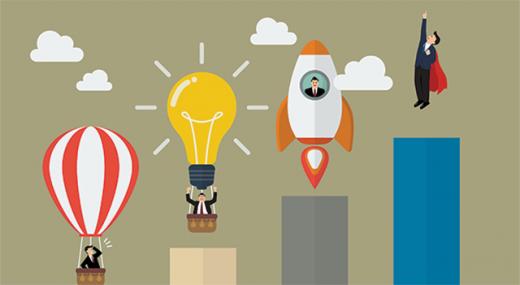
Shortly after a recent post, in which I referred to sowing the seeds of change, I enlisted the help of my son, Ben, to reseed a particularly bare area of our yard. I’d neglected this spot for a few years, and it had become sparse and dormant.
ADVERTISEMENT |
Fixing the problem was therefore not merely a matter of spreading new seed. There was a significant amount of work to be done first to prepare the soil. This essentially exposed the problem and at the same time made it amenable to improvement. Had I just sown seed on the thatch and weeds that had infested the grass, the results would have been disappointing. A seed or two might have taken root, but most would have languished.
…
Add new comment