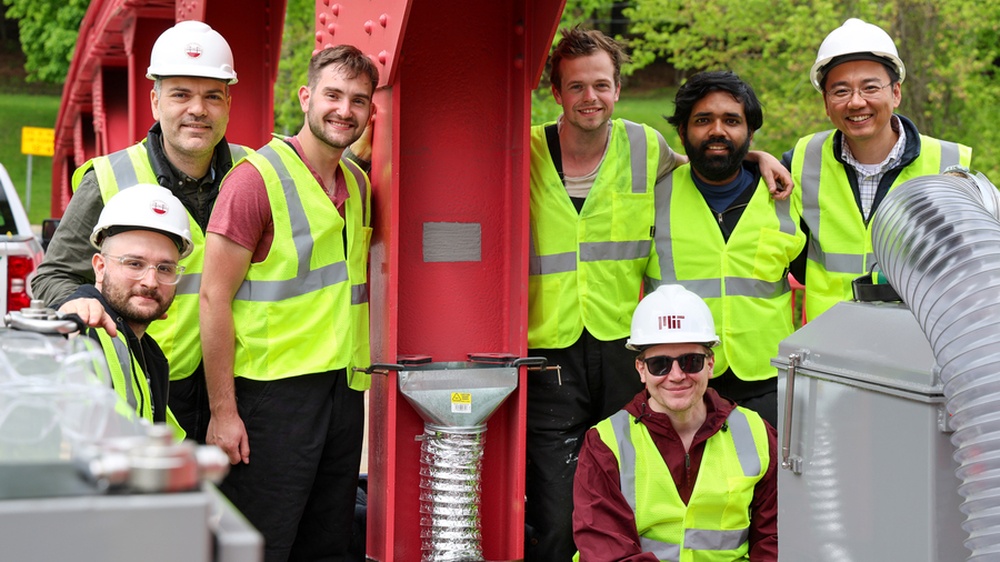
Alexia Cota / UMass Amherst
Members of the UMass Amherst and MIT research team pose next to the 3D-printed patch. Haden Quinlan (front, kneeling) of the Center for Advanced Production Technologies at MIT, is one of the researchers leading MIT’s efforts on the project.
More than half of the nation’s 623,218 bridges are showing significant deterioration. Through an in-field case study conducted in western Massachusetts, a team led by the University of Massachusetts at Amherst—in collaboration with researchers from the MIT Department of Mechanical Engineering (MechE)—has just successfully demonstrated that 3D printing may provide a cost-effective, minimally disruptive solution.
ADVERTISEMENT |
“Anytime you drive, you go under or over a corroded bridge,” says Simos Gerasimidis, associate professor of civil and environmental engineering at UMass Amherst and former visiting professor in the Department of Civil and Environmental Engineering at MIT, in a press release. “They are everywhere. It’s impossible to avoid, and their condition often shows significant deterioration. We know the numbers.”
…
Add new comment