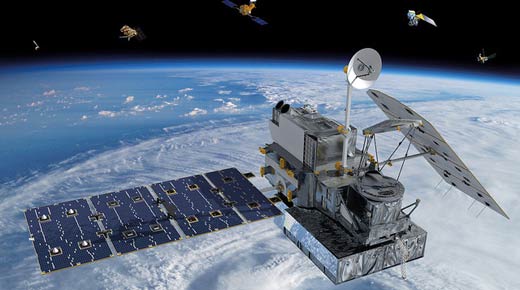
Understanding measurement risk can mean the difference between a successful mission or a failed one
Credit: NASA Goddard Space Flight Center
Imagine that a satellite is launched into space and communications are intermittent. This happens because the satellite is wobbling, which causes connection problems in the receiver. The cause of the wobbling is identified: It is the result of not using a calibration provider with a low enough uncertainty.
ADVERTISEMENT |
The load cells used to measure the amount of fuel stored in the satellite must be almost perfect. However, if a calibration provider doesn’t have the right measurement capability, the load cells won’t be accurate enough to make the measurement. In this case, the result is a wobbling satellite and significant resources needed to fix the problem.
…
Comments
The graphs suggest a commercial program for the calculations.
Is there a commercial program to automate the calculations and present the graphics you depict in the article?
Commercial software
Stanley
Take a look at Minitab. It should be useful for this type of data gathering and presentation.
Add new comment