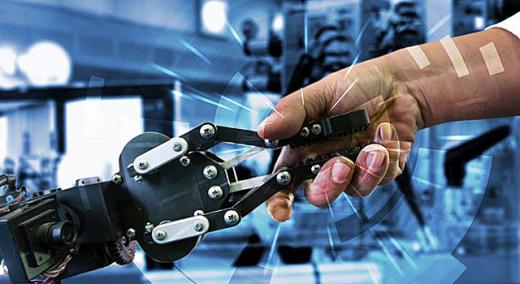
Industry 4.0 is the current trend of automation and data exchange in manufacturing technologies. Also known as the Fourth Industrial Revolution, it follows behind the previous three revolutions of: 1) mechanization, water, and steam power; 2) mass production, assembly lines, and electricity; and 3) computer automation. Industry 4.0 is also known as the “smart factory,” via the introduction of cyber-physical systems.
ADVERTISEMENT |
Working in a kaizen-centered culture requires the constant, everyday elimination of waste in the workplace. This transforms an organization into one that continuously improves and provides excellent results.
Through the smart use of cyber-physical systems and the careful planning and integration of these systems into a kaizen culture, an organization can and will leapfrog the competition in terms of productivity and quality improvement while gaining more flexibility and throughput.
…
Add new comment