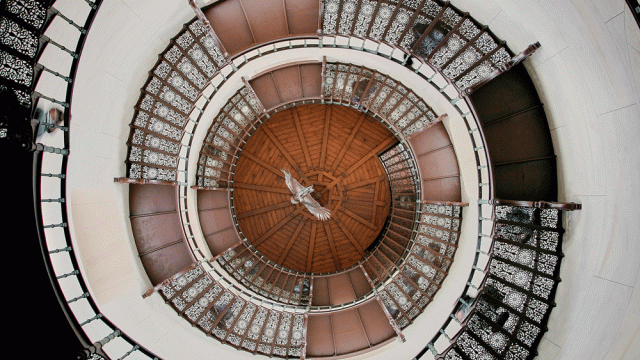
Wed, 01/22/2025 - 00:01
In this article, I’m exploring complexity through the lens of George Spencer-Brown’s Laws of Form (Cognizer Co., 1994). This philosophical and mathematical treatise explores the foundations of logic and mathematics via a unique symbolic system.…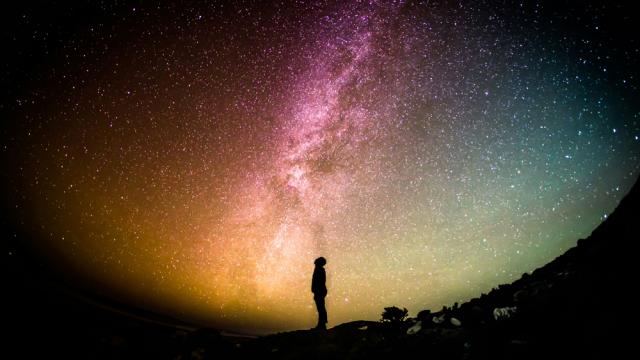
Mon, 11/11/2024 - 12:03
In this article, I look at the idea of “sweeping-in” in systems approach. Sweeping-in can be described as the process of opening up the inquiry of a system by expanding its boundaries. Philosopher and systems scientist C. West Churchman discussed…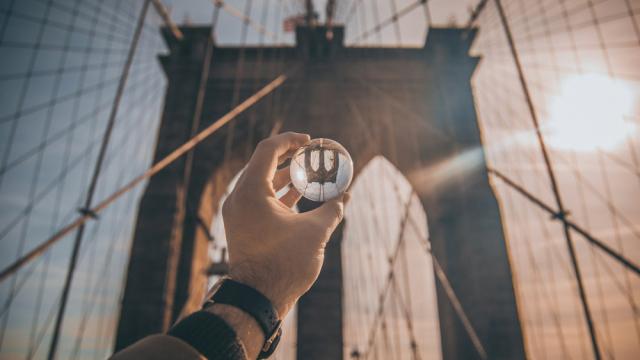
Mon, 10/21/2024 - 12:02
In this article, I’m looking at Weber’s Law. It’s named after Ernst Heinrich Weber (1795–1878), a German physician who was one of the pioneers of experimental psychology. I highly recommend the Numberphile YouTube video that explains this in detail…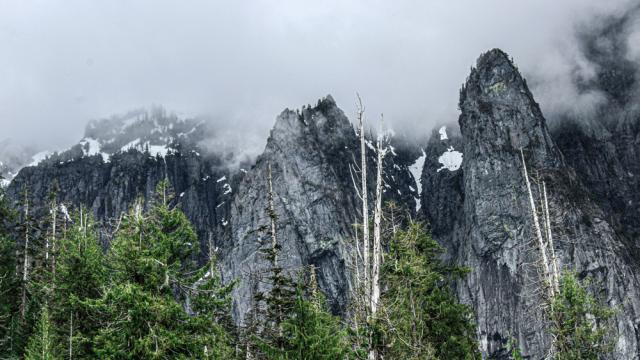
Tue, 08/13/2024 - 12:02
Recently, I wrote about the process capability index and tolerance interval. Here, I’m writing about the relationship between the process capability index and sigma. The sigma number here relates to how many standard deviations the process window…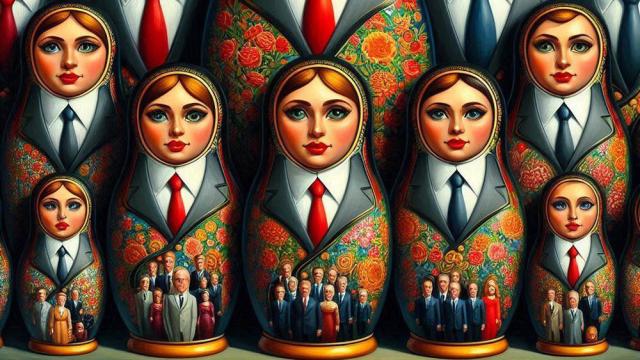
Tue, 07/02/2024 - 12:03
I have always been interested in the idea of autonomy in a social setting. In this article, I’m looking at autonomy in a social setting—such as an organization—from a cybernetics viewpoint. I’ll lean on the ideas of Heinz von Foerster and Stafford…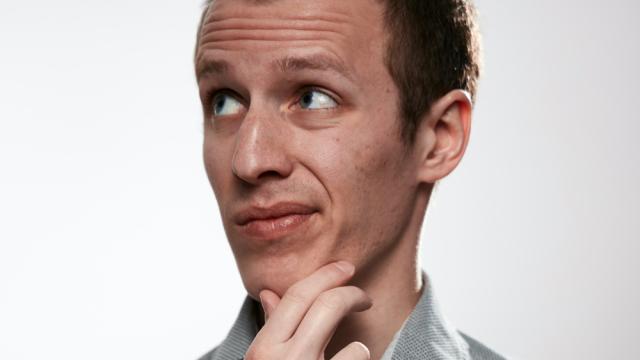
Tue, 05/07/2024 - 12:03
In this article, I’m looking at the relationship between capability index (Cpk or Ppk) and tolerance intervals. The capability index is tied to the specification limits, and tying this to the tolerance interval enables us to use the confidence/…