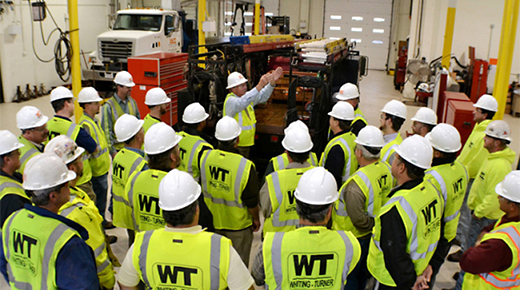
A job safety analysis (JSA) worksheet is almost identical in organization to a job breakdown sheet and standard work, all of which assess a job (or process) on a step-by-step basis. This suggests combining standard work with job safety analysis to support ISO 45001.
ADVERTISEMENT |
The concept can be carried even further by adding quality to support ISO 9001, and environmental considerations to support ISO 14001. The result is a comprehensive process assessment worksheet (CPAW) that empowers workers who are most familiar with the job to identify risks and opportunities, and recommend improvements. This article will focus primarily on the recently released ISO 45001 standard due to its role in occupational health and safety (OHS).
…
Comments
Best article on safety 45001 Ive seen yet
Hi William. Great article and very good breakdown of the new ISO 45001 standard which we (and I suspect many others) have begun working with. We consult for companies wanting this standard as part of their IMS. I like that your first big emphasis was on worker consultation as this is vital to genuine success. Please keep sharing, it seems Quality Digest has a wealth of good knoweldge amonsgts its writers.
Thanks
Add new comment