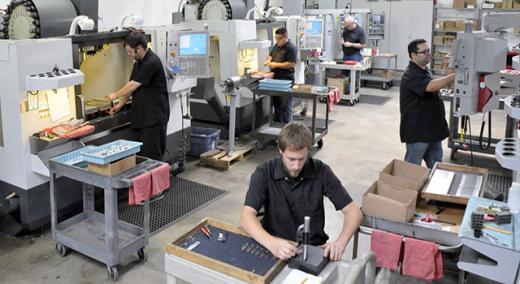
We had been working with the Toyota Production System Support Center (TSSC) for two years to build a model line in our assembly department. As we moved from small batch production to one-by-one, the results had been astounding: Customer lead time reduced from two weeks to one day, crew size cut in half, and overtime reduced from 40 hours per week to 10. Hundreds of small changes made by assemblers to the assembly process had made this possible. Everybody every day, GBMP’s slogan, was born from that experience.
ADVERTISEMENT |
Now it was time to move upstream from assembly to our internal supplier, machining, a resource that despite efforts to improve was still overproducing and delivering late. Setups on our CNC lathes averaged 90 minutes despite an improvement project supported by graduate engineers from a notable Massachusetts engineering school.
…
Add new comment