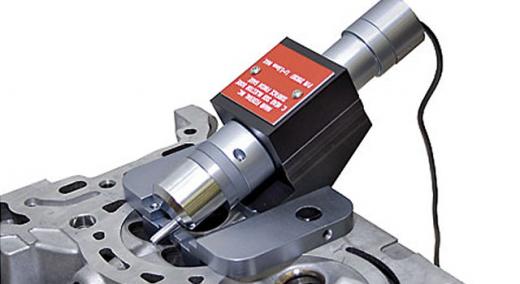
Before a fixture gauge is designed, the engineer must understand what specifications must be inspected. In many respects, the gauge’s design reflects not only the design of the part but also the manufacturing processes that produced it.
ADVERTISEMENT |
Machinists must establish datums in order to machine a part accurately, and gauge designers often need to know what those datums are in order to position the part repeatably relative to the gauge head or other sensitive device. Sounds simple and straightforward, but that is not always the case.
Sometimes the parts are so large that they cannot easily be brought to the gauge, and a special arrangement might be required to bring the gauge to a section of the part. Other times, the part is so small that it seems impossible to get to the dimension that must be measured. Gauge designers are always amused when a part print—that comes in at 10 times the normal size—refers to a small land at the bottom of the bore. At 10 times the size, it looks pretty simple, although in reality it may be impossible to measure.
This is when good fixture design comes into play to ensure the measurement can be made in a way that is easy for the operator to make, and to produce repeatable and accurate results.
…
Add new comment