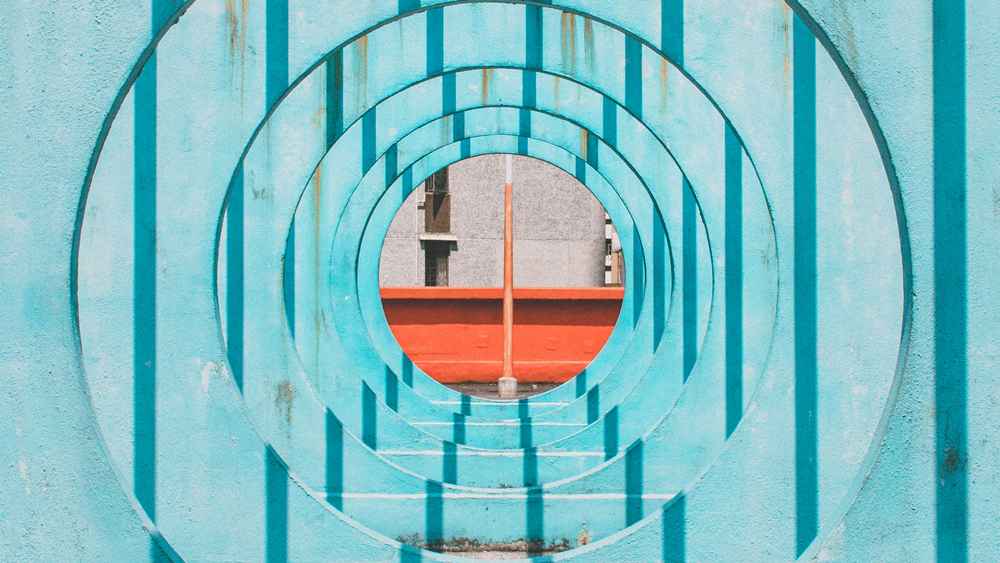
Photo by Joel Fulgencio on Unsplash
Most quality practitioners are familiar with the Taguchi loss function, which contends that the cost of any deviation from the nominal follows a quadratic model. This is in contrast to the traditional goalpost model, where anything inside the specification limits is good, and anything outside them is bad.
ADVERTISEMENT |
This article will show where the quadratic loss model came from, its use to optimize the economic safety factor, and its extensive limitations. The Taguchi model is in fact a one-size-fits-all model for applications in which we lack probabilistic models for the quality characteristic in question. The Taguchi loss function is overly pessimistic in the absence of substantial variation, and its use may lead to excessive costs. Here we address only the nominal-is-best situation.
…
Comments
It's nice to see the Taguchi…
It's nice to see the Taguchi loss function discussed again. Don Wheeler wrote extensively on this subject; I highly recommend The Process Evaluation Handbook. It discusses not only the quadratic loss function, but several other loss functions that are common in manufacturing and service; and has tables for calculating loss.
When I first attended Wheeler's Advanced Topics seminar, one of the exercises we did was estimating the Taguchi loss from one segment of the Japanese Control Chart record. This was a process operating well within the specs (CPk>2), but had a run where the process center shifted off nominal for a period of time. The entire class gasped when we came up with the final number. I don't remember what the number was, but it was in the thousands of dollars.
I do disagree with the statement that "tolerance stack-up shouldn't be an issue for in-specification parts." This is the thinking that caused U. S. auto manufacturers to lose out to the Japanese manufacturers for years until Deming, Wheeler and others taught them the error of their ways. That Batavia transmission study was a shock to Ford. When they went to gage the IDs in the valve body, the Japanese transmissions were so good that the inspector thought his gage must be off. He tried a second one, which was identical to the first...now he knew his gage was broken. He called a gage repairman, who came and verified that the gage was working and calibrated. The inspector checked the rest of the sample (10 valve bodies altogether), and they all looked identical and nearly perfect. This was when Ford finally had to admit that they had no idea how the Japanese were able to build the parts so much better. As one Ford executive put it, "While we were working hard to make all the parts in spec, they were working to make them all identical."
I worked at Ford in the 70s, and can tell you from personal experience that tolerance stack can matter a great deal. It was common practice in the production shops then to set up the machines at the high end of the spec. We knew it would take about an hour for tool wear to allow the parts to drift down to the lower end of the spec; we would check and adjust to bring the readings back up, then let it drift. We knew nothing at the time about SPC or Taguchi, but we did get curious one day about the tolerances. I happened to be working in an area that ground IDs on a circular part that also had an OD. We wondered, "What if our ID was as wide as it could be (still in spec), and the OD was as small as it could be? What if the part that fits inside it had an OD that was as small as it could be, and the part that our part fits inside had an ID that was as wide as it could be?" Pure tolerance stack-up.
So we tried it. The subassembly sounded like a washing machine full of bolts, and seized up after just about 40 seconds.
Add new comment