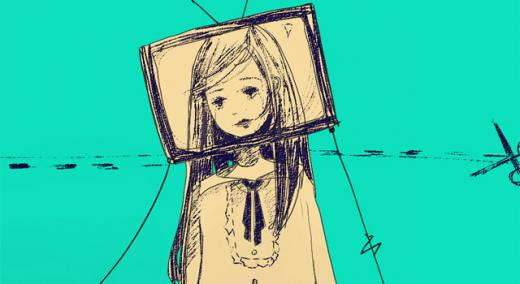
Despite the life science industry’s infatuation with modernity and trend chasing, even its most forward-thinking organizations have struggled to fully digitize and integrate their operations.
ADVERTISEMENT |
Yet, while the industry lags behind most other sectors in implementing business-streamlining digital technologies, many shrewd life science companies are working to close the digital gap so they can capitalize on the competitive advantages digitization affords.
As digital initiatives gain more traction, and as advanced technologies increasingly perform more of our mundane tasks, skilled life science professionals’ fears about job displacement are intensifying. Their digital apprehensions are undeniably intertwined with the global workforce’s general anxieties about automation, as highlighted in a 2017 PwC survey that reports 37 percent of the world’s workers are worried about eventually losing their jobs to automation. The unease is worsening, it seems, as only 33 percent of workers reported concerns about job-eradicating automation in the same survey in 2014.
…
Add new comment