Content by Mike Micklewright
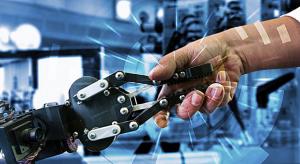
Tue, 05/28/2019 - 12:02
Industry 4.0 is the current trend of automation and data exchange in manufacturing technologies. Also known as the Fourth Industrial Revolution, it follows behind the previous three revolutions of: 1) mechanization, water, and steam power; 2) mass…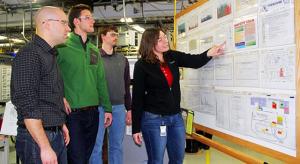
Thu, 04/25/2019 - 12:03
Knowledge of kaizen theory, principles, tools, and experience in application are of course very important in leading successful kaizen events that drive real bottom-line results. However, equally important are the facilitation skills of the person… Does Your Company Publish Fake News? How to overcome it in a kaizen culture
Wed, 03/22/2017 - 12:03
Fake news has fast become one of the most popular new phrases of 2017. We see it in Western politics, we listen to our news channels debate what is fake and what is not, and we hear our late-night comedians pan fake news with politically motivated… The Yin and the Yang of Standardized TrainingTraining Within Industry—the foundation of lean
Mon, 05/16/2016 - 12:09
Quiz time: What significance does the yin and the yang have in discussing standardized training? I suggest that you pause and guess (and then read on for the answer).
OK, we all get it, standards are a part of our lives in the business world, and… The Nuts and Bolts of Risk ManagementA tools-based approach
Wed, 03/30/2016 - 00:00
When considering any effort toward performance improvement, you should always start by looking at the organization’s principles and culture, and making sure these are aligned so they not only permit positive changes to occur, but also ensure that… Gemba Walks or Video Surveillance?A dichotomy of two approaches
Tue, 02/23/2016 - 11:20
In October 2014, 17-year-old Laquan McDonald was shot 16 times by a Chicago police officer. In November 2015, footage of the shooting was released and has been viewed all over the world. The footage shows an aggressive attack by a police officer, a… Lean, Quality, and Risk-Based Thinking in ISO 9001:2015Integrating principles, culture, and tools
Wed, 01/13/2016 - 14:19
I’ve made the point many times that the quality function and the lean/continuous improvement/kaizen function within an enterprise are really one and the same. Treating them as separate value streams with their own documentation, procedures, and… The Evolution of Daily KaizenTransferring principles of SPC to daily leadership
Wed, 12/23/2015 - 13:56
To many people, the relationship between daily kaizen and statistical process control (SPC) might seem as remote as the relationship between a kangaroo and the past iconic American TV series Friends. And yet, a kangaroo and Friends have a… Kaizen Approach to ISO 9001:2015Do it right this time!
Mon, 10/26/2015 - 11:34
Finally... the new version of ISO 9001:2015 has been released. I can hear many of you screaming, “Hurray!” Or not. More realistically, I’m sure many of you living in the kaizen world are thinking, “Yeah, so what? This stuff has nothing to do with… Still Can’t Master 5S? Try ‘1S.’Stop wasting time trying to stop wasting
Wed, 09/23/2015 - 16:50
I mean it! If your company can’t master 5S, try “1S” and stop! Stop the entire lean transformation until 5S is mastered in at least one process-focused area of the facility.
It’s a tremendous waste for a company to spend thousands, if not millions…