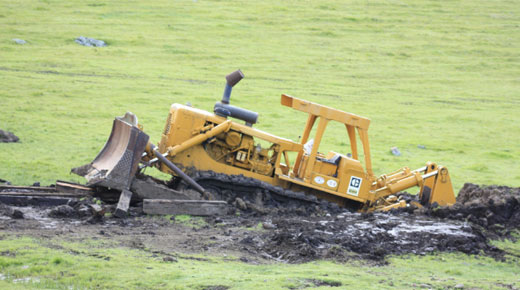
Reliability activities serve one purpose: to support better decision making. That is all they do. Reliability work may reveal design weaknesses, which we can decide to address. Reliability work may estimate the longevity of a device, allowing decisions when compared to objectives for reliability.
ADVERTISEMENT |
Creating a report that no one reads is not the purpose of reliability. Running a test or analysis to simply “do reliability” is not helpful to anyone. Anything with MTBF (mean time between failures) involved... well, you know how I feel about that.
The Type III error
A common problem in engineering work is the desire to solve the wrong problem. I know I am guilty of working on the issues that hold my interest rather than on the challenges requiring action. A Type III error is when you solve the wrong problem.
We only have so much time and resources for reliability work. There are plenty of challenges and interesting aspects of sorting out the reliability of a system. However. it is the focus on solving the right problems that matter. It is solving the right issues that provide value to the team and organization.
…
Comments
Decision Making
"Far better an approximate answer to the right question, which is often vague, than an exact answer to the wrong question, which can always be made precise." John Tukey
Add new comment