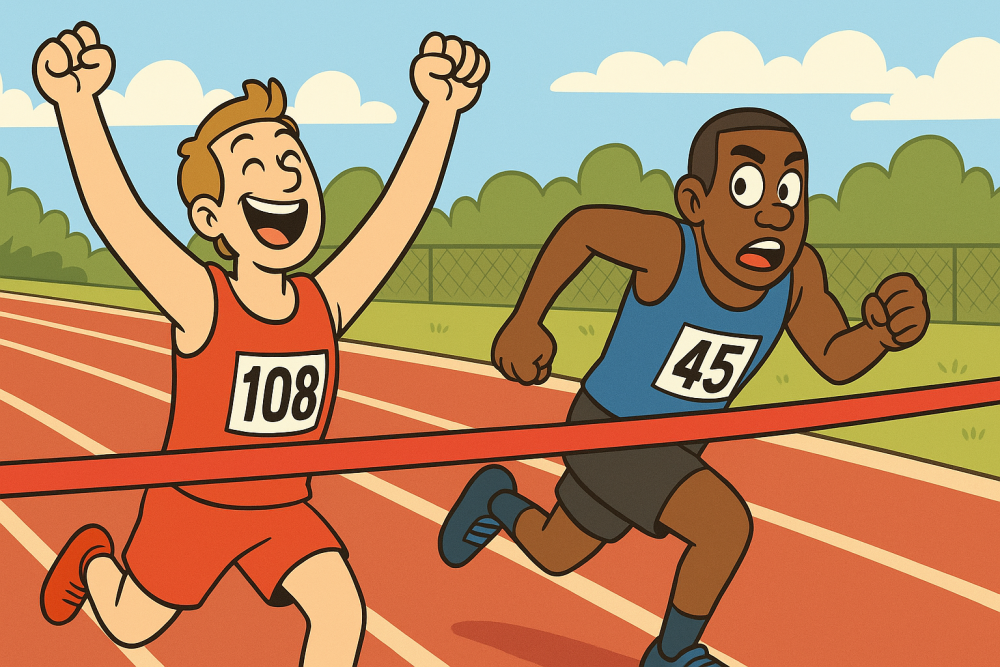
The level of excitement was high in our machine shop as we drew closer to our goal of less than 9-minute changeovers on the BNC lathe. (See Part One of this story for how we got there.) Setup improvements had so far reduced changeover time to 20 minutes, cutting the economic order quantity from weeks to days of stock on hand.
Our pull system now more closely resembled a supermarket with several containers on hand for each of the 66 parts in our pilot. After decades of viewing setups as a problem and inventory as a protection from stockouts, this new process was still confounding for many persons. But it was working, which was most apparent to the operators on the BNC and their internal customers in assembly:
• No more expedites and angry demands
• No more breaking down a setup in mid run to run a hot part
• No more juggling jobs between machines
• No more fiddling with tools and programs to get a good part
…
Add new comment