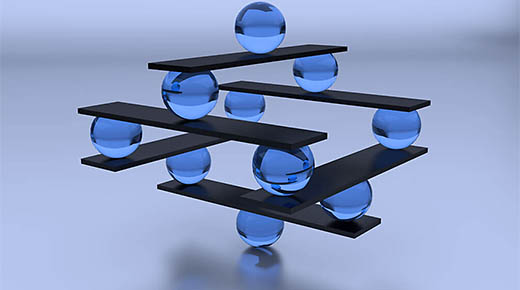
When Philip Crosby announced zero defects as a philosophy during the 1970s, it was met with incredulity. There were already many articles written on the fallacy of such a strategy and the enormous costs of moving toward zero defects. Fast forward 40+ years, and zero defects has become a reality.
ADVERTISEMENT |
The automotive and semiconductor/high-tech industries that we have worked with have achieved this strategy over a 30-year time period. The strategies to shift organizations that were at 20,000 to 50,000 defective parts per million (PPM) during the late 1980s to 1,000 PPM to 100 PPM and even parts per billion are now quite straightforward. Let us understand how this is done.
New-product development, defect prevention, and FMEA
Quality improvement and defect prevention start with a disciplined, new-product development process that includes phase gates. Most important, three tools are key to overall success:
1. Failure mode and effects analysis (FMEA) that is used with design and processes
2. Design for manufacturing (DFM) and design for assembly (DFA)
3. Upfront involvement of manufacturing in design
…
Add new comment