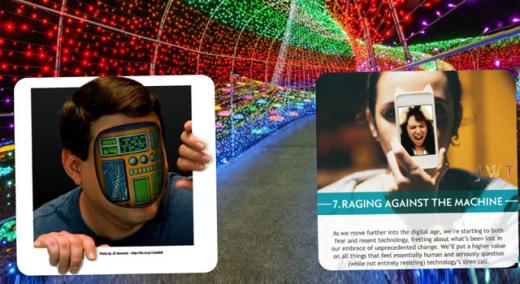
Credit: Gerd Leonhard
It’s human nature to resist change, and the life sciences industry is not exempt from a change-averse mindset. The proof: Life science organizations (LSOs) lag far behind counterparts in other sectors in implementing digital technologies that are designed to streamline business and manufacturing processes.
ADVERTISEMENT |
In fact, while the rest of the world continually vies for digital differentiators, only 21 percent of LSOs even view digital disruption as a potential threat, according to PwC’s most recent Digital IQ survey. The causes of LSOs’ digitization reluctance are abundant and legitimate—security, cost, data integrity and validation concerns are just a few—but fears about regulatory compliance are usually at the top of that list.
…
Comments
Very insightful! Sadly,
Very insightful! Sadly, what's holding most LSO's back from automation, is analysis by paralysis... and they will lose to their competition who breaks through that.
Add new comment