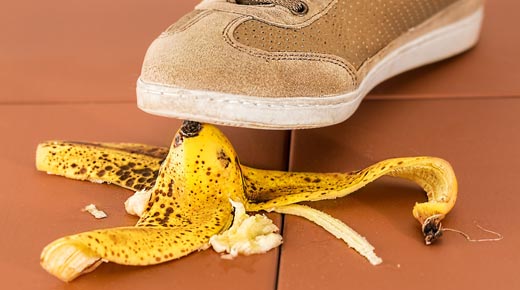
‘We’ve always done it that way” explains why many suboptimal and even obsolete methods are taken for granted. The range chart for statistical process control (SPC) is, for example, somewhat inferior to the sample standard deviation chart, and it is almost certainly a holdover from when all calculations had to be done manually.
ADVERTISEMENT |
It is far easier to subtract the sample’s smallest measurement from the largest one than it is to compute the sample’s standard deviation. Risk priority number (RPN) for failure mode and effects analysis (FMEA) could similarly be a suboptimal approach to risk analysis.
Risk priority number’s inherent drawbacks
The RPN is part of the body of knowledge for many ASQ certifications, and it appears in authoritative textbooks on FMEA and advanced quality planning as well as an Automotive Industry Action Group (AIAG) manual. AIAG may, however, be contemplating a replacement. Its nature is currently unknown but this is a good opportunity to discuss RPN and some existing alternatives.
…
Comments
Misquoting of "How to Get More Out of your FMEAs"
In the article you state “Various fixes have been applied to the severity rating to reflect its ordinal nature. Richard Harpster defines the “legal zone” to include any failure mode with a 9 or 10 severity in “How to Get More Out of your FMEAs”.
The statement misrepresents what the article actually said. The article states “Those who use FMEAs need to learn that the class value is more important than the RPN. The class value is derived from the severity/occurrence matrix shown in Figure 2 below, puts the RPN into its proper perspective.” When I wrote the article in 1999, the AIAG FMEA Manual 2nd Version was in effect. In the manual, the occurrence rating of a 1 indicated a failure of at least 1 in 1.5 million. If a company was designing automobiles and 1 out of every 1.5 million of their customers was going to be severely injured or die due to a known design issue, I believe most people would identify this combination of severity of harm and probability of exposure to indicate an unacceptable level of risk. If one were to look at it from a financial perspective, I am quite sure the financial penalties would be quite high in a court of law if it came out in testimony that an automotive company was knowingly shipping vehicles with a design flaw that they believed would result in the death or injury at a probability of 1 in 1.5 million. Consequently, given the limitation of using the Occurrence Rating Table in the AIAG FMEA Manual 2nd Version, the paper put the combination of Severity of 9 or 10 and Occurrence of 1 in the “legal zone” indicating unacceptable risk. If you had included a copy of the entire matrix from the 1999 article people would be able to see the important relationship that the article defined between severity of harm, probability of exposure to harm and risk.
One of the most important improvements in the AIAG 4th Edition FMEA manual was the changing of the definition of the Occurrence Rating of 1 in the Design and Process FMEA from a numerical value of “</= .01 per 1 thousand” to the statement that “The failure is eliminated through prevention control”. This allowed the creator of the Design and/or Process FMEA to properly identify the level of harm as a Safety or Regulatory Issue while assigning an occurrence rating of 1 that indicated that despite the high level of harm the risk is acceptable because of the actions the company had taken to reduce the probability of exposure.
One should never just use the Severity Rating to make any decisions to determine what must be worked on in any Design or Process FMEA.
Richard Harpster
Class Matrix
Richard,
The entire class matrix is definitely worth attention (bottom of https://www.qualitydigest.com/june99/html/body_fmea.html at the bottom). The takeaway I got from it is, in particular, that anything within the legal zone requires attention regardless of the occurrence rating, which is also the takeaway from the Army's Risk Management process; anything with a Catastrophic severity cannot have less than a medium risk level even if the occurrence rating is the best possible. The Warranty Zone, which I didn't mention, is definitely worth attention as well.
The point you make above about a design flaw with a 1 in 1.5 million chance of killing somebody being unacceptable also ties in with mine about the need to account for frequency of exposure to the risk. A 1 in 1.5 million chance of death, on a 1-time basis, might be considered acceptable as shown by the F/N diagram (e.g. 2E-5 of causing one death in any given year with a MTBF of roughly 625 times the human life expectancy) but, when multiplied by thousands or millions of opportunities (e.g. several million vehicles), it is not.
Critical Issue Missing From Specified Approach
When managing risk, it is critical to consider the products intended use. As an example, I have recently worked on both spinal implants and a late stage cancer treatment. In both cases, there were five categories of harm considered: Death, Permanent Injury, Injury Requiring Medical Attention, Injury Not Requiring Medical Attention and Inconvenience or Temporary Discomfort. Because of the differences in intended use, the definition of acceptable risk was different. Although attempts were made to reduce all risk, the definition of acceptable risk was much higher for the late stage cancer treatment than for the spinal implant.
The combination of the Severity/Occurrence Risk Matrix and Intended Use should be used to determine what must be worked on and acceptable levels of risk. The resultant strategy is known as a company's "Risk Policy" for the product.
Replacing the RPN article very well done
Bill; you have done some extensive research into the different approaches to risk for this article. I can tell you put a lot of work into providing your readers with good information. Thank you.
Priority Medium
“Priority-Medium,” action to improve prevention and/or detection controls (or justification on why current controls are adequate) SHOULD be taken.
What could be the criterion for taken action, why some of them you take action, and for another no? What criteria to use behind these words SHOULD? When is must and when is NO in this case, is not very clear to me.
Thank you!
Risk Priority
DD2977, Deliberate Risk Assessment Worksheet, presents only the ratings, and not what criterion should be used to make action mandatory. The ratings, like RPNs, allow the organization to prioritize the activities. Action must obviously be taken on Extremely High and High risks, and the corresponding principle for FMEA, that action must be taken on 9 and 10 severity failure modes--the "legal zone" defined by Harpster--suggests that action must be taken on a Medium risk that comes from a Catastrophic severity and an Unlikely probability rating (just as an RPN from Severity 10, Occurrence 2, and Detection 1, for a total of 40, would require attention). In any event, a Medium risk rating would take priority over a Low one, noting especially that no Catastrophic failure mode can get a Low rating.
Add new comment