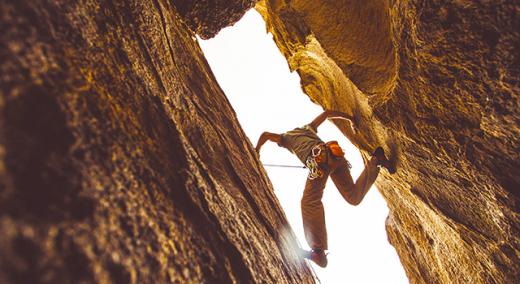
Body
In my article, “Tightened 100% Inspection” (Quality Digest, March 29, 2021), we found that the excess costs associated with tightened specification limits are generally prohibitive. Here we consider the question: “Under what conditions can we use tightened specifications without incurring undue excess costs?”
…
Want to continue?
Log in or create a FREE account.
By logging in you agree to receive communication from Quality Digest.
Privacy Policy.
Add new comment