Content by Tim Lozier
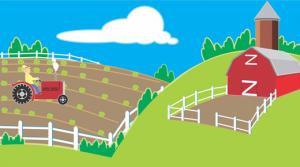
Wed, 06/13/2018 - 12:02
Quality management systems (QMS) have become strategic components that touch more and more of the business today. With new versions of QMS standards, and the enrollment of all people in the quality management effort, the need for cohesion from one…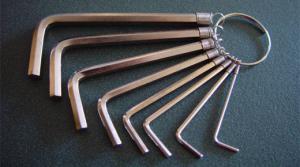
Tue, 05/22/2018 - 12:03
Corrective action is often an effective means of identifying and correcting quality and compliance events within the organization that can arise through the result of complaints, audits, incidents, nonconformances, or any adverse events.…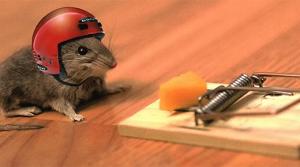
Wed, 03/21/2018 - 12:01
The concepts and frameworks behind quality management are evolving. As more companies adopt new technologies, and standards like ISO 9001:2015 begin to shift in focus, there is a concept that is arising out of Industry 4.0, the factory of the…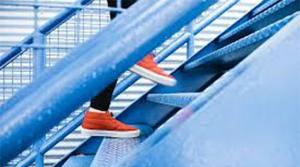
Tue, 12/05/2017 - 12:01
Enterprise software solutions have become commonplace, and in many organizations, quality management systems (QMS) are a strategic priority.
This article will cover five things that you can build into your QMS that will enhance your ability to…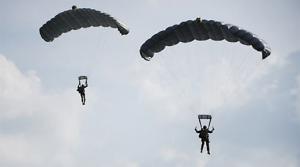
Tue, 08/15/2017 - 12:02
Sponsored Content
The difference between cloud providers is often found in their chosen deployment method. Typically, software can be implemented either through multi-tenant or dedicated cloud environments. With the advent of virtual servers, cloud…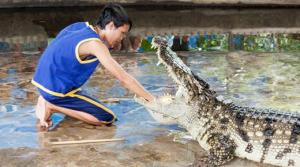
Wed, 07/05/2017 - 12:01
The dynamic of risk management and compliance seems to be experiencing a shift toward risk management in operations, and learning to pay attention to detail in order to leverage it.
The biggest question often asked is, “I’m aware my company needs… Four Beneficial Byproducts of Automating Your Corrective ActionsGet rid of gray areas and enhance continual improvement
Mon, 01/30/2017 - 12:01
Sponsored Content
For quality management to be effective, a solid corrective action process is critical. ISO standards and general best-practice guides suggest—and even mandate—a set procedure and proper documentation for addressing and correcting… Productivity Hacking in Quality ManagementSimple ways to get more visibility and control in your processes
Thu, 01/26/2017 - 12:02
When it comes to quality management, it’s not just about the requirements. As companies register to ISO 9001:2015, we see an additional shift. Not only are management system requirements changing to build an improved framework for the standard, but… Compliance Can’t Wait: Three Steps for Better Quality LeadershipEmails and spreadsheets are no way to store and share quality information
Wed, 07/20/2016 - 00:00
Recently, there has been a shift in the way quality is led and implemented in organizations. The updated ISO 9001 standard urges leaders to incorporate quality in all levels of business, from stakeholders to upper management and throughout the… Risk Management Outside Your Four WallsImplementing risk strategies for the supply chain
Thu, 04/21/2016 - 09:10
When we look at business dynamics, regardless of industry, we see an increasing rate of change in products, processes, and regulations. One process affects the next, and with a growing focus on regulations and standards, complexity becomes an ever-…