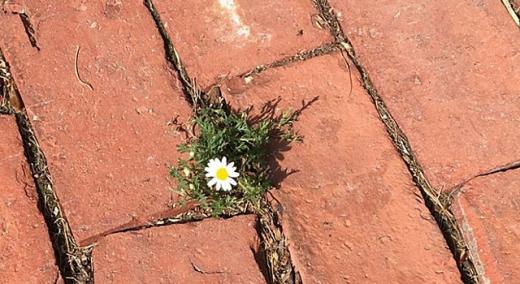
A daisy rising from my brick walkway reminded me this morning, that even in the worst environment, there is a chance for growth. But this kind of individual heroism does not portend success for lean transformation. As an organization with the slogan “Everybody Everyday,” GBMP places high value on total employee involvement as an essential piece of continuous improvement.
ADVERTISEMENT |
I have a long-standing practice of asking managers, “What percent of your employees come to work every day, excited about a potential solution to a problem or an idea for improvement?”
…
Add new comment