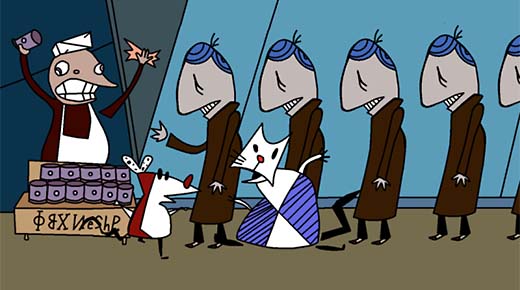
“All animals are equal, but some animals are more equal than others.”
—George Orwell
The famous quote from George Orwell’s political allegory, Animal Farm, occurred to me recently as I listened to a design engineer explain to me how he was taught in college that engineers have a special responsibility to help their less able coworkers. Not intending to single out engineers or generalize from one data point, this example demonstrates what I observe to be a longstanding preoccupation with degrees, certificates, and belts. We may refer to employees on the front line as “value-adding,” but too often it’s the ones with letters after their names that we actually value.
ADVERTISEMENT |
In 1957, Peter Drucker dubbed the latter group knowledge workers, “high-level employees who apply theoretical and analytical knowledge, acquired through formal education,” thereby inadvertently differentiating the thinkers from the doers, the high level from the low level, the brain trust from the variable expense.
…
Comments
Status
One of my first managers opined that consultants made their money by coming into the plant, interviewing the workers as to how to fix problems and improve the operation, putting those answers into a buzz word laden document (in an impressive binder) and writing an invoice for six figures (at least).
I took that to heart and later made my reputation as a problem solver by asking the front line worker, "Hey man, what's the problem with this operation?" Once the "grunts" realized that "people" were listening to me, I became the recipient of many great unsolicited ideas. Synergy at its best!
Add new comment