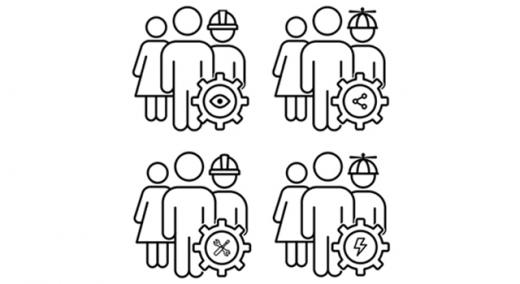
No matter who you are or what you do, you create systems and live in the systems of others every day. But for some reason, we’re never actually taught lean systems thinking. We think it is natural, that we just sort of “get it.”
ADVERTISEMENT |
On a personal level, we are most often governed by cognitive biases... more than 250 documented “shortcuts” our brains take to interpret and respond to the world around us. They, themselves, are systems, and they respond to stimuli in our world (which are generated by, you guessed it, more systems).
![]() |
It’s a soup, but it’s a soup of patterns.
…
Add new comment