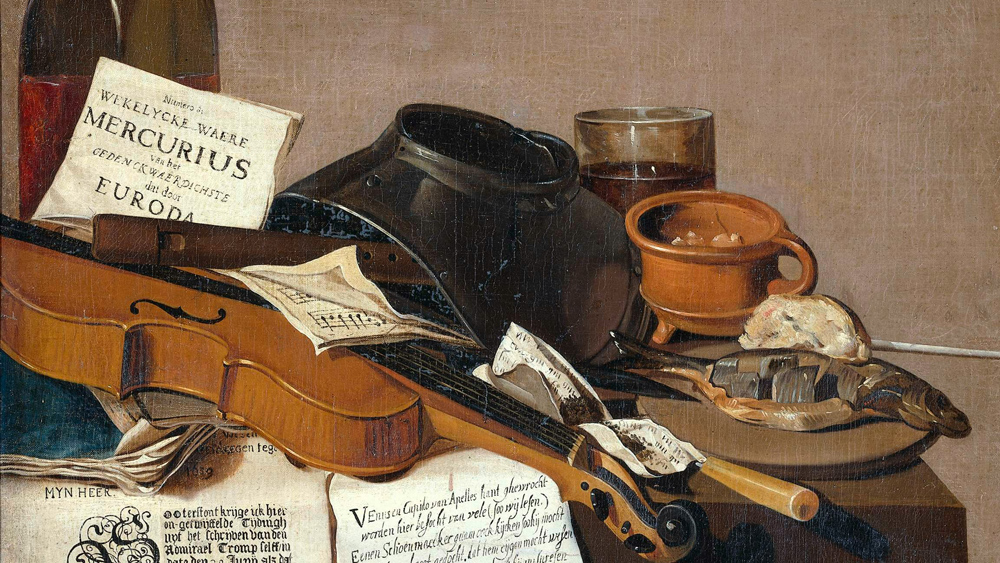
There’s perhaps no better reputation for quality than Stradivarius. As I’ve learned from Wikipedia, a Stradivarius is a violin or other stringed instrument “built by members of the Italian family Stradivari, particularly Antonio Stradivari (Latin: Antonius Stradivarius), during the 17th and 18th centuries.” The quality of these violins’ sound is legendary and widely believed by many to be unequalled to this day. (Wikipedia does cite some studies that show certain other instruments, including some recent ones, are in fact equals to Stradivarius sound quality, but the Stradivarius reputation remains undiminished.)
ADVERTISEMENT |
It’s not an exaggeration to suggest that most organizations today would be honored to be rated alongside Stradivarius. Do you know of any that are? I can’t think of any.
That’s quite a high bar. We should be able to learn from it, including perhaps why more than three centuries of successors apparently have been unable to replicate let alone surpass Stradivarius’ quality.
…
Comments
Stradivarius had variations
I recently attended a concert in Austin, Texas, in which a 1666 Stradivarius violin was played by violinist Soojin Han. In a pre-concert talk, she stated that she tried three different Stradivarius instruments all made from the same tree. She said they all sounded different, but she selected the one that fit her best and had the sound she liked. Stradivari would have had to evaluate the instruments by playing them or perhaps he had other means to tune them by ear. Modern techniques might mechanically vibrate the violin and look at a frequency spectrum recorded by microphones to determine what makes the violin most pleasing to the ear. I would guess that such methods might lead to more consistency than Stradivari himself was able to accomplish.
Craftmen are native-quality makers
For hundreds of thousands of years, quality has been carried by craftsmen. Craftsmen have quality as their mother tongue. They have studied for a long time, and know their profession "on the tip of their fingers". It was Taylor, by entrusting the work to workers with limited competence, who invented the quality controller position. And that’s when the situation got worse.
That’s the beauty of it.
Thank you for your article, Mr. Goldsmith.
In response to a comment from Mike re: “more consistency than Stradivari himself was able to accomplish”. I would argue that that was the beauty of it: uniformity of output was never high on a craftsman’s priority list! Each piece of output was unique. I also support Hubert BAZIN in his/her argument that Taylor was the assassin of craftsmanship. True, you need uniformity for your nuts and bolts, and most certainly for your guns and bullets. But a musical instrument is more of a work of art than a casting from a mould. You may wish to check out my article in the QD titled “Garvin’s Eight Dimensions of Product Quality Applied to Luxury Items” at https://www.qualitydigest.com/inside/quality-insider-column/garvin-s-eight-dimensions-product-quality-applied-luxury-items-100923
Please take a look at the part called Conformance dedicated to… Steinway piano vs Yamaha. I hope you enjoy it.
Thanks again.
Yours,
Andrey
Luxury
Thank you for your comments and reference to your excellent interesting article. It’s hard to know the extent to which Stradivarius instruments were considered luxury at the time of their creation, but they certainly are now. Similarly, it’s hard to know how much their durability was recognized at the time; but their reputation is that after hundreds of years they still sound better than instruments made today—presumably including even the poorest-performing extant Stradivarius instrument. No doubt, part of the prices they command is due to branding and people knowing how much they cost.
Re: luxury
Dear Mr. Goldsmith. Thank you for your comment and for taking interest in my article. Indeed, it is interesting to observe how objects gain value over time and become a 'luxury' today, when back in the day they may well have been just fit for purpose. Has got to do with both reputation and rarity for sure.
Add new comment