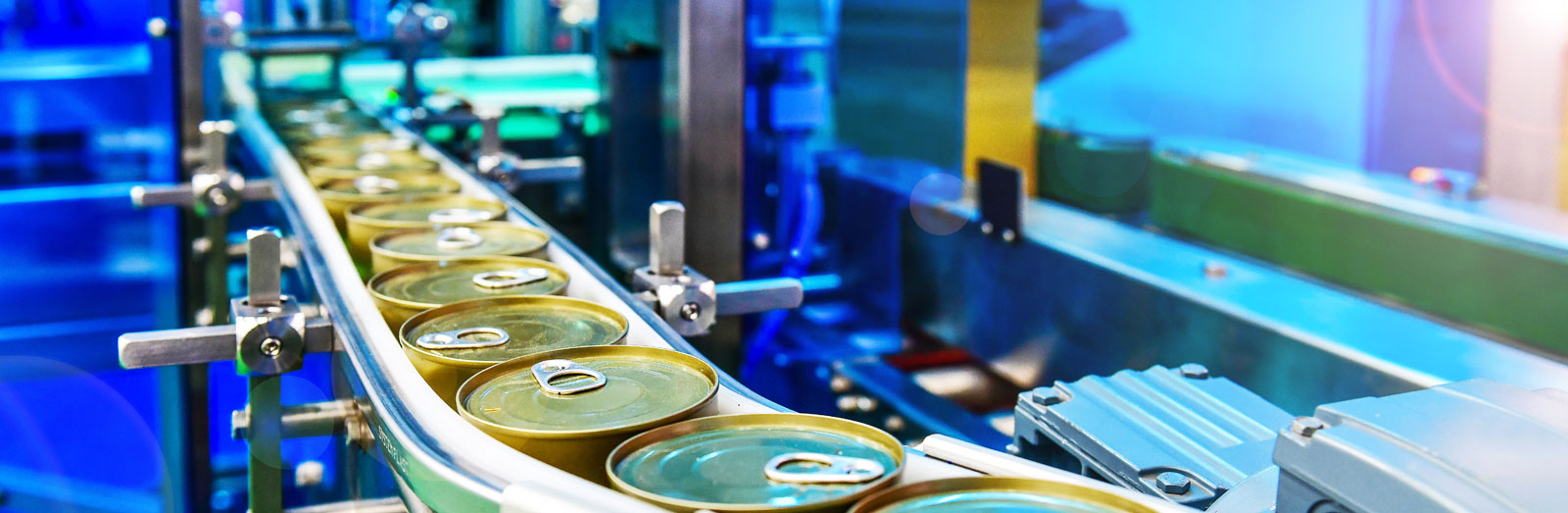
If you're involved in business you know: Strategy matters. Your strategies guide you to reach your objectives. Behind every successful business are purposeful strategies. Then again, as Alvin Toffler said, “The absence of strategy is fine if you don’t care where you’re going.”
We’re talking specifically about data-driven strategies like using “improving operational efficiency” to support a goal of increasing your profit margin. Or “improving product standardization” to increase international market share. The question is, how do you support your data-driven strategies? Where do your data come from?
Many leaders don’t realize they are probably sitting on a gold mine of data just waiting to be transformed into actionable information to support their strategies. I’m talking about the quality control data that are collected every day on the shop floor.
Standard operating procedure usually dictates that shop-floor data are used for quality control—and that’s about it. The data are used to consistently produce high-quality products. However, as quality becomes increasingly expected by customers—and achieved by many manufacturers—this former gold standard of organizational excellence is no longer enough of a differentiator to safeguard your market share. You will need to adopt additional strategies to stay relevant and profitable.
Using shop-floor data to support strategic initiatives
We can see the main difference between tactical and strategic data gathering this way: Tactical data are gathered at the shop floor and become input for control purposes; those same data are aggregated to become input for decisions that affect overarching strategic goals. By doing that, you step into the strategic level of business, where improvements involve loss or gain on orders of magnitude. Hundreds of thousands of dollars vs. tens of thousands, millions vs. hundreds of thousands.
“The absence of strategy is fine if you don’t care where you’re going.”
—Alvin Toffler, author of Future Shock (Random House Publishing, 1970)
Imagine a company is using digital SPC on the shop floor to monitor min-max product fill to meet quality control standards. The data reflect effectiveness of line equipment and employees. The data are used to verify if product is meeting tolerances, and then they are stored away. All well and good, but....
Are there multiple shifts, production lines, and facilities? With a robust enterprisewide SPC software, multiple data sets can be aggregated and mined to expose profit-eating trends. There are savings to be had by actioning those data-cum-information.
Figure 1: Tactics and strategy are intimately linked
At a strictly tactical level, data almost exist in a bubble. Shop-floor data collection is always relevant to its own little world and serves the purpose of quality control just fine. But as soon as your organization has more than one shift or production line, it becomes imperative that the terminology of each data set match. Data collected on the shop floor must be standardized to meet companywide goals for analysis. Why? Because the more complex your operation is, the more potential there is for leaving money on the floor due to missed opportunities for enterprisewide process improvement. An enterprisewide SPC platform is the tool of choice to help organizations collect and standardize data in a timely fashion.
“Strategy without tactics is the slowest route to victory. Tactics without strategy is the noise before defeat.”
—Sun Tzu, ancient Chinese military strategist
Employing an enterprisewide SPC platform is the key to unlock the power and potential of the data you already collect. This is how different departments and levels within your organization can plot and visualize data to help you make informed decisions. This is also perhaps the only way for an organization to align all levels of business activities to achieve company goals.
Follow along with us in the next few articles in this series as we make the case for bringing advanced enterprisewide software to the shop floor. After that we’ll look at a case study that explains how one company effectively used its data at multiple levels within the organization to prioritize cost-saving improvement strategies.
Add new comment