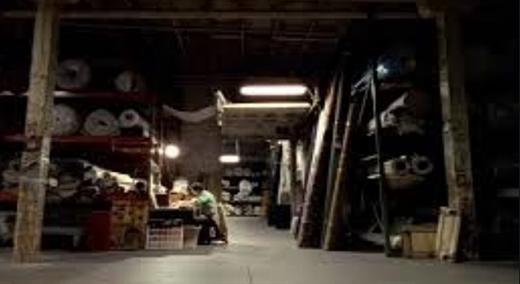
Several years ago, I was asked to address a startup meeting at a new client, a large manufacturer of medical devices. The company was resource-rich, but after several years of trying had not yet gained significant traction with its lean efforts.
ADVERTISEMENT |
There were perhaps 40 people in the room, half from line management and half from the company’s continuous improvement staff. I addressed the group, first describing my organization, GBMP, and then sharing a little bit about my previous experience as an operating manager. Specifically, I described the challenge to shift from a bounded thinkers vs. doers paradigm to one where every employee is a thinker-doer. (GBMP’s slogan, Everybody Everyday, is derived from that experience.) “Managers can’t take on this lean challenge all by yourselves,” I cautioned my audience. “There’s just too much to be done. It’s crushing to have just a few problem solvers.”
…
Comments
Thinker-Doers: spot on
Bruce, your ariticle was spot on. THANK YOU! “The best improvement ideas actually come from the people who do the work.” This is the truest statement in all my 40 working years in manufacturing and business. I am a six sigma master black belt. I have worked on process improvement most of my engineering career. I learned this lesson right at the beginning and it has served me well every time. It is so simple, and yet held in such disbelief and denial by most, except, of course, by the people who actually do the work. Listen to those people, then go figure it out with the data, the tools, etc. They just gave you the answer, somewhere in everything they said. I will add one more thing. Look for the person who is very quiet. Most of the time, that is the person who knows something even more, that hasn't been said yet. Respect them enough to ask. Process improvement at its finest and most effective starts with and capitalizes on “The best improvement ideas actually come from the people who do the work.”
Dr. Barney Fife?
Without a VP title or a PHD to feed his ego, that skeptic might have been more open to "radical" ideas. "Not Invented Here" syndrome is bad enough, but by presenting him with the idea that "a worker" might have something of value to bring to the table, something he or his empire had not thought of, you were threatening his self image. Perhaps even threatening his sense of security. I suspect that this person, having amassed his staff of SME's, was lobbying for even more, along with other additional support. Unfortunately, one comes across this type all too often and, equally unfortunately, the organization does not determine the real story for a long time, if ever.
Thinker-Doer Language of Influence
Research into motivation patterns has shown that Thinkers are about 40% of the population; Doers are about 40% as well. 20% can do both.
Doers don't take much motivation. Their motto is "Just do it."
Thinkers have to analyze everything before deciding. Influencing language for Thinkers would sound like this: "Haven't you waited long enough to get started on this or are you going to wait until it's too late?"
For this VP of QI, we might say:
"As you may know, the eighth speed bump of Lean is unused employee creativity.
Haven't you waited long enough to start using the wealth of employee wisdom available to accelerate performance, or are you going to keep waiting for some magical high idea to come along?"
To learn more about the language of influence, download my free Motivate Everyone Quick Reference Card. I have found these language skills invaluable when wrangling improvement teams and their leaders.
Doers are important
I recall that Tom Peters wrote that the person who does the job knows more about it than anybody else. Henry Ford credited his hourly workers with many, if not most, of his workplace productivity improvements. The ECR (Error Cause Removal) program relies on front-line workers to identify potential quality problems and, by implication, muda or waste. The phrase "Thinker-Doer" sums up this important concept in 2 words.
Add new comment