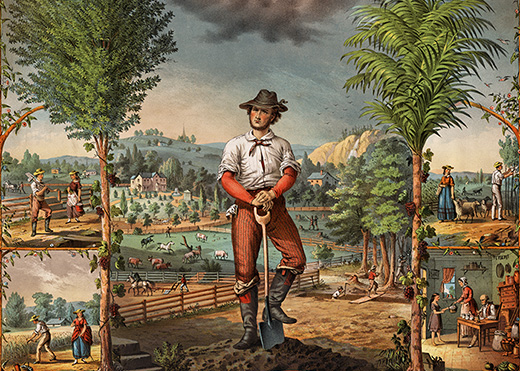
When it comes to quality management, it’s not just about the requirements. As companies register to ISO 9001:2015, we see an additional shift. Not only are management system requirements changing to build an improved framework for the standard, but we also see an emphasis on an overall mindset that prioritizes quality.
ADVERTISEMENT |
With that in mind, the question remains: How can we work together as a team to promote a companywide commitment to quality in a centralized and common way?
Let’s take it one step further. Your processes don’t just exist within your four walls, so it’s important to extend these quality principles to your external parties so everyone benefits from them.
How do we centralize quality to promote visibility?
If the entire organization is working together toward quality goals rather than one person owning it, we need a centralized, common, and collaborative environment that gives us visibility into our quality management system (QMS) while making us active participants in quality.
…
Add new comment