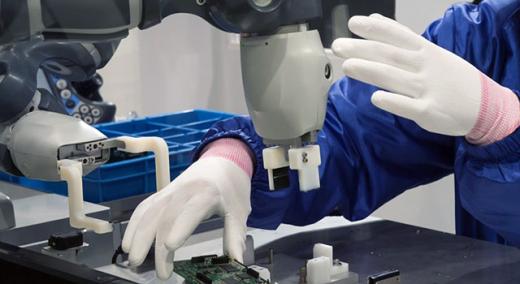
One of the most significant developments of potential interest to small and medium-sized manufacturers in the area of industrial robots is the introduction about 10 years or so ago of a subset of industrial robots called collaborative robots or “cobots.”
ADVERTISEMENT |
What makes them different from standard industrial robots is that cobots are specifically designed to be safely used around people. Why is this significant? Well, industrial robots, as high-tech as they might appear, are actually dumb. They will move to the place and at the speed that they have been programmed to achieve, but if a person happens to get in the way on the way to their destination, look out! Because standard industrial robots are designed for high speed, and they run off of high voltage (typically 220V AC) , they can be dangerous. Think of the last time that you saw the image of an industrial robot in an actual manufacturing setting. Why do you think they are normally situated in cages or behind guarding?
…
Add new comment