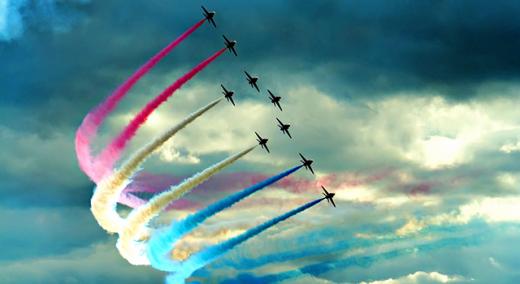
Lean production of multiple products is built on the assumption that the process aim can be properly set for each short production run. This article will describe how to set the process aim so that your short production runs can be on target.
ADVERTISEMENT |
In a lean production environment, without a bank of in-process inventory to cushion the impact, and without adequate lead time to allow for reworking or refabricating the product, a single off-target run can shut down an assembly operation and create a massive pile of unintended, in-process inventory. (I once saw 25 jumbo jets parked outside their assembly building. When I asked why they were parked there, I was told that they were all waiting for parts—a billion dollar pile of in-process inventory!)
Aim vs. consistency
A plant had three suppliers for a piece of wire. When a shipment arrived they collected a sample of five pieces and measured their lengths. These five values were subgrouped together and placed on an average and range chart. The charts for each of the three suppliers, drawn to the same vertical scale, are shown in figure 1.
…
Comments
Great article, I have a question
We deal with a batch process that produces many products on the same production line. So this article details exactly what we are facing. We have found that the target-centered XmR approach does drive us to target more quickly. However, overall variation in the run tends to increase during a production run since we are more agressively adjusting the process.
So there is a trade-off between:
- on-target, higher variation
- off-target, lower variation
Of course everyone wants on-target, low variation. Starting a production run closer to target and getting to target more quickly does improve variation during the run - but that isn't always possible. Any thoughts or experience on balancing this trade-off?
Add new comment