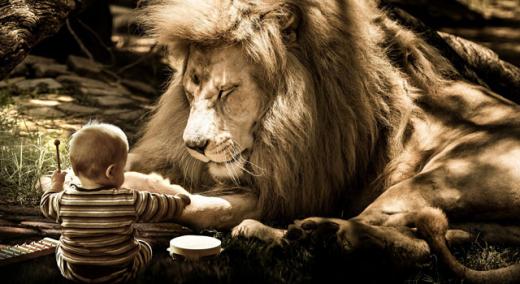
The Pareto principle calls for focus on the vital few rather than the trivial many. While none of ISO 9001’s clauses are trivial—a nonconformance for any of them requires corrective action—ISO 9001 users can avoid most nonconformances by focusing on the clauses that are the most frequent trouble sources, and also on what look like frequent common root causes for most of the nonconformances.
ADVERTISEMENT |
Penny Ouellette at Orion Registrar provided a valuable service by identifying the clauses in question.1 The following information is based on nonconformance reports (NCRs) collected by the ANSI National Accreditation Board (ANAB), as accumulated roughly halfway into the transition from ISO 9001:2008 to ISO 9001:2015. The NCRs were written against the following sections of the standard.
4.4.1 Quality management system and its processes
7.2 Competence
8.4.1 Control of externally provided processes, products, and services
9.1.2 Customer satisfaction
9.2.1 Internal audit
9.3.2 Management review inputs
…
Add new comment