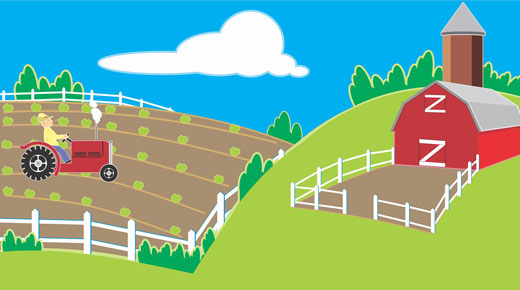
Quality management systems (QMS) have become strategic components that touch more and more of the business today. With new versions of QMS standards, and the enrollment of all people in the quality management effort, the need for cohesion from one system to the next is becoming critical.
ADVERTISEMENT |
Let’s consider the “story of quality”—the chain of quality’s effect on various areas of the business, and how those operational areas rely on quality-based information to gain visibility and control, affect operations with a quality eye, and create a hub of quality throughout design, production, supply chain, and post-market.
There are three elements here that are necessary to this story of quality—integration, harmonization, and risk-based thinking.
Integration
In today’s business environment, it is nearly impossible to effectively manage operations, quality, and the product life cycle without implementing business software systems. Applications such as supply chain management (SCM), enterprise resource planning (ERP), manufacturing execution systems (MES), and similar tools have become a necessary part of enterprise technology.
…
Add new comment